Anodized aluminum is a surface treatment that converts the aluminum backing into a protective and corrosion-resistant oxide. In this process, aluminum is placed in an electric bath and electrolyzed. Consequently, the aluminum oxide layer on the steel surface is increased. Not only is this oxide layer incredibly durable but it can also be customized in terms of color and texture.
How is Aluminum Anodized?
Anodizing is an electrochemical process that increases the natural oxide content of aluminum surfaces. Here’s a step-by-step breakdown of how to anodize aluminum:
1. Cleaning:
Before anodization begins, the aluminum surface must be thoroughly cleaned to remove dirt, oil, and oxide debris. This is usually done with an alkaline or acidic cleaner.
2. Pre-Treatment:
After cleaning, the aluminum is subjected to a pre-treatment step, which involves etching the surface to create a uniform, microscopically rough texture. This step ensures that the anodized layer will adhere properly to the aluminum.
3. Anodization:
The purified and pretreated aluminum is placed in an electrolyte bath usually containing sulfuric acid. A direct upward flow of water passes through the aluminum, reacting oxygen ions on the aluminum surface to form an aluminum oxide layer This oxide layer is what gives anodized aluminum its unique properties.
4. Coloring:
During the anodization process, it is possible to introduce color to the aluminum by using organic or inorganic dyes. This step allows for a wide range of custom color options, making anodized aluminum popular for decorative and architectural purposes.
5. Sealing:
After anodization and, if applicable, coloring, the aluminum is sealed to close the pores of the oxide layer. This further enhances the corrosion resistance and durability of the material.
The Benefits of Anodized Aluminum
1. Corrosion Resistance:
One of the primary reasons for anodizing aluminum is its remarkable corrosion resistance. The anodized layer acts as a barrier that protects the underlying aluminum from environmental factors like moisture and chemicals. This property makes anodized aluminum ideal for outdoor applications and industries where exposure to harsh conditions is common.
2. Durability
Anodized aluminum is significantly more durable than untreated aluminum. The anodization system hardens the surface, making it extra abrasion-resistant and less liable to corrosion. This sturdiness extends the lifestyles of anodized aluminum products.
3. Custom Color Options
Anodized aluminum gives a wide variety of color opportunities. Whether you want a specific color for branding or need it to in shape a present design, the anodization method offers particular shade control. This material is particularly valuable in industries such as construction and automobile manufacturing.
4. Light Weight
Despite the added layer of oxide, anodized aluminum retains its lightweight properties. This makes it a preferred choice in industries like aerospace and transportation, where weight considerations are crucial.
5. Cost
While anodization does add value to the manufacturing of aluminum products, the lengthy time period blessings regularly outweigh the preliminary investment. Its extra durability and corrosion resistance lessen renovation and substitute expenses, making it a more cost-effective option in the long run.
Applications of Anodized Aluminum
The versatility and durability of anodized aluminum have led to its widespread use in various industries. Here are some common applications:
1. Architecture:
Anodized aluminum is a popular choice in architectural design. It is used for cladding, curtain walls, and other exterior elements of buildings. The custom color options and corrosion resistance make it an attractive material for both aesthetics and durability.
2. Aerospace:
In the aerospace industry, weight savings are critical. Anodized aluminum provides a lightweight yet robust solution for aircraft components, ensuring safety and fuel efficiency.
3. Automotive:
Anodized aluminum is employed in automotive parts and accessories. It enhances the appearance of wheels, trim, and grilles while providing protection against road salt and other environmental factors.
4. Electronics:
The electronics industry uses anodized aluminum for components like cases, heat sinks, and connectors. Its resistance to electrical conductivity and corrosion are advantageous in this field.
Can Materials Other Than Aluminum Be Anodized?
While anodization is most commonly associated with aluminum, it is possible to apply this process to other metals, including titanium and magnesium. The key difference lies in the specific electrolyte solutions and process parameters used for each material. However, the benefits of anodization, such as corrosion resistance and improved durability, can also be achieved with these metals.
Conclusion:
Anodized aluminum is a remarkable material that enhances the properties of regular aluminum, making it corrosion-resistant, durable, customizable, lightweight, and cost-effective. Its unique characteristics have earned it a prominent place in various industries, from architecture to aerospace, electronics to cookware. Whether you encounter anodized aluminum in a building’s exterior or the cookware in your kitchen, its presence reflects the exceptional qualities achieved through the anodization process.
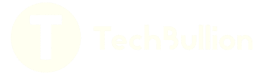