If you are a textile or apparel exporter, then you know that a little error in production or shipping can be quite catastrophic. Things like a missing button, a needle lodged in fabric, or damage during shipping can cause serious financial damage and even put your business reputation at risk.
The question now is, how can you as a textile and apparel exporter guarantee consumer safety and also ensure your products aren’t damaged during shipping? This is where pre-shipment inspection comes in.
What is Pre-Shipment Inspection?
Pre-inspection shipment is a quality control process through which exporters ensure that their products meet the quality standard of customers before shipping. It also involves packaging the products properly to ensure that they are not damaged before they get to the customers.
This quality control process is the way most textile and apparel exporters today establish high standards. Pre-shipment inspectors usually will perform several visual and functional tests on a sample of the apparel exports and their packaging to detect damages or defects. With the aid of automation, this process also ascertains if the packaging is sturdy enough to withstand shocks, tearing, rupturing, and any other damages to the textile or apparel during shipment.
Importance of Pre-Shipment Inspection for Textile and Apparel Exporters
As a textile and apparel exporter, ensuring product quality is of utmost importance not just for the sake of regulatory compliance but also for the sake of your brand. To succeed in today’s highly competitive textile and apparel industry, your textile exports must be free from damages and also match the required quality standards set by the buyer.
Quality control and pre-shipment inspection are effective tools to protect exporters against costly risks. As much as it is important to save time and meet shipping deadlines, rushed or no inspection at all leads to costly delays in production and product recall. Quality control is generally more efficient when done with proper care. The introduction of automated machinery such as automatic needle detectors has ensured that quality checking and inspection can be completed faster and more effectively than before.
In summary, every textile and apparel exporter needs to adopt proper quality control processes not just to avoid legal problems but also because of the other advantages it brings. Some of these advantages include;
- Identification of quality defects
- Promotion of brand reputation
- Improvement in import efficiency
- Avoid costly rework and delays
Benefits of Working with a third-party Inspection Company for Pre-Shipment Inspections
For many textile and apparel exporters, having a final random inspection forms part of their quality control process. Working with a third-party inspection company, however, ensures a higher level of assurance and control.
There are several elements involved in conducting a proper pre-shipment inspection; from defining the units that will be selected for evaluation to the final random inspection process. Third-party inspection companies follow the ANSI Z1 .4-2008 (ANSI Sampling Table) to define the number of units that will be randomly selected for evaluation. One major benefit of this is that detecting quality defects at an early stage of the final random inspection can be guaranteed.
Third-party pre-shipment inspectors always work closely with clients to develop detailed product checklists that can be used on-site. The final random inspection checklists are specifically designed according to the client’s requirements and products.
At the end of the day, the goal is to prevent textile or apparel exports with visual or functional defects from being shipped to buyers and end-users. Third-party inspectors are experts at detecting defects. One notable thing about them is that they are not affiliated with any factories or companies and so can provide unbiased and independent inspection reports.
Once inspectors detect a trend where the same or similar types of defects are being repeated, inspection data will inform intervention which will promote the manufacturer’s quality performance. A professional pre-shipment inspection assures concerned parties that their products are ready to be exported to their destination market.
Overview of the Inspection Process
The inspection process for textiles and apparel exports is unique and differs greatly from other export products. Pre-shipment inspections are carried out on-site at the factory or production company and often involve the following procedures:
Quantity Verification
This involves verifying the correct quantity of the product to be exported. The inspectors count the shipping cartons to ensure that the correct number of products and boxes will be sent to the right destination. This phase also involves verifying that the correct packaging material is being used.
Random Selection
All certified pre-shipment inspection companies use the internationally recognized statistical sampling procedure. The acceptable number of defects in a batch of textile exports is defined with an Acceptance Quality Limit (AQL).
Cosmetic and Workmanship Check
After the random selection, the next thing the inspector does is examine the workmanship of the textiles for any visible defects. Visible defects are often categorized as minor, major, or critical. This assessment is based on specifications that have been agreed upon by the exporter and customer.
Function Test
Specifically for textile or apparel inspections, the inspector performs a series of physical tests on the product to determine the strength of the zippers, buttons, and other embellishments. Oftentimes, pull tests, fatigue tests, and stretch tests are carried out. The number of stitches per inch is also counted while advanced tools are used to measure fabric density.
After identifying defects, the inspectors sort them into different categories based on the severity of the defects. Inspection results are either tagged PASSED, PENDING, OR FAILED. Inspection reports are delivered within 24 hours of completion with each report outlining the client’s order, a summary of the inspection result, and the detailed inspection results. Some pre-shipment reports include clear digital images or photos, to show exactly what was discovered at all inspection points.
Conclusion
Textile and Apparel exporters have to make sure that the products they export are safe for customers and are well-packaged enough to resist damage during the shipment. The pre-shipment inspection involves the meticulous evaluation of products before they are shipped to verify their quality, quantity, and price and as such is crucial for textile and apparel exporters.
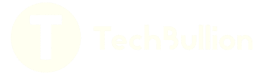