Material testing is the backbone of innovation in industries ranging from aerospace to construction, where materials’ integrity and reliability can determine the success or failure of entire projects. The precision with which materials are tested directly impacts product safety, performance, and durability, making accurate specimen preparation a key part of the testing process.
As technological advancements push the boundaries of what materials can do, the demand for more efficient and precise testing methods has never been higher. Traditional methods of specimen preparation often involve time-consuming processes and multiple machines, which can lead to inconsistencies and delays.
In response to this growing need, the ImpactMill CNC system by TensileMill CNC emerges as a groundbreaking solution. This innovative system offers unmatched capabilities in preparing both impact and flat tensile specimens, simplifying the process while guaranteeing compliance with the highest industry standards. By integrating advanced technology with a user-friendly design, ImpactMill CNC positions itself as a vital tool in material testing’s future.
A Dual-Function System for Enhanced Efficiency
The ImpactMill CNC is the world’s first hybrid system designed to prepare both impact and flat tensile specimens with exceptional accuracy and efficiency. In industries where time is money, this dual-functionality offers a significant advantage by eliminating the need for separate machines to perform each type of preparation. This not only reduces the overall footprint of equipment but also optimizes the testing process, making it more cost-effective and less labor-intensive.
At the core of the ImpactMill CNC’s functionality is the integration of TensileSoft™ design with a Fanuc controller, creating a user-friendly interface that even non-trained CNC machinists can operate easily. This intuitive design reduces the learning curve and allows companies to make use of their existing workforce without extensive training. The system’s capability to prepare up to eight samples in a single cycle further amplifies its efficiency, cutting preparation time by up to 90% per specimen. This dramatic reduction in preparation time enables testing facilities to increase throughput without compromising the quality of the specimens.
Moreover, the ImpactMill CNC is designed with operator convenience in mind. The system’s TM Fix Technology minimizes vibration and chatter during the preparation process, making sure that each specimen meets the required surface roughness and dimensional accuracy. This focus on precision not only increases the reliability of the testing results but also extends the lifespan of the machine by reducing wear and tear on critical components. The ImpactMill CNC, therefore, represents a significant leap forward in specimen preparation technology, offering a comprehensive solution that addresses both the operational and quality control needs of modern material testing facilities.
Compliance and Precision: Meeting Industry Standards
When it comes to material testing, compliance with strict industry standards is non-negotiable, as the accuracy of test results depends on the precise preparation of specimens. The ImpactMill CNC excels in this area by making certain that each specimen it prepares meets the exacting requirements set by standards such as ASTM E23. This standard is extremely important for impact testing, particularly in industries where materials under stress must be validated in a rigorous manner.
What sets the ImpactMill CNC apart is its ability to achieve consistent and repeatable results across multiple specimens, a feature that is particularly valuable in high-stakes applications where even the slightest variation in specimen quality can lead to significant discrepancies in test outcomes. The system’s advanced engineering allows it to prepare specimens with surface roughness within the 25-40Ra range, which is well below the ASTM E23 threshold, providing perfect specimen preparation.
Furthermore, the ImpactMill CNC’s precision extends to its ability to handle different specimen sizes, including the most common dimensions used in Charpy and Izod impact tests. This versatility allows testing facilities to rely on a single machine for multiple testing scenarios, reducing the need for additional equipment and simplifying workflow. The system’s capacity to prepare up to eight specimens in one cycle not only saves time but also ensures that each specimen is prepared under identical conditions, enhancing the reliability of test results.
Flexibility and Advanced Features for Targeted Testing Needs
The ImpactMill CNC is more than just an innovative machine; it’s a comprehensive solution designed specifically to meet the specific needs of many industries where material testing is imperative. Industries such as aerospace, automotive, construction, and metallurgy can significantly benefit from the ImpactMill CNC due to its ability to handle both impact and flat tensile specimens with precision. Due to this, it is an important tool for companies that require consistent and reliable testing in order to ensure the safety and performance of their materials under different conditions.
For the aerospace and automotive industries, where material integrity can directly affect safety, the ImpactMill CNC provides the precision necessary to guarantee that all specimens meet stringent standards before being used in critical applications. Its capability to deliver accurate and repeatable results helps these industries maintain high quality control levels.
Construction companies, too, can benefit from the ImpactMill CNC, as it allows them to test a variety of materials used in infrastructure projects, from metals to composites. The ability to prepare both impact and tensile specimens on one machine simplifies the testing process, enabling more comprehensive evaluations without the need for multiple specialized tools.
Metallurgy labs, which often deal with a wide range of materials and require precise testing for research and development, will find the ImpactMill CNC invaluable. Its ability to prepare multiple specimens in one cycle means efficient testing, even when dealing with high volumes or complex testing requirements.
Overall, the ImpactMill CNC is ideally suited for industries that prioritize accuracy, productivity, and reliability when testing materials. With the integration of this advanced system into their workflows, companies can improve their testing capabilities, reduce operational costs, and improve the overall quality of their products.
ImpactMill CNC – Redefining Specimen Preparation in Material Testing
The ImpactMill CNC system is a transformative addition to the material testing industry, setting a new standard for efficiency, precision, and versatility in specimen preparation. By offering a dual-function capability that effectively integrates the preparation of both impact and flat tensile specimens, this machine addresses the growing demands of modern testing facilities with remarkable effectiveness.
Its compliance with stringent industry standards, such as ASTM E23, guarantees that each specimen is prepared to the highest quality, providing consistent and reliable results. The system’s advanced features, like TM Fix Technology and a user-friendly interface, further enhance its value, thereby allowing it to be used by different types of operators in a variety of testing environments.
ImpactMill CNC stands out as a pioneering solution that not only meets but exceeds the expectations of material testing professionals in a field where accuracy and efficiency are paramount. ImpactMill CNC simplifies the preparation process and delivers high-quality specimens, enabling laboratories to achieve more accurate and reliable test results, which ultimately drives innovation and excellence.
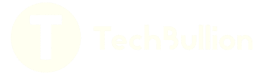