Electron beam (eBeam) technology, long utilized for specialized manufacturing processes, has evolved significantly over the past decade. Known for its precision, speed, and efficiency, electron beam technology is increasingly being adapted to meet the growing demands in fields like aerospace, automotive, and healthcare. But with these advancements, the question arises: what’s next for eBeam machine technology?
A Quick Overview of eBeam Technology
eBeam machines utilize a focused beam of high-energy electrons, which is directed at a material, causing localized melting or modification. This process is highly effective in manufacturing applications such as welding, additive manufacturing, surface modification, and heat treatment. eBeam technology can achieve high precision with minimal thermal distortion, making it ideal for materials that are sensitive to heat.
One primary advantage of eBeam machine technology is its ability to work in a vacuum environment, which minimizes contamination and enhances control over the manufacturing process. Additionally, it allows for efficient energy use, with energy directly transferred to the target area, reducing waste and overall energy consumption.
Recent Advancements in eBeam Technology
Over the last few years, significant improvements have been made to eBeam machine capabilities. These advancements range from enhanced beam control to integration with digital manufacturing systems, and each innovation has pushed the boundaries of what eBeam machines can achieve.
- Improved Beam Control and Precision
Advances in digital control systems and software have enabled greater precision in eBeam machines. For example, new machine designs incorporate AI algorithms that can adjust beam parameters in real-time, leading to higher accuracy and reducing errors. This technology can be particularly beneficial for industries that require exacting standards, such as aerospace and medical device manufacturing. - Hybrid Manufacturing Systems
As manufacturing processes become more integrated, hybrid manufacturing systems that combine eBeam technology with other techniques (such as laser or additive manufacturing) have emerged. These systems allow for faster production and reduce the need for secondary processes. The result is more complex and highly customized parts that can be produced in less time, a significant benefit for industries where customization and efficiency are crucial. - Automation and Machine Learning
Automation is another area where eBeam technology is making strides. By incorporating machine learning algorithms, eBeam machines can learn from previous operations to optimize settings for future tasks, improving overall efficiency and reducing waste. Automation also allows for increased uptime, as machines can self-monitor for issues, perform self-calibrations, and even adjust their settings autonomously. - Enhanced Additive Manufacturing Capabilities
Additive manufacturing with eBeam technology, also known as electron beam additive manufacturing (EBAM), is transforming the way high-strength metals like titanium and superalloys are processed. With eBeam machines, manufacturers can produce lightweight, complex metal parts that meet strict tolerance requirements. This capability has been especially valuable in aerospace and medical sectors, where the demand for strong yet lightweight components is high. - Eco-Friendly Manufacturing
With growing pressure to adopt sustainable practices, eBeam machine technology is well-positioned as a low-waste and energy-efficient option. As eBeam technology requires no hazardous chemicals and operates in a closed system with minimal emissions, it is increasingly seen as a viable choice for environmentally conscious manufacturers. Innovations that further improve the energy efficiency of eBeam machines could make it an even more attractive option in sustainable manufacturing practices.
What’s Next for eBeam Machines?
While current advancements have elevated the capabilities of eBeam machines, the technology is far from reaching its full potential. Several emerging trends and technologies are likely to shape the future of eBeam machines, allowing them to achieve even greater precision, efficiency, and versatility.
- Higher Beam Power and Modulation
Future eBeam machines are likely to feature higher beam power and more versatile modulation options. This development will enable them to work with a broader range of materials and complete even more complex manufacturing tasks. High-powered beams could potentially reduce process times and make eBeam technology competitive with other high-speed manufacturing methods, such as laser-based systems. - Integration with Industry 4.0
As manufacturing shifts toward the Industry 4.0 model, which emphasizes interconnectivity and real-time data processing, eBeam machines are poised to play a crucial role. By connecting eBeam systems with broader production networks, manufacturers can monitor performance metrics in real time, make adjustments to enhance quality, and optimize resource allocation. This integration will drive efficiencies across entire manufacturing ecosystems, reducing downtime and waste. - Enhanced Software Capabilities and AI Integration
Future advancements in AI and software for eBeam machines will provide even greater control over manufacturing processes. For instance, AI-driven systems could analyze data from previous projects to improve accuracy, predict machine wear, and suggest maintenance schedules. These AI capabilities will make eBeam machines smarter, capable of autonomous decision-making, and highly adaptable to varying production demands. - Expanded Applications in New Sectors
With its ability to produce precise and complex parts, eBeam technology is likely to find applications in emerging industries like renewable energy, where it could be used to fabricate parts for wind turbines, solar equipment, and energy storage systems. The technology’s inherent precision and environmental advantages also make it suitable for developing sustainable, long-lasting components for a wide range of applications. - Miniaturization and Portability
Another exciting frontier for eBeam technology lies in the development of portable or miniaturized machines. While eBeam systems traditionally require sizable equipment and infrastructure, innovations in beam focusing and power systems could lead to more compact models. Such advancements would make eBeam machines more accessible for smaller manufacturers and open up possibilities for on-site repairs or modifications in industries like aerospace, where in-field servicing can reduce downtime.
Conclusion
The future of eBeam machine technology looks promising, with advancements geared toward greater precision, efficiency, and versatility. As eBeam machines continue to evolve, they will play a critical role in shaping the next generation of high-tech manufacturing. Whether through increased integration with AI, new applications in renewable energy, or hybrid manufacturing systems, eBeam technology is on track to become an even more essential tool in a range of industries.
For those keeping an eye on the latest in manufacturing technology, eBeam machines represent a dynamic, sustainable, and rapidly advancing solution that is likely to define the future of precision manufacturing. The ongoing innovations in electron beam technology will continue to drive efficiencies, enabling manufacturers to meet the challenges of modern industry with greater flexibility and minimal environmental impact.
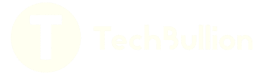