When it comes to milling, there are two primary techniques: climb milling (down milling) and conventional milling (up milling). Both methods have their unique applications and come with distinct advantages and disadvantages. You had better know the differences for choosing the right milling strategy, especially when dealing with different materials or machine conditions.
Climb Milling (Down Milling)
In climb milling, the direction of the cutter’s rotation is the same as the feed direction of the workpiece. The cutting action begins with the maximum thickness and gradually decreases as the cutter passes through the material. It is commonly used when the machine has no backlash and the workpiece does not have a hardened surface.
Advantages of Climb Milling:
Better Surface Finish: because the cutting forces push the workpiece down, reducing vibrations and improving stability during the process.
Longer Tool Life: Since the cutting forces are lower, the wear on the tool is minimized. Therefore, it can extend longer tool life, which can save costs over time.
Lower Power Consumption: Due to the smoother cutting process, power consumption is typically 5% to 15% lower than in conventional milling.
Efficient Chip Removal: In climb milling, chips are pushed behind the cutter, making chip removal more efficient, which is especially useful when working with soft materials like aluminum alloys.
Suitable Materials for Climb Milling:
– Aluminum: Aluminum alloys, due to their softness and ease of cutting, respond well to climb milling.
– Magnesium: Like aluminum, magnesium alloys benefit from the smoother cutting process.
– Titanium and Heat-Resistant Alloys: Although these are harder materials, the advantages of climb milling can still make it a preferred option
Conventional Milling (Up Milling)
In conventional milling, the cutter rotates in the opposite direction of the feed. The cutter engages the material at a minimal thickness and gradually increases the thickness of the cut. It is often used for hardened surface layer on the workpiece or when the machine has some level of backlash.
Advantages of Conventional Milling:
Avoids Tool Damage on Hard Surfaces: If the workpiece has a hard skin or irregular surface, conventional milling is safer. The cutting teeth first engage with the already-machined surface, reducing the chance of tool damage from surface imperfections.
Better for Machines with Backlash: If the milling machine has a worn feed mechanism or some level of backlash, conventional milling can prevent unwanted movement of the worktable.
Effective for Tougher Materials: Conventional milling is ideal for materials that could challenge the tool’s integrity in climb milling, such as forged parts with hardened surfaces or materials prone to chipping. Now that we’ve covered the benefits of Climb Milling vs. Conventional Milling, let’s look at their key differences.
Key Differences Between Climb and Conventional Milling
– Tool Engagement: In climb milling, the tool engages the material from the top surface, cutting the full depth from the start. In conventional milling, the tool initially skims the surface before gradually cutting deeper.
– Force Direction: In climb milling, cutting forces push the workpiece downward, helping to keep it in place. In conventional milling, the forces lift the workpiece, which may require more robust clamping.
– Heat Generation: Conventional milling tends to generate more heat due to the increased friction as the tool slides before cutting.
Climb and Conventional Milling Comparison:
Item | Climb Milling | Conventional Milling |
Cutting Thickness | From thick to thin | From thin to thick |
Slippage | None | Exists |
Tool Wear | Slow | Fast |
Surface Hardening Phenomenon | None | Exists |
Action on Workpiece | Presses down | Lifts up |
Eliminates Backlash in Screw & Nut Gap | No | Yes |
Vibration | Large | Small |
Power Consumption | Low | 5% to 15% higher |
Surface Roughness | Good | Poor |
Suitable for | Finishing | Roughing |
How to Choose Between Climb and Conventional Milling
Climb Milling:
– Best for Smooth, Soft Materials: When working with soft metals like aluminum or magnesium, climb milling offers a better finish and longer tool life. The cutting forces are directed downward, reducing vibrations and improving stability.
– Efficient for Low-Power Machines: Due to its lower power consumption, climb milling is an excellent choice for machines with limited horsepower.
– Ideal for Backlash-Free Machines: If the machine has no backlash, climb milling is preferable because it prevents issues like tool deflection or movement of the worktable.
Conventional Milling:
– Best for Tough Surfaces: When the workpiece has a hard surface layer, such as from forging or casting, conventional milling helps avoid damage to the tool.
– Better for Older Machines: Machines with backlash or less rigid setups benefit from conventional milling, as it reduces the risk of worktable movement during the cut.
– Suitable for Irregular Surfaces: If the workpiece surface is uneven, conventional milling offers more control and prevents the tool from being damaged by sudden changes in cutting conditions.
Power Consumption and Chip Removal
Compared to conventional milling, the cutting forces in climb milling are more consistent and directed downward, which reduces the machine’s power requirements by up to 15%. Therefore, climb milling is more energy-efficient, especially in large-scale production.
Additionally, climb milling is good at chip removal. Since the chips are pushed behind the cutter, they do not interfere with the cutting edge, leading to a cleaner and more efficient process. In contrast, conventional milling tends to push chips in front of the tool, which can cause re-cutting of the chips, negatively impacting surface finish and tool life.
Surface Finish and Tool Wear
Surface finish is generally better in climb milling. The reason is that the cutting teeth engage with the material in a way that minimizes friction and heat generation, leading to a smoother surface. In conventional milling, the tool tends to rub against the material before cutting, which can lead to increased friction, heat, and a rougher surface.
In terms of tool wear, climb milling is gentler on the cutting edges. The cutting forces are directed downward, reducing the impact on the tool and prolonging its life. Conventional milling, on the other hand, subjects the tool to more abrasive forces, particularly on hardened surfaces, which accelerates wear and reduces tool life.
Conclusion
In summary, both climb milling and conventional milling have their application, and you should consider several factors when choose them.
We have guide you these differences, we hope it can help you make more informed decisions when setting up your milling operations.
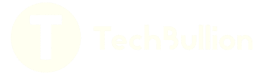