Manufacturing has come a long way from hand labor and crude hand tools. It now relies on complex machines and extremely precise tools that are able to mass-produce millions of the same part with virtually no mistakes. It may be the lid of a water bottle or the container of a detergent, chances are that it was made with specialized equipment that is designed to get the job done quickly, precisely, and safely.
In this article, we will explain how modern manufacturing uses precision equipment and automation devices, and how these technologies are more critical than anything else today. We will explain two topics in more detail as well: bottle cap mold accessories and cap pressinging machines. They’re only a small piece of the overall picture, but they show how science, engineering, and automation converge to power the products that we utilize every day.
The Importance of Precision in Production
Accuracy is the ability to do something in the very same way, time after time. In manufacturing, it is the ability to cut, form, or shape material to tiny tolerances—sometimes in micrometers (one-thousandth of a millimeter). Accuracy is important because a tiny difference can create enormous problems, like parts that won’t fit together or products that will definitely break.
One of the greatest examples of this is on bottle caps. We place them on water bottles and household cleaners. If a cap is just a little off, then it leaks or won’t open. That is why companies pay such close attention to using molds and tools to ensure each cap is the same.
Jinchen Precision is a company that specializes in producing plastic cap accessories and equipment. The bottle cap mold accessories of their company are employed in the machines that form the molten plastic into the precise form of a cap. The molds need to be very accurate and durable because they are used repeatedly on high-speed production lines.
How Bottle Cap Molds Work
Production of plastic caps starts with injection molding. In this process, plastic is melted and molded in liquid state and injected into metal molds. The mold is opened, and the finished cap is pushed out when it is cooled and hardened. This is done in seconds and thousands daily.
The mold itself must be flawless. If it’s ever so slightly imperfect, the cap might be the incorrect size or shape. That’s why manufacturers like Jinchen Precision use the finest steel on the market and the most modern machining tools to make their molds. They also produce accessories such as ejector pins and cooling systems that contribute to the elegance of the process.
Without these, there would be no method for producing caps that fit well at all times. This shows just how important accuracy is—not only to the product itself, but to the equipment used to produce the product.
Automation in Modern Packaging
Once the cap has been produced, it needs to be fitted to a container. It would be time-consuming to do this manually and would cause errors. That is where cap pressinging machines come in handy. These machines can fit hundreds or even thousands of lids in a given hour with minimal human labor.
TC Machinery has the machinery to do exactly that. Their cap pressing machines can cap any type of container, be it plastic boxes for detergents or metal cans. They are quick, efficient, and easy to install in nearly any factory.
One of the great benefits of machines such as these is their versatility. They can accommodate lids of various sizes and shapes without the cost of an entire new machine. This is cost-effective and space-effective, and enables the companies to very rapidly respond to new packaging requirements.
How Cap Pressing Machines Work
Cap pressing machines are usually equipped with some typical components:
- The conveyor belt that carries containers into place
- A sensor system to measure the size and kind of the container
- A machine press that pushes the lid onto the container mechanically
- A pressure controller that modulates pressure, timing, and position
These machines also have automation capabilities such as programmable controls and safety aspects. This is to say they can be left operating during the day with reduced supervisions and less possibility of damage or harm.
Aside from safety and speed, these machines also enhance seal quality. Seal quality guarantees the product to be fresh, safe, and convenient to transport. This is particularly useful for fluid products like detergent because leaks can cause severe issues.
Accuracy Meets Effectiveness
The precision of the molds and machine usage automates the process, allowing companies to attain maximum production with zero compromise on quality. A factory using both Jinchen Precision mold accessories and TC Machinery cap pressing systems can seal and fill thousands of containers an hour, all with the same outcome.
This not only conserves waste but also conserves money for companies in the form of materials, labor, and repairs. Good tools mean less trouble, and that means less time and money wasted on fixing mistakes.
The Role of Innovation and Engineering
Behind all of these machines and tools are groups of engineers and technicians who will design, test, and refine the technology. They would simulate, through computer models, how plastic would flow into a mold, or how pressure would impact a lid in sealing. They would also conduct actual testing to observe how materials would behave when subjected to heat, stress, and wear.
Innovation continues here. Businesses now look at ways of printing molds through 3D printing, which can be done quickly and at a low cost. Others are incorporating smart sensors into equipment, so that it can identify faults and adjust accordingly.
These technologies allow factories to be more responsive, efficient, and responsive to demand while producing the highest quality products.
Why This Matters to Everyone
You might not be considering cap pressing machines or mold tools when you buy a bottle of water or a box of soap. But without them, you might not have the item—or at least not in the form you know. Precise tools and equipment are the quiet backbone of modern life. They help create the packaging that protects our food, contains our cleaning materials, and makes products easier to use.
And as the global community becomes greener, precision also cuts down on waste. Improved tools mean fewer defective parts. Intelligent machines mean lower energy consumption. It is a win-win for companies and the planet.
Conclusion: Building a Better Future in Manufacturing
Modern manufacturing depends on a great deal more than fast equipment. It requires careful planning, technical expertise, and a commitment to getting it right. From casting plastic caps with precision molds to closing containers with state-of-the-art press machines, every detail matters.
Firms such as TC Machinery and Jinchen Precision are at the forefront. By using precise tools alongside intelligent automation, they demonstrate how technology can make production more efficient, more consistent, and less polluting.
Gazing out to the horizon, the message is unavoidable: precision and automation are not options—they’re requirements. And with the appropriate machines and equipment, we can build a manufacturing universe that’s ready for anything.
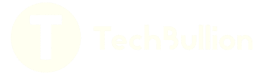