Introduction
Crucibles are critical in various industries, and the crucible material choice significantly impacts process quality and efficiency. Boron nitride (BN) crucibles have gained attention for their unique properties. This article compares boron nitride crucibles to other common crucible materials, highlighting the advantages of BN.
Chemical Inertness:
BN crucibles are highly chemically inert, resisting reactions with molten metals and corrosive substances. This minimizes contamination and preserves material integrity.
Non-Wetting to Molten Metals:
Boron nitride crucibles have low wettability to molten metals, preventing adhesion and allowing easy material removal. This property is beneficial for processes using reactive and sticky materials, reducing adhesion issues.
Thermal Shock Resistance:
BN crucibles have excellent thermal shock resistance, withstanding rapid temperature fluctuations without cracking or deforming. This enhances crucible longevity and reliability, especially in applications with demanding thermal cycling unlike quartz and alumina crucibles.
Electrical Insulation:
Boron nitride crucibles demonstrate strong electrical insulation properties, making them suitable for processes requiring electrical resistance or insulation. This characteristic is valuable in applications like induction melting, where electrical currents must be controlled, unlike graphite crucibles which are conductive.
Compare with metal crucibles
When compared to metal crucibles, boron nitride crucibles present several advantages. Metal products offer versatility in terms of processing methods, allowing for the creation of various shapes and even large-sized crucibles through welding. However, metals are prone to chemical reactions at high temperatures, and their strength significantly diminishes under such conditions. Refractory metals like molybdenum, tungsten, and tantalum are preferred due to their high temperature tolerance. Yet, the stronger the temperature tolerance of a metal, the more challenging it becomes to shape and manufacture. Tungsten and tantalum, for example, are scarce resources, and the energy-intensive manufacturing processes of their crucibles make cost reduction difficult. These metal crucibles can introduce impurities into the materials being melted due to their similar composition. Furthermore, metal crucibles have poor wettability to molten metal compared to ceramic materials. Consequently, ceramic crucibles, such as boron nitride crucibles, offer significant advantages in specific applications.
Tantalum Crucibles
Compared with graphite
Graphite is a crystalline form of carbon, characterized by its dark black to deep gray color. Graphite has soft texture, smooth surface, conductivity, and chemical inertness. Therefore, it is commonly used for crucible production. However, graphite crucibles suffer significant corrosion during smelting and casting processes, reducing their lifespan. Moreover, due to the conductivity of graphite, in induction furnaces, induced currents heat the graphite crucible instead of the material inside it. This property could be advantageous in some cases but not suitable for all materials. Additionally, the carbon element in graphite can alloy with many metals, introducing undesirable impurities. In contrast, boron nitride minimizes the possibility of impurities in the melted metal. Early boron nitride formulations incorporated additives like CaO as binders for easier sintering, which could be an impurity for the melting material. As advancements in manufacturing techniques continues, manufacturers have reduced the need for binders in boron nitride materials. For example, BN99 boron nitride from QS Advanced Materials contain only about 0.3% CaO, while higher purity TPBN boron nitride ceramics have overall impurity levels below 0.1%. Both graphite and boron nitride materials offer strong processability, allowing for CNC machining into various shapes. Therefore, if graphite can produce complex shapes that are challenging for other ceramics, boron nitride can achieve the same.
Compared with oxide ceramics
Aluminum oxide and quartz are the most common materials for oxide ceramic crucibles. Oxide ceramic crucibles do not require air shielding during the production process, resulting in relatively low manufacturing costs, making them widely used. However, oxide ceramics are brittle and hard, which makes them difficult to machine using conventional methods, and their shape precision from direct sintering is poor, making it challenging to create precisely shaped crucibles. Moreover, oxide ceramics have much higher thermal expansion coefficients compared to boron nitride, and high-density oxide ceramic crucibles have poor thermal shock resistance. On the other hand, as oxides, the presence of oxygen in certain specific applications is unacceptable, necessitating the use of alternative materials.
Carbide ceramics are commonly used high-temperature resistant ceramic materials, apart from oxide ceramics. Similar to oxide ceramics, they are highly hard materials and have limited processing methods after sintering, such as drilling and grinding. A relatively inexpensive method to obtain carbide ceramics is through reactive sintering, but this method often results in a significant amount of free carbon, which is not desirable for crucibles. On the other hand, the manufacturing cost of high-purity carbide ceramics is considerably high, which often hinders their widespread application.
Compared with other nitride ceramics
When comparing boron nitride crucibles with other nitride ceramic crucibles, notable differences arise. Silicon nitride is the most common representative of nitride ceramics, besides boron nitride. It shares similar characteristics with carbide ceramics, being hard, high in strength, and challenging to process. Customizing a new size often takes over a month, and high-purity silicon nitride products are costly. Therefore, unless for specific cases, using silicon nitride as a crucible material is not recommended. The same applies to aluminum nitride (which is generally more expensive than silicon nitride). In contrast, the advantages of boron nitride crucibles are more evident. Chemically, it is similar to other nitride ceramics, but it is softer and can be processed into various shapes after sintering. This allows manufacturers only need to keep stock for sintered boron nitride blanks, and quickly process them into different shaped products for customers. The change in stocking methods significantly reduces overall costs compared to other nitride ceramics. Consequently, boron nitride has become the most widely used nitride ceramic material.
Conclusion
In summary, boron nitride crucibles provide a range of advantages that differentiate them from other crucible materials. Their high-temperature stability, chemical inertness, non-wetting properties, thermal shock resistance, and electrical insulation make them a preferred choice across many industries. While materials like graphite, alumina, quartz, and zirconia have their own applications, boron nitride crucibles excel in demanding processes requiring extreme temperatures, resistance to chemical reactions, minimal adhesion, thermal shock resistance, and electrical insulation.
As technology continues advancing, the demand for boron nitride crucibles is expected to grow, driven by their superior performance and reliability. The unique properties of boron nitride make it an optimal choice for applications in materials science, metallurgy, and chemical processes where precision, purity, and efficiency is paramount. By selecting boron nitride crucibles, industries can enhance their processes, improve product quality, and achieve greater control over their operations.
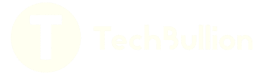