Data centers, manufacturing facilities, power plants, and HVAC systems all heavily rely on cooling towers. They contribute to the efficient operation of machinery and equipment by regulating and dissipating heat. But due to constant use and exposure to the elements, some of cooling tower parts may deteriorate, sustain damage, or wear and tear with time. They ought to be changed appropriately to take care of any linked possible problems.
The average lifespan of a cooling tower
The conventional cooling tower’s average lifespan has risen compared to previous years due to technological advancements. Towers typically require 20 to 30 years of regular maintenance before requiring significant repairs or replacements. However, those significant repairs can need to be made much earlier if the right actions have been performed over the years or just by bad luck.
Repair or Replace: Which Is The Better Option for cooling tower components ?
If regular cooling tower maintenance is performed, a cooling tower’s usual lifespan is 15 to 30 years. However, it’s time to make important repairs if you’ve noticed a drop in its performance and rising cold water temperatures. When a repair isn’t practical, it’s time to make replacement plans. If the cost of cooling tower repair is more than half of the cost of replacement, you’ll know that this is the right course of action. In this scenario, replacing the cooling tower will be a more sensible financial move. However, if you can fix rather than replace, you’ll probably save a lot of money because replacement frequently requires extensive planning, scheduling, and expense.
It could be advisable to replace the entire cooling tower if the repair will involve several man-hours and major pieces of equipment. Investing in a new and upgraded cooling tower can be the only way to solve your cooling tower’s issues. To prevent costly downtime and long-term maintenance expenses associated with cooling tower issues, these systems are now significantly more efficient. It’s important to weigh your cooling tower alternatives according to tonnage and consult with one of our knowledgeable specialists to help you make the right choice.
The cost of downtime with an outdated, high-maintenance cooling tower is another factor that shouldn’t be ignored. How much does it cost building occupants who lose their air conditioning? or decreased output in factories that handle manufacturing?
When there’s a chance that the cold water basin won’t sustain the weight any longer, is it preferable to build a new cooling tower in this case?
It’s easy maths: replace the unit if the cost of cooling tower repair exceeds 60% of the cost of a new one. This implies that the location of equipment and the cost of servicing cooling towers for repairs may have a significant impact on the price of major restoration for operating units.
However, because the tower shell never needs to be relined or renovated and requires very little total maintenance, cooling towers built on seamless engineered polyethene shells have a far lower cost of ownership.
Making Cooling Tower Repairs:
Let’s talk about the benefits of cooling tower maintenance first.
- The cost is lower than if the cooling tower were replaced.
- Repairing a cooling tower is frequently a simple and quick process.
- The cooling tower has many more years of useful life left in it.
- While upgrading, thermal performance may be improved.
Alright, what are the drawbacks of cooling tower repair?
- It’s possible that some harm is irreparable.
- The issue might not be entirely resolved by the cooling tower repair.
- Following a repair, the cooling tower might not be able to function to its full potential.
Here are some noteworthy advantages of prompt frigid coil cooling towers part replacement if you now manage and operate cooling towers.
Increased Energy Efficiency All Around
Industrial processes generate heat, which cooling towers remove with great energy usage. Fan blades, motors, and fill materials are examples of parts that might deteriorate over time and lose some of their performance. By replacing these worn-out components on time, you can minimise energy waste and operational expenses while ensuring that the cooling tower fans run as efficiently as possible. Long-term savings can be achieved by upgrading to more energy-efficient components, which can help improve total energy efficiency.
Increased Efficiency of Heat Transfer
A cooling tower’s fill material increases the surface area that can evaporatively absorb heat, facilitating the transfer of heat. However, the cooling tower fill media ability to conduct heat could deteriorate or get clogged with impurities. To ensure adequate cooling and avoid system inefficiencies, the cooling tower’s heat transfer efficiency can be restored by replacing worn-out or fouled fill material.
Reduced Water Losses and Leaks
To stop water leaks and losses, cooling tower component integrity is essential. The cooling tower’s effectiveness may be impacted by corrosion, erosion, or wear, which may also cause water waste and possible harm to nearby infrastructure and equipment. Professionals should replace worn-out or defective parts on time to preserve the integrity of the system, avoid water leaks, and guarantee economical water use.
Decreased Interruptions and Downtime
Operations might be disrupted by a malfunctioning cooling tower, which can lead to expensive downtime and production delays. It is simple to lower the chance of unexpected breakdowns and lessen their impact on operations by replacing essential components on time. In addition to preventing unanticipated failures, proactive maintenance and part replacement can maintain system functionality.
Guaranteed Compliance with the Requirements
Regulations about the environment and safety, such as those governing emissions, noise levels, and water treatment requirements, apply to cooling towers. Deteriorating or ageing parts might not adhere to the regulations as they stand, which could lead to problems with compliance. Your company can guarantee that its cooling towers comply with all applicable safety and environmental laws by promptly replacing any out-of-date or non-compliant equipment.
Replacing cooling tower parts on time is essential to preserving peak performance and efficiency. Your company may optimise cooling tower efficiency, lower operating costs, and extend equipment lifespan by prioritising routine inspections, proactive maintenance, and prompt replacement of worn or broken parts. In addition, working with knowledgeable cooling tower suppliers and professionals can give you access to high-quality spare parts and knowledge, which can further increase the effectiveness and performance of your cooling tower systems.
Professional Advice for replacement cooling tower parts:
Cooling towers lose efficiency after many years of use, which puts more strain on the other parts of your entire cooling system. You may reduce this capacity loss and increase the lifespan of the cooling towers, pumps, chillers, heat exchangers, and other components of your cooling system by implementing appropriate maintenance programmes and doing regular servicing.
To minimise long-term maintenance costs, it might eventually be time to replace your cooling tower with a new model. Selecting between plastic and metal for your new cooling tower might have a significant impact on its lifespan and functionality.
The following list of a few factors justifies replacing a metal cooling tower:
Durability:
These days, engineered plastic cooling towers are a more practical solution than metal cooling towers for most commercial buildings because of advanced high-density polyethene (HPDE) technology, which stands up better over time. The extended lifespan of plastic industrial cooling towers can also be ascribed to the substantial warranties that accompany them. Due to the plastic cooling towers’ seamless construction and resistance to corrosion, providers are more inclined to offer lengthy warranties.
Increased energy efficiency:
Even the most costly cooling tower models made of stainless steel are composed of welded sheets that are prone to leaks. A cooling tower that leaks is not likely to operate at maximum efficiency, as any facility manager is aware.
Reduced expenses for upkeep:
When the downtime from regular cleaning, corrosion maintenance, and apparent leakproofing is factored in, traditional metal cooling towers may get expensive. By replacing the cooling tower with a new seamless design and plastic material, these three issues can be resolved. Additionally, the caustic or acidic water treatment chemicals that frequently result in leaks or other common problems with metal cooling towers are impenetrable to modern HDPE technology.
Alternatives for antimicrobials:
Microbes that thrive in the typical cooling tower setting can frequently create health hazards like Legionnaire’s disease. To stop the growth of dangerous bacteria and lessen outbreaks, antimicrobial resins can be added to the plastic used in new cooling towers.
Every building needs a different approach. Equipment replacements may be the consequence of an emergency or part of a growth strategy. For any reason, you should hire a group of project managers and experts who will assess your current system thoroughly and then recommend the most economical and energy-efficient ways to upgrade the cooling tower in your building.
So how can you determine if it’s time to replace the complete tower or if a repair is your best bet? The solution is to add up the prices of the two solutions mentioned above, taking into account the age of your tower and the possibility of an extended lifespan with the required maintenance.
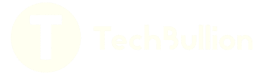