In many of today’s cutting-edge technical developments, what fundamental technique serves as a foundation?
One thing unites 3D printing, robotics, and new forms of transportation: they are frequently propelled by planetary gear motor. Planetary gear systems, also referred to as epicyclic gear systems, initially seem to be fairly complicated. Undoubtedly, the complex components of creating this kind of gear system require the expertise of a qualified gear engineer.
If you’re seeking a rudimentary grasp of planetary or epicyclic gearboxes, this article gives you the specific information you need.
What is Planetary Gearbox?
Input and output shafts must be aligned in a gearbox to be considered planetary gear or epicyclic gearbox. To transmit the highest torque in the smallest possible form (known as torque density), a planetary gearbox is used.
A fantastic illustration of a planet-wheel system is the hub for acceleration on a bicycle.
Ever questioned how such a small hub could contain so much strength and capability?
One-stage planetary gear systems are utilized for three-speed hubs while two-stage systems are used for five-speed hubs. There is reduction, direct, and acceleration states in every planet gear system.
The mathematical expressions for the minimum and maximum reduction ratios are 3: l and 10:1, correspondingly. When the ratio is less than 3, the sun gear becomes excessively huge in relation to the planet gears. The sun wheel becomes excessively short as the ratio goes over 10, which reduces the torque. The ratios are often absolute, or integers.
Main components of Planetary Gearbox
The mechanism that generates several gear ratios using the same set of gears is known as a planetary gear set. There are three essential components to every planetary gearbox:
- The sun gear (central part)
- The ring gear (outer component)
- The planet gears and the carrier for the planet gears
These three elements can all be held stationary, used as inputs or outputs, or both. The gear ratio for the gear set is decided by selecting which component performs which function.
The table lists these configurations together with the power and speed outputs they provide.
Types of Planetary Gearbox
Based on their performance, planetary gearboxes come in three primary varieties: shaft output, wheel drive, and spindle output. Here are some details about them and how they work.
- Shaft Output
The planetary components that are located nearby are driven by the sun gear and are housed in a shaft drive gearbox’s turning carrier. By providing drive to the shaft through a rotating carrier, the ring component is kept fixed. The system’s housing component, which produces a turning shaft, is directly fixed to the machine. An output of 113,000 Nm is possible from a shaft output gearbox.
- Wheel Drive
In a wheel-drive planetary gearbox, the sun gear drives the planetary components that surround it and are fastened to a carrier. The planet gears move the outer ring gear when the sun gear is operating. The system’s housing can accommodate a combination of wheels. The functionality of the system can be maximized by connecting the wheel directly to the gearbox. Planetary gearboxes for wheel drive can handle torques of up to 332,000 Nm.
- Spindle Output
Even though the output is given as a flange, spindle output planetary gearboxes operate in the same way as shaft outputs. The planetary spindle drive types are suitable for applications requiring up to 113,000 Nm of torque.
How does Planetary Gearbox work?
The planetary gearbox is one type of gearbox that satisfies all the modeling requirements for servo applications while offering comparatively extended performance lifetimes and minimal maintenance requirements. This is because planetary gearboxes have a smaller overall footprint than other device types while yet offering excellent torque transmission, adequate rigidity, and low noise.
A “sun” gear, also referred to as a central gear, is located in the middle of the planetary gearbox, as was previously mentioned. The input component is always this. Two or more “planet” components, also known as outer gears, are present around the outside. There is a ring element surrounding the planet’s constituent parts, which completes the creation. A carrier connects the planet gears, and the carrier is united by the output shaft.
The planetary or epicyclic gearbox is made up of a carrier, the planetary gears, an outer ring with teeth that face inwards, commonly referred to as an internal gear, and the sun gear in the center. The solar gear spins when power is applied. The standard by which the planetary gears mesh with the sun gear determines how the sun gear revolves, and vice versa.
The planetary gears also spin around the sun gear since they are proportional to the ring section, which is fixed. The carrier maintains the planetary gears’ fundamental structure and establishes their gaps. It incorporates the output shaft and rotates with the planetary components.
Applications of Planetary or Epicyclic Gears
Planetary gearing is perfect for special applications because of its high ratio potential, modular construction, and durability. Some of the main applications or usage of these Planetary or Epicyclic Gears include:
- These gears can be used in wheel drive motors, industrial transporting applications, automotive and off-road gearboxes, and more.
- Even a seemingly straightforward application, such as the shifting mechanism on a bicycle, employs planetary gearing.
- They can be coupled to electric motors or utilized as a powertrain between internal combustion engines.
- Planetary gears, particularly in the industrial setting, are used to power forestry applications such as log decks, debarking machinery, sawing machinery, pulp washers, and vacuum filters.
- Steel mills, phosphate industries, conveyors, mixers, and drums for asphalt and cement all make use of planetary gear drives.
Planetary or Epicyclic Gear Systems: Benefits and Drawbacks
Benefits
The planetary gearbox has several benefits that set it apart from more conventional gear types like helical and parallel shaft gearboxes, making it an intriguing substitute in situations requiring:
- With a high torque gearbox, it is small and light.
- On the output shaft, high radial loads
- Increased reduction ratios
- It operates more quietly.
- Since all gears are constantly in the mesh, switching from one gear to another is possible without suffering any loss.
- Distributing the load evenly among all gears with more contact points.
Drawbacks
- The gear assembly is only possible for certain tooth-to-gear ratios.
- Complexity
- To prevent adding additional gearing, the driver and propelled equipment must be lined up.
- Efficiency calculations might be challenging.
Selecting the right Planetary Gearbox for your need
The outcome should be taken into consideration while choosing a planetary gearbox’s gearing size and ratio. Efficacy, design, pricing, and functionality all need to be balanced carefully. A consultative approach to modeling is used by well-known constructors. They start every project by creating deep learning of the specific situation, the torque, speeds, and machine performance.
They also evaluate and offer suitable, dependable, and economical planetary gearbox technology using their knowledge and experience. They guarantee years of trouble-free operation for every gearbox they offer. They remain at the cutting edge of planetary gearbox technology thanks to a constant stream of innovation and outstanding engineering.
Conclusion
Hence, Planetary gear systems have several benefits, including inertia, torque density, and compactness. Planetary concepts have received a lot of attention recently as a result of these attributes. Mechanical engineers can be confident that planetary gear units will continue to be utilized in a very broad range of machinery, engines, and automated systems in the future.
FAQS
- Why use Planetary Gearbox?
Due to the three planets’ gears’ uniform distribution around the sun, planetary gearing is used in tough applications. They can withstand greater torques and cutbacks in a smaller, more compact design because they are more resilient and power-dense. Additionally, planetary gears are a versatile, strong, and tough gear set that power a variety of industries under challenging circumstances and severe shock loads.
- What Planetary Gear options do we have?
There are 1-speed and 2-speed planetary or epicyclic gearbox variants available. To meet any situation, professional manufacturers can provide single, double, or triple sets. Within the limitations of planetary gears, they can also integrate hydraulic, dynamic, and electromagnetic brakes.
- Can we use a Planetary gearbox with a Servo Meter?
The main benefit of using a planetary gearbox with a servo motor is that the torque is distributed over three gears (the planet portions), which results in a torque that is nearly three times greater than that of a “normal” gearbox at the same dimensions.
Our Takeaway!
We hope you find the information we’ve provided best planetary gearboxes in China. If you have any questions about planetary gear motor, feel free to contact Doncen Motor. Our engineers are willing to working with you!
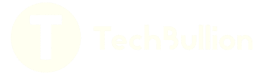