A refractory metal is a metallic element that has a very high melting point, allowing it to maintain its structure and mechanical and chemical properties at very high temperatures.
The minimum melting point to classify a metal as refractory varies, but most sources agree that the primary refractory metals are niobium, molybdenum, tantalum, tungsten, and rhenium.
Their refractory properties make these five metals incredibly useful in metallurgy and engineering, but which of the refractory metals is the most resistant to heat and wear?
Take a look below to learn more about the most refractory metals in the world.
Which metal is the most refractory?
Refractory metals are grouped together because they share properties such as high melting points and high boiling points. In addition to their heat resistance, these elements are also chemically inert, very hard, and relatively high-density at room temperature.
The table below shows some of the key properties that earn these metals their ‘refractory’ title, and a reputation for being extremely strong and stable materials.
Properties | Niobium | Molybdenum | Tantalum | Tungsten | Rhenium |
Melting point | 2,468°C | 2,610°C | 2,996°C | 3,410°C | 3,180°C |
Boiling point | 4,927°C | 5,560°C | 5,425°C | 5,660°C | 5,627°C |
Mohs hardness | 6.0 | 5.5 | 6.5 | 7.5 | 7 |
While it’s only the second most dense metal of the group behind rhenium, tungsten has the highest melting point and the highest boiling point of all the refractory metals, as well as having the highest scratch resistance on the Mohs hardness scale of 1–10.
Tungsten is known for having the highest melting point of all metals on the periodic table, not just the refractory metals group. According to Britannica, tungsten also has the highest tensile strength at temperatures above 1,650°C and the lowest thermal expansion of all metals.
This surely qualifies tungsten as the most refractory metal of them all – so it’s no surprise that tungsten is one of the most popular metals used across various industries.
Refractory metal-based alloys and carbides are used in virtually all major industries, including electronics, aerospace, automotive, chemicals, mining, nuclear technology, metal processing, and prosthetics.
The many uses of tungsten metal
Thanks to its extreme melting point and resistance to corrosion and creep deformation, tungsten can be used to fabricate parts for use in a range of challenging environments, typically starting with powder metallurgy.
Common applications of tungsten include light bulb filaments, contacts in electronic circuits, mining and drilling tools, radiation shields, counterweights, chemical catalysts, munitions, furnace components, aircraft parts, sports equipment, and even jewellery.
Tungsten can also be alloyed with other elements to lend them its refractory properties. It’s often compounded into extremely tough tungsten carbide for various machining parts – an alloy that’s second in hardness only to diamond, at 9–9.5 on the Mohs scale.
With so many uses, life as we know it wouldn’t be the same without tungsten, which is why it’s also classified as a critical raw material around the world.
Fortunately, if you’re looking for tungsten parts, it’s possible to order them online from a reputable national tungsten supplier. Available as wires, bars, crucibles, billets, and sheets, you’re sure to find tungsten in the form, size, and quantity you need.
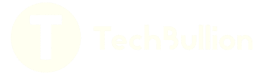