Induction motors are the backbone of modern industry, handling about one-third to one-half of the electrical machines used in industries today, either as the main driver or support. In this post, we’ll break down the basics of what an induction motor is, how it works, and the different types, so you can get a good overall idea of these essential machines. Among all electric motors, induction motors are the most common.
What is an Induction Motor?
Induction motors work on the principle of electromagnetic induction. This is when an electric current is induced in the rotor due to the magnetic field created by the windings in the stator. Simply put, the motor has two main parts:
Stator: The fixed part of the machine, which has coils that generate a rotating magnetic field when AC (alternating current) is applied.
Rotor: The part that rotates inside the stator. It can be either a squirrel cage type or a wound type.
The magnetic field from the stator interacts with the currents induced in the rotor, creating torque on the shaft, which causes the rotor to spin. This is thanks to a magnetic field in the rotor that rotates in the opposite direction.
How Does an Induction Motor Work?
An induction motor works based on Faraday’s law of electromagnetic induction and Lenz’s law. Let’s break it down step by step:
AC Supply to Stator: When AC voltage is applied to the stator windings, it creates a rotating magnetic field (RMF) around the stator. This field spins at what’s called synchronous speed (Ns), which depends on the frequency of the AC supply and the number of poles in the motor.
Induction in the Rotor: The rotating magnetic field crosses the air gap and cuts through the rotor conductors. According to Faraday’s law, this induces an electromotive force (EMF) in the rotor. Since the rotor is a closed circuit, it causes currents to flow in the rotor.
Production of Torque: The currents induced in the rotor create their own magnetic field. This field interacts with the rotating magnetic field from the stator. Based on Lenz’s law, the rotor starts turning in the same direction as the stator’s magnetic field to reduce the difference between them. This interaction generates the torque that makes the rotor spin.
Asynchronous Operation: The rotor never quite catches up to the speed of the stator’s magnetic field (the synchronous speed) because if it did, there would be no relative motion, no induced EMF, and no current in the rotor. This difference between the rotor speed and synchronous speed is called slip.
Types of Induction Motors
Induction motors come in different types based on the rotor type and the number of phases. Let’s take a look:
Based on Rotor Type:
Squirrel Cage Induction Motor: This motor has a rotor made of conductive bars that are shorted at both ends with end rings, creating a cage-like structure. It’s the most common type because it’s simple, tough, low-cost, and reliable. But it has limited starting torque and not much speed control.
Wound Rotor Induction Motor: This one has a rotor with windings similar to the stator and is connected to external resistors or controllers via slip rings. This design gives better control over starting torque and speed, making it great for applications that need variable speed or high starting torque. However, it’s more expensive and needs more maintenance.
Based on the Number of Phases:
Single-Phase Induction Motor: You’ll find these in homes and small businesses where three-phase power isn’t available. They’re used in things like household appliances, fans, and small machines. Since single-phase motors don’t produce a rotating magnetic field at startup, they need extra help to start, like capacitors or auxiliary windings.
Three-Phase Induction Motor: These motors are the go-to for industrial and commercial use because they’re efficient, reliable, and can create a self-starting rotating magnetic field. They don’t need any external starting mechanism and can handle bigger power loads.
Advantages of Induction Motors
There are several perks to using induction motors, and here are a few:
Simplicity and Durability: Since they have fewer moving parts, induction motors are less likely to break down and don’t need a lot of maintenance.
Cost-Effective: They’re cheaper to make and keep up compared to other motor types.
High Efficiency: Especially when running at full load, induction motors are super efficient, which means you can save on energy.
Versatile: These motors can be used pretty much anywhere—from big industrial settings to home appliances.
Disadvantages of Induction Motors
Even though induction motors have a lot of advantages, they also come with some downsides. Here are a few:
Limited Starting Torque: Induction motors, especially the squirrel cage ones, have lower starting torque. This makes them a poor choice for tasks that need a lot of torque at the start, like cranes or heavy machinery, unless you add something like capacitors or special starters.
Poor Speed Control: It’s harder to control the speed of an induction motor compared to a DC motor. While you can use methods like Variable Frequency Drives (VFDs), they add cost and complexity. Simple methods like adjusting voltage don’t work very well for precise speed control.
High Inrush Current: These motors draw a lot of current when they start, sometimes several times their full-load current. This can cause voltage drops and may require special starting methods (like star-delta or soft starters) to handle it.
Lower Power Factor: Induction motors tend to operate at a lower power factor, especially when they’re not running at full load. A lower power factor means they use more apparent power, which could lead to higher electrical bills. You might need to add power factor correction devices, which will cost extra.
Dependence on Slip: The motor’s speed is affected by the slip—the difference between the synchronous speed of the magnetic field and the actual speed of the rotor. This means you can’t control the speed very precisely, and it might vary depending on the load. Keeping a constant speed under different loads can be tricky without advanced control systems.
Application of Induction Motors
Induction motors are super tough and efficient, which is why they’re used in all sorts of applications. Here are some common places you’ll find them:
Industrial Drives: These motors are used to power things like conveyors, pumps, compressors, and other big industrial machines.
HVAC Systems: They drive fans and blowers in heating, ventilation, and air conditioning systems.
Household Appliances: Single-phase induction motors are found in washing machines, refrigerators, air conditioners, and a lot of other home appliances.
Electric Vehicles: Lately, induction motors have been showing up more and more in electric vehicles because they’re reliable and efficient.
Conclusion
Induction motors, with their simple design and dependable performance, are crucial in both industrial and home settings. If you understand how they work, the different types, and how to handle things like starting methods and speed control, you can pick the right motor for the job and get the best performance. As technology keeps advancing, these motors are getting even more efficient and versatile, keeping their place as a key part of modern electrical engineering.
Related Articles
The Difference Between Linear and Tactile Switches
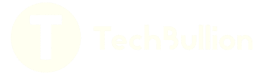