Regarding manufacturing systems in production management, it’s clear that a simple software solution just won’t cut it. You need a solution as dynamic and robust as your production line. The software you use can often make the difference between endless efficiency and costly stops. With all the alternatives available, how do you choose one that works for you? The answer is clear. You need to use a software solution that integrates management and transformation processes, helping your team get more connected while providing meaningful insights.
For example, A North American food processing plant opted for an intuitive system that needed just a little training so their team could focus on production. Ultimately, for manufacturers looking to make a difference, LLumin offers a solution that will redefine maintenance management software. This blog aims to discuss critical characteristics you should consider when choosing a manufacturing maintenance solution and how LLumin aids with its pricing plans for this software.
Key Attributes In Manufacturing Maintenance Solutions
1. Connectivity With Manufacturing Control Platforms
A comprehensive manufacturing inventory management system would be able to connect with your current system in the production area easily. Once in place, the software needs to communicate with high-speed production systems so that it can provide actual time data. The integration helps to coordinate maintenance schedules with production, preventing downtime events.
- 24/7 System Reassurance: You can now monitor your equipment or process in actual time through integration. Any equipment breakdown or downtime is immediately diagnosed by production management if maintenance software can be synchronised with them, and fast corrective action may also take place.
- Automated Workflows: Integrated systems can automate maintenance workflows according to the production plan. For example, when a machine needs maintenance, the system can automatically adjust production schedules to reflect and even accommodate that downtime.
- Better Decision Making: Manufacturing maintenance software offers a 360-degree of operations that helps managers make decisions by keeping actual time data in view. Through this, you will save on maintenance and serve production more efficiently.
2. Elite Stock Handling Tools
Another important feature of manufacturing maintenance software is strong inventory management capabilities. An industrial supply chain manages the list of all parts and materials necessary to ensure they are adequately stocked, so maintenance does not get delayed.
Inventory Tracking: The inventory level should be tracked accurately with all spare parts and tools in stock. This reduces the chances of equipment downtime because of lack of parts.
Automated Reordering: Advanced software can automate purchasing policies. This blockchain suite should be smart enough to understand when the levels of inventory drop below a specified point and will order an automatic reordering based on minimum thresholds set for all crucial components, so there is constant availability.
Cost Management: Inventory management software should be able to track costs because when you have no idea about the cost of goods, how would you even price them? Being able to understand an inventory’s cost implications enables businesses to make more accurate decisions in the stock levels, cutting down on irreplaceable spending.
3. Inclusive Machinery Service Oversight
Maintaining equipment, however, is a core feature of any manufacturing maintenance software. This feature takes care of documenting, tracking and optimizing maintenance activities.
Maintenance Logs: The system should keep detailed logs of any work done for maintenance. This will cover things like regular maintenance, emergency repairs or standard checks. These logs act as a record that tells you how much wear and tear the equipment was under during its life.
Predictive Maintenance: Comes with advanced tracking features to make predictive maintenance possible. It can anticipate some machine failures by looking at performance and historical data, letting you get to the equipment before something breaks.
Compliance and Reporting: Your equipment maintenance tracking software must add in the features of compliance and reporting. This is key for industries with heavy compliance requirements. The reports should clearly show areas of compliance with industry standards, and regulations.
4. Flexibility And Fine-Tuning
People forget that there is a great diversity when it comes to software for manufacturing and inventory. What works for one company may not necessarily work for another. For that reason, the software for production and inventory should be adjustable to correspond with certain business processes.
User-Defined Workflows: User-defined workflows are key. As a result, businesses can customize the software according to their specific workflows, meaning that companies maintain the ability to chain users together correctly.
Scalability: The needs of a business change as it grows. Ideally, the best software should be scalable to support new features or users without damaging existing system operations.
Custom Reporting: Businesses can create reports that provide them with the type of information they want to see. Whether it is about tracking KPIs or you have to create compliance reports, custom reporting ensures that every piece of information is accurate.
5. Learning Support And Simplicity
If software is dense and convoluted, or hard to understand and operate, it will eventually fail no matter how advanced the technology may be. Thus it is important to think how easy the tool should be for newcomers.
-User-Friendly Interface: It must be easy to use and navigate through the various components without requiring extensive training. This minimizes a steep learning curve, and the new system is quickly taken up by the employees.
-Training And Support: The vendor should provide training and support. This entails the teaching of new users at startup and continued user support including manuals and online tutorials.
User Permissions: The software should offer the ability to assign user permissions, meaning operators should only get access to what they need according to their roles. It ensures that security is in order and no one steals your data.
6. Price Factors
Cost, as with any business expenditure, should not be the only thing to consider when opting for manufacturing maintenance software.
Licensing And Subscription Fees: What does the software cost? Some may charge a one-time licensing fee, whereas others run on a subscription. After evaluating both the two-wheelers for a couple of seconds, select the model that suits your pocket and future finances.
Return On Investment (ROI): Estimate the potential return you could get after purchasing and implementing this quality control software. Factors to consider include reduced downtime, use of resources and savings on maintenance costs. If the long-term benefits are good, a higher initial cost may be justified.
Hidden Costs: Find out about hidden costs, such as charges for extra users, more functions or ongoing support. Be transparent about all costs and mention them in your budget.
7. Measures Of Shielding
All businesses put data security high on their list of concerns, and manufacturing maintenance software providers are no different. They should also include strong security measures to secure confidential data from being accessed by others except for authorized personnel.
User Authentication: The user should have to prove their identity via things like password or biometrics else it can lead to someone having unauthorized access.
Data Encryption: Any data in transport or at rest should be encrypted by the software itself. This ensures that the data cannot be read or modified by unauthorized parties.
Backup And Recovery: Software should provide automatic backup and recovery features. These features allow for rapid recovery of data with minimal business interruption during a system failure or in the case of a security breach.
8. Aid And Vendor Credibility
Another essential point is the reputation of a software vendor. The kind of vendor that you are acquiring your software from makes a big difference in the overall experience with contract management software because having an established track record for reliable and high-quality applications extends to customer support as well.
Customer Reviews And Testimonials: Check the vendor’s reputation by reading customer reviews and testimonials. This answers how well the software is doing in terms of performance, reliability and usability.
Support Services: Review the vendor’s support services. This encompasses the availability of technical help, response time and quality with which support is extended to you. Great customer support will lead to quick problem resolution and less downtime.
Product Updates And Improvements: By ensuring software vendors are regularly updating their programs, agents can be confident that they remain ahead of the competition. Ensure the vendor delivers updates and those are part of your subscription or licensing agreement.
9. Resource Conservation And Sustainable Practices
Selecting a manufacturing maintenance software that helps you take environmental impact and sustainability into account is becoming important.
Energy Management: A few maintenance management solutions provide functionalities that track the energy used by equipment. This knowledge gives businesses a new opportunity to identify parts of their energy usage where costs can be saved and environmental impact can be diminished.
Maintenance Efficiency: To create additional ROI for your organization and the environment, invest in software that supports sustainable maintenance practises which increases the life of machines or equipment while reducing waste.
Regulatory Compliance: Ensure that the software helps you and comply with environmental regulations and standards. This will help to avoid any legal trouble and also present an image of a responsible corporate entity.
Pros Of Choosing LLumin For Manufacturing Maintenance Software
Enabling The Future Of Maintenance Through Predictive Knowledge
LLumin moves the organization from basic, reactive solutions to preventative problem-solving and faster responses with predictive analytics. Picture the system in which you can be forewarned of possible equipment trouble before it results in an unforeseen (expensive) breakdown. As a result, armed with LLumin in your tool belt, you begin to transition from maintaining the status quo around uptime availability and overall equipment life.
Reduce Compliance Costs And Exposure To Risk
With LLumin, compliance is more than just recording and reporting. It becomes an integral part of the daily duties that lively enforce your desired state rules. On top of that, the software automatically tracks your adherence to industry standards and regulations for you. Taking strategic actions to avoid the bureaucracy can help you scale quickly and keep fines at a distance, making compliance management much less of a headache.
Your Trusted And Proven Partner For Future Manufacturing Excellence
LLumin is an investment in success. One cannot be this compliant without predictive analytics that LLumin customizes so powerfully to meet our needs. How will you not just sustain your operations, but also perform them at the highest capacity possible for continuous sustainability? Partner with LLumin and leverage the expertise in developing scalable solutions for the flexibility required by today’s manufacturers.
LLumin Pricing Plans
The software offers three pricing plans, designed around different business sizes so that each client has the best option for their budget.
Plan 1 ($540/year per user): It provides features like asset management, work order management, actual time maintenance updates and stockroom control.
With the premium plan in Plan 2: It is around $960/year per user. This comes with all the features in their professional plan at an additional integration; active directory, condition monitoring, GIS system interface, and HR management.
Plan 3: This is known as the business plan and costs $1320/year/user. This will include the premium plan features and add on more exclusive functions such as a risk management tool, and OEE utilities (dashboard & reports), and also provide project tracking features.
Interested? Request a demo!
Conclusion
For manufacturing operations, where every second is critical and accuracy can be the make-or-break for efficiency levels; your decision around maintenance software could make the difference. Choosing the proper manufacturing maintenance software allows you to tap into an entirely new level of operations excellence. This isn’t just maintaining, but changing how you maintain the whole of your maintenance strategy. You need models that give you a bigger picture simplifying the entire complex data and even suggesting some straightforward actions without overloading. Look for software that steps beyond the day-to-day and can predict potential disruptions before they hit your production line.
Enter LLumin, a game changer in equipment maintenance tracking software. LLumin’s software takes this one step further, going beyond the traditional to bring together modern technology with practical real-world usage. This is not only about tracking maintenance but it can also change how you run your entire operation.
FAQs
1. What is manufacturing maintenance software?
- A modern concept of machinery upkeep is manufacturing maintenance software. It centralizes data, schedules maintenance based on predictive analytics and can even predict when potential failures may be coming.
2. What features does manufacturing maintenance software offer?
- Its solution covers predictive maintenance, actual time equipment monitoring and alerting work order management with detailed analytics. Additionally, asset tracking, compliance management and mobile access for optimized operation are part of the solutions to improve manufacturing.
3. How can a CMMS benefit manufacturing maintenance software?
- CMMS stands above manufacturing maintenance software by bringing data together, automating schedules and augmenting reports. It provides solid ideas for operational strategies leading to better maintenance programs and crashing system downtime.
Read More From Techbullion
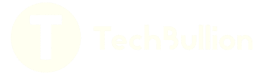