Welding machines play a vital role in various industries, enabling the joining of materials by creating a strong and permanent bond. One type of welding machine that has gained significant attention is the electron beam welder. In this article, we will delve into the use and benefits of electron beam welders and explore their significance in modern manufacturing processes.
Electron beam welders are advanced welding machines that utilize high-energy electron beams to fuse materials together. This technology is widely employed in industries such as aerospace, automotive, electronics, and medical device manufacturing. The process involves directing a focused stream of electrons onto the material, which generates intense heat and creates a molten pool. As the pool solidifies, a robust weld joint is formed, ensuring the integrity and durability of the finished product.
So, what makes electron beam welders unique and sought after? One of their primary advantages is the ability to achieve deep penetration welding. The high energy density of the electron beam allows it to penetrate even thick sections of materials, resulting in stronger welds compared to other welding techniques. This deep penetration capability is particularly beneficial in industries that require welds with exceptional strength, such as in the construction of aircraft components or critical medical devices.
Furthermore, electron beam welders offer precise control over the welding process. The focused electron beam can be precisely manipulated, enabling welders to achieve intricate and precise welds. This level of control is crucial in industries where precision and accuracy are paramount, such as electronics manufacturing. By maintaining strict control over the welding parameters, electron beam welders help minimize distortion and heat-affected zones, ensuring the integrity of delicate electronic components.
Another noteworthy advantage of electron beam welding is its ability to join dissimilar materials. Traditional welding methods often struggle to weld different types of metals or materials together due to differences in melting points and thermal expansion coefficients. However, electron beam welders can overcome these challenges. The intense and concentrated heat generated by the electron beam allows for effective joining of dissimilar materials, expanding the range of applications and design possibilities in various industries.
In addition to its technical advantages, the use of electron beam welders can also lead to cost savings in the long run. The high efficiency of electron beam welding results in reduced material waste and minimal post-welding processing requirements. Moreover, the precise and controlled nature of the process helps minimize the need for expensive rework or repairs, ultimately improving productivity and overall operational efficiency.
Conclusion
In conclusion, electron beam welders have revolutionized the welding industry by offering unique capabilities and advantages. Their ability to achieve deep penetration, precise control, and the joining of dissimilar materials make them indispensable in industries that require high-quality welds. With the potential for cost savings and increased productivity, electron beam welders continue to play a crucial role in modern manufacturing processes. Whether it is the construction of aircraft, the production of intricate electronics, or the fabrication of medical devices, electron beam welders provide a reliable and efficient solution for creating strong and durable weld joints.
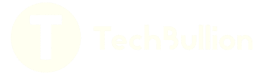