Most present-day contractors are focused on the perfect resource management strategies that will help them with the allocation of all the required assets at once. For this purpose, digital tools are applied and integrated into the existing corporate systems. For example, software for building estimation brings 100% control over planned costs. And this is about well-thought resource management. Because estimating labor, equipment, facility, and supply costs will be automated.
What Are Construction Resources to Manage?
There are four main construction resources to manage. If you pay attention to each aspect while developing your management strategies, the perfect result is guaranteed. Remember that there are four factors to take into consideration in the context of brilliant resource management. They are human resources, equipment, materials, and facilities.
Do not neglect any of them to set your company free from annoying challenges like delays, poor budget planning, low-level profit margins, failed deadlines, too-late deliveries, bad supply chains, and many more.
Resource 1: Human Resources
Let’s start with human resources. Your labor costs and the professionalism of your team depend on this very factor.
The list of vital roles for your successful performance on the market are the following ones in the context of human resources required for construction:
- Estimators – one or several specialists are responsible for estimating, costing, and budget planning tasks. The pre-construction stage is impossible without competent specialists in this direction.
- Architects and designers – these experts are your eyes and creative directors. They should make a specialty out of modern digital tools to provide project plans with quality modeling and visualization properties as fast as possible (3D modeling software, BIM systems, AI-powered design programs, etc.).
- Supervisors – do not neglect these intermediary parties between narrow-direction specialists and managers. Hire several specialists for better interactions between your departments and the hottest insights provided from the field workers to the management pool of your company.
- Engineers – these workers bring all the architects’ and designers’ plans into reality through their high-level competence in the field of building, electrical systems, mechanical utilities, etc. They can supervise your construction workers on the site as well.
- On-site workforce – the average workers on the site who undertake their tasks to build the objects timely and hassle-free without delays and other challenges. These are skillful builders and other narrow-direction specialists on the site.
Do not forget about quantity surveyors for your construction projects. These specialists can consult not only architects but clients as well. This is the top advisor and the leading party in any negotiations with the customer and the company’s management team. Manage your team properly and explain their tasks.
To optimize their work, automate their routine task performance. Implement time management apps, communication applications, and cloud-based software for documentation sharing, commenting, and confirmation. Think of digital-friendliness and automation right here and now to speed up processes and cut labor costs.
Resource 2: Equipment for Construction
Both heavy machinery and tools for building are required for your projects. That is why you should meet with your managers and estimators to decide which equipment you are going to rent and which will be bought from a long-term perspective. Usually, contractors purchase heavy machinery they use for most projects first. Some extraordinary orders with specific equipment can be held through rental policies.
If you are going to attract subcontractors, it will be suitable to discuss with them the opportunity to work on the site while applying their own tools and machinery. Offer compensation if it is more reasonable than standard rentals.
Your equipment resource pool can be enlarged step by step. First, you can buy bulldozers, then – cranes, trenchers, etc. But if your machinery costs are well-managed, you can perform your projects only with the help of rented tools and machinery like other contractors do.
Resource 3: Building Materials
Think of cost-effectiveness and quality of required materials for the building. Do not forget about the eco-friendliness of the supplies you need. Most customers would like green-building projects now. Additionally, try to optimize your supply chains to cut down transportation costs and avoid too-late deliveries.
With reliable suppliers, you will be able to cut materials costs as well. Search for partners with bulk pricing and discounts for standing clients. This way variations on the market of building materials will be far from too risky for your budget.
Resource 4: Facilities
Remember that your on-site workers are the main workforce for the construction phase of any project. When the pre-construction stage with numerous changes, estimating, and budget approvals come to an end, your builders start to realize the scheduled plan on the site. They need convenient conditions with all the required facilities.
While thinking of licenses, permits, and other arrangements, do not forget about on-site comfort for workers. Add all the required facilities (according to today’s CDM regulations for construction companies) to your costs. This way you will need at least living accommodations, lockers, canteens, toilets, sanitary facilities, changing rooms, and drinking water facilities for your on-site workforce.
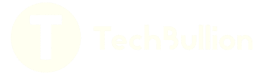