We’ve seen plastic seats made of molded plastic and metal hardware in the past, but today’s plastic seats are much more advanced. They are made from high-density polyethylene (HDPE), durable and lightweight plastic. However, the manufacturing process of these chairs is quite complex and requires specialized equipment to produce a high-quality product. Plastic seat production is a customer group we often interact with, so today, we would like to share with you what processes are involved in the production of plastic seats.
Production of plastic seats first requires plastic particle processing!
Plastic pellet processing is the first step in producing plastic chairs. It involves breaking down large pieces of plastic into smaller pieces and forming molds. Benefits of plastic pellet processing include Improved quality control by allowing you to see what the final product will look like before molding. This allows any errors or issues in your design to be corrected before they become too costly or time-consuming. After plastic granule processing, high-quality plastic granules suitable for plastic injection molding machines can be obtained for further production of plastic seats. These processed particles can significantly improve product quality.
Then, perform injection molding!
The pretreated plastic particles are put into the injection molding machine, and the molten plastic material is injected into the mold through heating and high-pressure injection, where various seat parts are formed. This can be done at high pressure and temperature or both. In some cases, you may only want to use one tool for injection molding; in other cases, you will need two different types of equipment: one for heating the material and another for shaping the material for the final shape. When choosing between these options, it is essential to consider which material you are working with before deciding which parts should be fixed or rotated at this production stage.
The Production of plastic seats also requires cooling and solidification!
The production of plastic chairs also requires cooling and solidification. This process is critical to the quality of plastic seats. It may take up to 24 hours; however, this time frame depends on the size of your company’s facility. Cooling involves cooling the molten plastic with water to make it hard enough for cutting and trimming. After completing this step, assembly begins by assembling parts such as legs, arms, and others using screws or bolts.
By cutting and trimming!
Plastic seat production also requires cutting and trimming. Machines can do this process, but there are two methods. The cooled and solidified plastic seat parts are cut out and decorated, removing excess material. The first method uses a CNC cutter, which cuts the seat’s shape out of a large piece of plastic. The second option is to use a hand tool like scissors or a knife to cut your body out of smaller sheet pieces and assemble them into one large piece. Sometimes, the two methods are suitable for use in combination.
Finally, the different Production of plastic seats are assembled!
After the previous process, the assembly sequence is determined. The plastic seat parts’ assembly sequence and corresponding positions are determined according to the product design and process requirements. After being joined together using the appropriate parts, this process may require adjustments and positioning to ensure the seat is stable and meets design requirements. Finally, the details are improved, and the final inspection determines the quality! Of course, different products will have other processes and require other assembly processes!
In the end
We hope this article gave you a better understanding of the processes involved in producing plastic seats and what is required. We at Topstar can provide the production line equipment mentioned above to everyone. Let everyone better control the quality of products and create more good products!
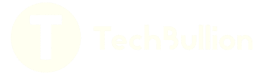