Medical injection molding is a manufacturing process used to produce high-precision medical components by injecting molten medical-grade plastics into molds. This process is essential for producing a wide range of medical devices, ensuring that they are durable, sterile, and precise. It’s a highly efficient, cost-effective method, capable of producing parts with intricate designs and tight tolerances, making it ideal for the medical industry, where quality and reliability are critical.
Process Overview
- Material Selection:
The process starts with the selection of medical-grade plastic materials, which are typically chosen for their biocompatibility, durability, and resistance to sterilization methods. Common materials include polyethylene (PE), polypropylene (PP), polyetheretherketone (PEEK), and silicone, all of which meet the stringent regulatory standards for medical devices. - Melting the Plastic:
The selected plastic material is fed into a hopper, where it is heated to its melting point in an injection molding machine. The plastic is typically in the form of small pellets, which are melted into a liquid state using high temperatures. - Injection into Mold:
Once the plastic has reached the required viscosity, it is injected into a mold under high pressure. The mold is a precise cavity designed to form the shape of the medical component. The injection process ensures that the material fills the mold completely, forming the desired component shape with high precision. - Cooling and Solidifying:
After the plastic has been injected, the mold is cooled, causing the plastic to solidify. The cooling rate must be controlled carefully to avoid defects such as warping or incomplete curing. - Ejection and Inspection:
Once cooled, the mold is opened, and the finished component is ejected. The component is then subjected to a series of inspections to ensure it meets the required quality standards. This may include dimensional checks, surface finish evaluations, and tests for any potential defects. - Post-Processing (if required):
Depending on the complexity of the part, additional post-processing steps such as trimming, polishing, or sterilization may be required. This ensures that the final product is ready for use in medical applications, meeting both functional and safety standards.
Types of Medical Devices Produced
Medical injection molding is widely used to produce a variety of medical components, ranging from everyday items like syringes to more complex devices such as surgical implants. This process, particularly when performed using Precision Mold Medical techniques, ensures that all parts meet the highest standards of quality and precision. Below are some key examples of medical devices produced through this method:
- Surgical Implants:
Surgical implants, such as knee and hip joint replacements, often require precision molding. Materials like PEEK and titanium composites are commonly used to create strong, durable components that are compatible with the human body. These parts need to be precise and meet stringent regulatory requirements to ensure they function correctly in the human body. - Syringes:
Medical syringes are produced in high volumes using injection molding. The process ensures that each syringe is uniform and meets the required standards for sterility and functionality. Plastic syringes are often made from materials such as polypropylene (PP), which is strong and resistant to chemical degradation. - Catheters:
Injection molding is used to create catheters, which are medical devices used to carry fluids into or out of the body. The molding process ensures that the catheters have a smooth surface finish, flexible nature, and precise dimensions to avoid complications during use. - Knee and Hip Joint Replacements:
Joint replacements are complex medical devices that are often produced using injection molding. These components must be extremely precise to ensure proper alignment and function when implanted in the body. Materials like PEEK or medical-grade silicone are commonly used, as they are biocompatible and provide the necessary strength and flexibility. - Blood Bags:
Medical-grade plastic materials are molded into blood bags that can safely store and transport blood. The molding process ensures that the bags are leak-proof, durable, and able to withstand sterilization procedures. Materials such as polyvinyl chloride (PVC) are commonly used for blood bags due to their transparency and durability. - Needles and Other Injection Devices:
Small, high-precision components like needles, lancets, and infusion sets are produced using injection molding. The accuracy of the molding process ensures these components are safe for use in medical procedures. Stainless steel may be integrated into some parts (such as the needle tips) through insert molding. - Diagnostic Instruments:
Injection molding also plays a key role in the production of diagnostic devices, such as Petri dishes, test tubes, diagnostic trays, and other laboratory equipment. These devices require precision and high-quality materials that do not interfere with test results. - Dental Devices:
Devices such as dental implants, dentures, and orthodontic brackets are often produced using injection molding. The precision of the process is essential to ensure that these components fit correctly and function as intended. - Personal Protective Equipment (PPE):
With the global focus on health and safety, injection molding is also used to create components for PPE, such as face masks, face shields, and gloves. The molding process ensures that these items are produced in high volumes, with consistent quality and precision.
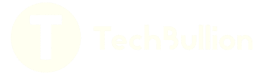