When dealing with sophisticated machinery, such as an electric rotary actuator, ensuring it operates efficiently and reliably over its service life is paramount. This is particularly crucial as more industries begin to rely on these devices for precision and control in various applications, from manufacturing to aerospace. Proper maintenance of these actuators prolongs their life and enhances their performance and reliability. This article explores advanced maintenance techniques that are vital for anyone looking to maximize the potential of their electric rotary actuators.
Understanding Electric Rotary Actuators
Electric rotary actuators are devices that convert electrical energy into rotational motion. They are used in various applications where precision, efficiency, and control are required. Unlike their pneumatic and hydraulic counterparts, electric rotary actuators offer better energy efficiency, precision, and easier integration with digital control systems.
The Importance of Regular Inspections
Routine inspections are a cornerstone of effective maintenance for electric rotary actuators. These inspections should focus on checking for signs of wear and tear, ensuring that all electrical connections are secure, and assessing the condition of mechanical components like gears and bearings. Early detection of potential issues through regular inspections can prevent costly downtime and repairs.
Calibration and Testing
Regular calibration and performance testing are critical to maintaining the accuracy and functionality of electric rotary actuators. These procedures ensure that the actuators perform as expected under varying operational conditions. Calibration involves adjusting the actuator’s control systems to ensure they meet the precise requirements of specific applications, while testing evaluates the actuator’s response to commands and its ability to maintain performance over time.
Enhancing Performance with Software Updates
With the advancement in actuator technology, many electric rotary actuators are now equipped with software that controls and monitors their operation. Keeping this software updated is crucial as updates often include improvements in performance, new features, and bug fixes that enhance the actuator’s functionality.
Predictive Maintenance Techniques
The integration of sensors and monitoring software in electric rotary actuators allows for predictive maintenance, a technique that uses data-driven insights to predict when maintenance should be performed. This approach helps prevent failures before they occur by analyzing data trends such as temperature, vibration, and operational cycles to schedule maintenance more effectively.
Implementing Advanced Diagnostic Tools
Advanced diagnostic tools play a critical role in maintaining electric rotary actuators. These tools can detect anomalies in electrical signals, mechanical performance, and other critical parameters. By using these tools, technicians can quickly identify issues that might not be visible during regular inspections.
Sustaining Actuator Health and Longevity
To extend the life and performance of electric rotary actuators, implementing a comprehensive maintenance strategy that includes lubrication, alignment checks, and timely replacement of worn-out parts is essential.
Importance of Proper Lubrication
Lubrication reduces friction and wear in the moving parts of an actuator, which is vital for the longevity and efficiency of the device. Using the correct type of lubricant and following the manufacturer’s recommendations for application intervals ensures optimal performance.
Routine Replacement of Critical Components
Over time, certain components of an electric rotary actuator such as seals, bearings, and gears may wear out and need replacement. Establishing a routine replacement schedule for these components can prevent unexpected failures and extend the actuator’s operational life.
Keeping a Maintenance Log
Maintaining a detailed log of all maintenance activities performed on an electric rotary actuator provides valuable insights into the device’s operational history. This log can help identify recurring issues, track the frequency of maintenance tasks, and plan future maintenance activities more effectively.
Conclusion
Advanced maintenance techniques for electric rotary actuators are critical for ensuring these components meet their performance and durability expectations. By understanding the basics of actuator operation, implementing regular inspections and testing, updating software, utilizing predictive maintenance, and performing routine hardware checks, you can significantly enhance the reliability and efficiency of your electric rotary actuators. Properly maintained, these devices can provide superior performance that supports a wide range of industrial applications, driving productivity and reducing operational costs.
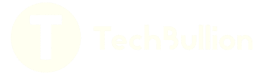