Around 1.6 billion people don’t have adequate shelter. Due to the global pandemic, every nation is expected to struggle with affordable and safe housing in the near future.
Groundbreaking tech companies are now doing what was once thought to be impossible, providing cost-effective shelter. They use 3D printing, engineered materials, and robotics to build houses quickly while saving money. We’re in the early days of 3D building homes and the technology is now available for builders and contractors.
Kevin May, President at LandHub says, “When the industry matures, we believe we’ll witness a completely new world of housing. These homes aren’t only for the poor — everyone will benefit.”
What exactly are 3D printed houses?
3D printed homes are built using the process called “additive manufacturing.” This process builds the house’s structure layer upon layer utilizing a unique concrete printer.
The printers are robotic, similar to those used in the automotive industry. They have a nozzle on a robotic arm or a crane that dispenses the concrete in a pre-planned pattern. Some use a support arm moving back and forth on rails while it pumps out concrete.
Can 3D printers build a complete house?
Most 3D printed homes require the hands-on support of people who are training in the technology. The technicians constantly monitor the progress, checking the concrete levels and the finishes.
3D printers can build the foundation, exterior, and interior walls (i.e. the structure’s structure).
3D printers cannot make a building habitable; when they will truly revolutionize the construction industry. Currently, they don’t install or create all the finishes and services. The construction workers install windows, doors, heating, cooling, plumbing, and interior fixtures and decor. However, we’re optimistic that technology will advance and these things could be completed by robotics in the future.
Materials of 3D printed homes
Mostly, 3D printed homes are built of concrete, but one Italian company uses natural fibers, rice waste, and raw earth to construct homes. They use any natural resources they can find at the locations where they build. They believe this “bio cement” is better for our environment and makes the process more affordable.
Some companies are even experimenting with bioplastic and terra-cotta bricks. They aim to offer more affordable homes to both undeveloped and industrialized countries.
When are the 3D printed houses ready?
The timeline depends on house size. Many companies can build a 3D house in 1 to 3 days. The small houses (less than 650 square feet) can be printed in less than a day. It takes three days if the homes are about 2,000 square feet.
This estimated time is for 3D printing the exterior and interior walls. You know that you’d need additional time to finish your house. You’d need to add windows, doors, fixtures, plumbing, cooling, heating, and electrical.
Advantages of constructing 3D homes
- Faster construction: The home’s walls and foundation will be built in a few days.
- Reduced labor: With 3D concrete printing, companies hire a few people to monitor the 3D printer.
- More affordable: ICON, a 3D printer manufacturer, says home construction cost is reduced by 10% to 50%.
- Less waste: People don’t have to carve or cut materials to make the house, so this type of construction is less wasteful. 3D printers only use the amount of material that you need to finish the home.
- More endurable: Reinforced concrete is a stronger material for the areas disposed to natural disasters. Most shelter and safe rooms are built with reinforced concrete since it’s unaffected by high wind, fire, pest, and mold.
- Endless design possibilities: 3D printed houses are a completely new world for architects.
Final thoughts
3D homes could become a concrete reality and save a global housing crisis. Darren Robertson of Northern Virginia Home Pro told us that, across America, the cost of housing has far outpaced increases in salaries, so much so, that property prices are growing at twice the rate of wages.
Similarly, the Major Challenge of Inadequate U.S. Housing Supply recently estimated that 2.5 million additional housing units will be needed to make up America’s housing shortage. 3D printing could simultaneously solve the housing affordability and shortage problem.
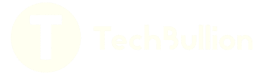