Introduction
Printed circuit boards (PCBs) are essential components in electronics that provide the mechanical structure and electrical connections for components. The two main types of PCBs are rigid PCBs and flexible PCBs (flex PCBs). Rigid-flex PCBs combine both rigid and flexible materials to create boards with both rigid areas and flexible areas.
This article will compare rigid-flex PCB to flex PCBs. The key differences include:
- Materials and construction
- Applications and use cases
- Design and layout
- Cost
Understanding these differences allows designers to select the best PCB option for their specific needs.
Materials and Construction
Rigid-Flex PCBs
Rigid-flex PCBs contain both rigid sections and flexible sections. The rigid sections are typically made of materials like FR-4, while the flexible sections use polyimide or other flexible polymer materials.
The rigid and flex sections are bonded together using adhesive layers during manufacturing. This allows the PCB to maintain rigidity for components and connections in some areas, while bending and flexing in other areas.
Common rigid-flex PCB constructions:
- Multilayer: Multiple rigid layers separated by flexible layers. Allows more complex circuitry.
- Rigid islands: Smaller rigid sections connected by flexible material. Good for discrete components.
- Flexible folds: Larger flexible areas that fold, like book binding. Useful for compact devices.
Flex PCBs
Flex PCBs use only flexible base materials without any rigid fiberglass layers. Polyimide films like Kapton are most commonly used. Flex PCBs can bend and fold repeatedly without damage.
Some constructions of flex PCBs:
- Single-layer: A simple flex PCB with one layer of copper traces. Low cost.
- Multilayer: Flex PCBs with two or more trace layers. Allows more complex circuits.
- Rigid sections: Small stiffeners added for connectors or components.
Applications and Use Cases
When to Use Rigid-Flex PCBs
Rigid-flex PCBs are ideal when:
- Both rigid and flexible connections are needed
- 3D layout and compact folding is required
- Dynamic flexing or bending during use
- Components require rigidity for stability
- High layer counts or complex circuits
Common applications:
- Wearable devices
- Medical devices
- Foldable/shape-changing electronics
- Military and aerospace systems
When to Use Flex PCBs
Flex PCBs work best when:
- Only flexible and dynamic connections are needed
- Simple circuits with fewer layers
- Tight bend radii required
- Production in high volumes
- Low-cost solution needed
Typical uses:
- Interconnects between PCBs
- Wiring harnesses and cable replacement
- Consumer electronics
- Sensors, antennas, and other discret devices
Design and Layout
Rigid-Flex PCB Design
Rigid-flex PCBs require advanced design to integrate the rigid and flex materials. Key considerations include:
- Layer stackup: Determine layer materials and order – rigid, flexible, and adhesive. More layers allow more complex routing.
- Rigid-flex interfaces: Must be well-supported to avoid separation or cracks.
- Routing: Trace routing paths between rigid and flex areas. Match lengths for optimal signal integrity.
- Flex folding: Multiple bend radii must be designed properly.
- Component placement: Ensure components are supported in rigid areas. Avoid placing on folds.
- Testing: Simulate dynamic bending and vibration during design verification.
Flex PCB Design
Designing flex PCBs is less complex with mainly flexible materials. Design priorities include:
- Bend radii: Avoid sharp folds to prevent conductor cracking and insulation damage.
- Layer stackup: Typically 1-4 layers. More layers can add costs.
- Routing: Careful trace routing for optimal flexibility and bendability.
- Components: Minimal components which can withstand flexing.
- Stiffening elements: Small rigid sections can be added if needed for strength.
- ESD protection: Additional shielding may be needed for exposed conductors.
Cost Comparison
Rigid-Flex PCB Cost Factors
Rigid-flex PCBs are generally more expensive than rigid or flex PCBs alone. Key cost drivers:
- Materials: Rigid-flex uses both rigid and flexible substrate materials.
- Layer count: Higher layer PCBs cost more, and rigid-flex often requires 10+ layers.
- Advanced design: The rigid-flex design process is more complex and time intensive.
- Low volume: Rigid-flex PCBs tend to be produced in lower volumes which increases costs.
- Testing: Extensive qualification testing is required to ensure reliability.
Typical rigid-flex PCBs range from $2,000 to $10,000 for prototype volumes depending on size, layer count, and other requirements.
Flex PCB Cost Factors
Flex PCB costs are driven by:
- Material type: Polyimide is more expensive than PET substrate.
- Layer count: Each additional layer increases cost.
- Volume: Higher volume production runs spread costs over more units.
- Complexity: More complex flex PCBs require tighter tolerances and advanced manufacturing.
- Size: Larger flex PCBs will be more expensive.
Flex PCB prototypes can range from $500 – $5,000 based on these factors. High volume manufacturing reduces per unit costs significantly.
Summary and Key Differences
Factor | Rigid-Flex PCB | Flex PCB |
Materials | Rigid and flexible materials | Only flexible materials |
Layers | Typically 8+ layers | Usually 1-4 layers |
Design | Complex to integrate rigid and flex | Simpler design focused on flex |
Use cases | Need both rigid and dynamic flex | Only flexible connections needed |
Cost | $2K – $10K for prototype | $500 – $5K for prototype |
In summary, rigid-flex PCBs provide both rigid and flexible connections for complex layouts and dynamics requirements, while flex PCBs are optimal for purely flexible interconnects in cost-sensitive applications. Carefully evaluating the design requirements and use case is important to selecting the best PCB technology.
Frequently Asked Questions
What are some examples of rigid-flex PCB applications?
Some common rigid-flex PCB applications include wearables, medical devices, military systems, aerospace avionics, robotics, and consumer electronics like cellphones and laptops. The combination of rigid and flexible regions allows these devices to package electronics compactly while maintaining flexibility and durability.
How many bending cycles can a flex PCB withstand?
Flex PCBs are typically tested to verify they can withstand a minimum of a few thousand bending cycles before failure. Factors like bend radius, conductor thickness, and material type all affect the flex life. Polyimide flex PCBs with larger bend radii could endure over 1 million cycles in some cases.
Can components be mounted directly on flex PCBs?
It is generally recommended to avoid mounting components directly on the flexible areas of flex PCBs or rigid-flex PCBs. The flexing can damage or detach conventional rigid components. Specialized flex-compatible components are available when needed, or small rigid islands can be used to mount components.
What are some best practices for rigid-flex PCB design?
Important rigid-flex design principles include managing layer stackups, designing robust rigid-flex interfaces, routing signals appropriately between rigid and flex areas, allowing sufficient bend radii for folds, strategic component placement, and extensive prototype testing to confirm reliability.
How do costs compare for prototyping rigid, flex, and rigid-flex PCBs?
For prototype volumes, rigid PCB costs typically start around $1,000, flex PCBs from $500-$2,000, and rigid-flex in the $2,000-$10,000 range. Actual costs vary widely based on size, layer count, and other factors. Volume manufacturing can significantly reduce per unit costs.
Conclusion
Rigid-flex PCBs fill an important niche for electronics needing both rigid support and dynamic flexing. They combine the best of rigid and flex PCBs for complex layouts and unique applications. Flex PCBs provide simpler and lower cost flexible interconnects when the circuitry allows. As PCB technology continues evolving, rigid-flex and flex PCBs will enable ongoing innovation in cutting-edge electronic devices and systems.
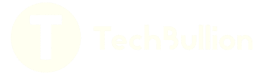