Industrial grade inductive proximity sensors are tough, reliable devices used in factories and other industrial settings to detect metal objects without touching them. These sensors are built to withstand harsh conditions and work consistently in busy, noisy environments. They play a crucial role in automation, safety systems, and quality control processes. This guide will explain what makes these industrial grade inductive proximity sensor special, how they work, and why they’re so important in modern industry.
The Basics of Inductive Proximity Sensors
These sensors work by creating a magnetic field and detecting changes in it. When a metal object gets close, it disrupts this field. The sensor notices this disruption and sends a signal. It’s like having an invisible bubble around the sensor that can feel when metal enters it.
Industrial grade sensors are beefed-up versions of regular proximity sensors. They’re designed to keep working even when exposed to oil, water, dust, and extreme temperatures. This makes them perfect for use in places like car factories, food processing plants, and mining operations.
Key Features of Industrial Grade Sensors
What sets these sensors apart is their durability. They have tough metal or plastic casings that can take a beating. Many are sealed tight to keep out water and dust. This means they can be power-washed or work in dirty environments without breaking.
These sensors are also made to be very precise and reliable. They can detect metal objects consistently, even when things are moving fast. Many can work millions of times without wearing out. This is important in places where machines are running all day, every day.
How They’re Used in Industry
Factories use these sensors all over the place. They might be part of an assembly line, making sure parts are in the right place before a machine starts working. In packaging plants, they can count products or check if boxes are full.
These sensors are also used in safety systems. They can tell if a machine guard is in place or if someone’s hand is too close to a dangerous area. In warehouses, they help with inventory by detecting when metal containers are moved or stacked.
Different Types for Different Jobs
There are several types of industrial grade inductive proximity sensors. Some are small and can fit in tight spaces. Others are bigger and can detect metal from further away. The shape and size depend on where they’ll be used and what they need to detect.
Some sensors are extra sensitive and can detect tiny pieces of metal. Others are made to ignore small bits and only react to larger objects. There are even sensors that can tell the difference between different types of metal.
Installation and Maintenance
Putting in these sensors is usually straightforward. Most can be bolted or clamped into place. But it’s important to install them correctly. They need to be the right distance from what they’re detecting, and away from things that could interfere with them.
Once installed, these sensors don’t need much care. They don’t have moving parts, so they don’t wear out easily. But it’s a good idea to check them regularly to make sure they’re clean and working right. Sometimes they might need to be adjusted if the setup of the machinery changes.
Advantages Over Other Sensing Methods
Industrial grade inductive proximity sensors have some big advantages. Unlike some other types of sensors, they don’t need to touch what they’re detecting. This means they last longer and can work in situations where physical contact isn’t possible or safe.
They’re also not affected by dirt, oil, or non-metallic materials. This makes them more reliable than some optical sensors that can get confused by dust or bright lights. And because they use simple magnetic fields, they’re often cheaper and easier to use than more complex sensing systems.
Choosing the Right Sensor
Picking the right sensor depends on the job. You need to think about things like how far away the metal will be, how big it is, and what kind of metal it is. The environment matters too – is it wet, dusty, or very hot or cold?
It’s also important to consider how fast things will be moving and how precise the sensor needs to be. Some jobs need sensors that can detect things very quickly or tell the difference between objects that are very close together.
The Future of Industrial Sensing
As factories get smarter, these sensors are evolving too. Newer models can connect to computer networks, making it easier to monitor and control them from far away. Some can even diagnose problems with themselves, letting maintenance teams know when they need attention.
Engineers are working on making sensors that use less power and can detect even smaller changes. As industry moves towards more automation and precision, these little devices will play an even bigger role in keeping everything running smoothly.
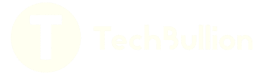