At the heart of what modern manufacturing is today is a key change—one where machines and human skills meet to change how much can be done. Hidden underneath every well-designed product and high-quality package is an important engine for steady production. Global industries depend on it to produce precise and complex shapes as standards in design continue to rise.
As good technology continues to grow, equipment for manufacturing has become more than tools—it now closely cooperates to help produce items from raw components to the final finished products.
Industrial Evolution Needs Precision: Why Die Cutting Must Step Up
Nowadays, the speed of manufacturing means that precision is no longer optional—it’s required. With each change in industry, pressure for quality, quick results and less waste causes standard processes to reach their maximum. Shaping challenges are met in large part thanks to die cutting. Still, these traditional systems tend to miss the mark when it comes to complicated designs and lots of repetitive production.
At this point, die cutting technology needs to adapt and improve. The shift toward fully automatic flatbed die cutting machines marks a significant leap forward, offering unparalleled precision, speed, and efficiency. They allow businesses to have better quality products, simplify their workflows, avoid common mistakes and use less material. Since millimeters matter greatly today, die cutting needs to stay ahead of new industrial developments.
Using automation and precision technology enables manufacturers to compete and satisfy the expectations of today’s markets.
What Is a Fully Automatic Flatbed Die Cutting Machine?
A fully automatic flatbed die cutting machine is a sophisticated piece of manufacturing equipment designed to cut, shape, and crease materials with remarkable precision and speed. Unlike conventional machines that require manual operation, six-side printing does everything, from adding raw materials to stacking the finished product, without much need for workers.
One reason these machines are valuable is that they can make complex die-cut shapes on several types of materials, including plastics, paperboard and even thin metals. Due to their versatility, films are needed in packaging, the automotive, electronics and other industries. The importance of fully automatic flatbed die cutting machines lies in their transformative impact on productivity and quality control. They help manufacturers save time and money by providing accurate cuts that use little waste and take up little time.
In addition, their ability to automate tasks helps ensure workers avoid being exposed to danger repeatedly.
A Hidden Player in Metal Can Bottom End Production:
Every part of metal cans for packaging is important for keeping the product safe and satisfying the customer. One often overlooked but vital part is the metal can bottom end—the sturdy base that supports the entire container and maintains its shape under pressure. Behind the seamless production of these essential components is the fully automatic flatbed die cutting machine, a hidden player that quietly delivers precision and efficiency.
With great precision, this machine shapes and slices the sheets, guaranteeing every bottom end is of good quality. Automating how die cuts are made allows manufacturers to create endless metal can bottoms that are both perfectly sized and have smooth edges. Simplified can seaming increases the strength of cans and makes assembly run smoother, so not as much time is spent solving bottlenecks and more items can be produced.
The role of the fully automatic flatbed die cutting machine in metal can bottom end production exemplifies how advanced manufacturing technology supports even the smallest components—components that ultimately have a huge impact on product performance and consumer trust.
The ‘Intermediate Link’ That Holds Production Together
In any type of manufacturing, the efficiency is determined by how well the various stages are connected. The fully automatic flatbed die cutting machine acts as a crucial ‘intermediate link’ that bridges raw material preparation and final assembly, ensuring the entire workflow remains smooth and uninterrupted.
By delivering precisely cut components—whether it’s packaging blanks or metal can bottom ends—this machine guarantees that subsequent processes like folding, sealing, or welding can proceed without delays or quality issues. Because of its automation, this process reduces errors and always gives the same end result which is essential for production lines that need to work quickly and accurately.
A reliable link is necessary so that manufacturers do not face production slowdowns and spend more money. The fully automatic flatbed die cutting machine’s ability to keep materials perfectly shaped and ready for the next step is what holds modern manufacturing together, enabling factories to meet tight deadlines and maintain competitive advantage.
Multi-Industry Applications: Beyond Just Packaging
While the fully automatic flatbed die cutting machine is often celebrated for its role in packaging, its influence extends far beyond this single industry. With its accuracy and many features, it plays an important part in several manufacturing areas. Machine tools are often used in the automotive industry to cut gaskets, insulation materials and components to the right dimension.
Folks in the electronics field depend on them to build sensitive components like circuit board masks and protective films. The medical arena relies on their skills to produce specific shapes for items used just once and for medical packaging. By being useful in multiple sectors, it demonstrates how the machine processes any combination of paper, plastic, rubber or metal just as quickly and accurately.
By serving such a broad spectrum of applications, the fully automatic flatbed die cutting machine underscores its indispensable role in modern manufacturing, driving innovation and quality across countless products and markets.
Conclusion:
The fully automatic flatbed die cutting machine stands as a silent powerhouse in modern manufacturing, blending precision with automation to transform how products are made. From crafting flawless metal can bottom ends to shaping components across diverse industries, this technology is a critical enabler of efficiency, quality, and scalability.
When these systems are used, manufacturers are able to make more products, spend less on material waste and provide a constant output to stay ahead of the competition. As different branches of industry change and develop, the value of this quiet process will also grow.
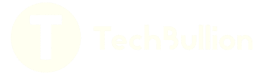