Industrial washing systems are essential in manufacturing and processing industries, where cleanliness and precision in production processes are paramount.
These systems are designed to clean parts, tools, and equipment, removing contaminants that could otherwise compromise product quality, efficiency, and safety.
But how do they do it?
There are different types of industrial washing systems: the important thing is to know how to choose the one best suited to individual needs.
So, now we will dive into different types of industrial washing systems, to discover how they work, the industries that use them, and the benefits they offer.
Different types of industrial washing systems
There are several types of industrial washing systems tailored to meet specific cleaning requirements based on the material, contaminants, and desired level of cleanliness.
Below, we explore the main types.
Water-based washing plants
Water-based washing plants use water, often with detergents or chemicals, to clean various components.
These systems can include high-pressure water jets, ultrasonic cleaning, and immersion cleaning.
They are versatile and suitable for a broad range of industries and contaminants, including oils, dirt, and metal shavings.
Ultrasonic Cleaning Systems utilize high-frequency sound waves to create microscopic bubbles in the cleaning solution. This “cavitation” process helps remove contaminants from complex parts with intricate designs.
Spray Washing Systems instead use high-pressure water jets to clean surfaces quickly and efficiently, commonly used for larger parts or components with simpler geometries.
In Immersion Cleaning Systems, parts are fully submerged in a tank filled with water and cleaning agents. This method ensures that every surface, including interior cavities, is thoroughly cleaned.
Sometimes combined with agitation or ultrasonic waves, immersion cleaning is especially effective for parts with complex shapes, small openings, or hard-to-reach areas.
It’s frequently used for removing oils, dirt, and particulates from machined components or assembled parts in industries like automotive, aerospace, and manufacturing.
Low-boiling solvent washing machines
Low-boiling solvent washing systems use solvents that evaporate quickly at relatively low temperatures.
These systems are particularly effective at removing grease, oils, and other hydrocarbons from metal parts and tools. The solvent, when heated, vaporizes and thoroughly cleans even the smallest areas of parts.
In this process, parts are placed in a chamber with solvent vapors.
When they cool, the vapor condenses on the part, dissolving contaminants and leaving it clean.
This method is highly effective for metal components in the aerospace, automotive, and electronics sectors.
Modified alcohol industrial washing systems
Modified alcohol systems use a closed-circuit process that combines the properties of both water and low-boiling solvents, making them highly adaptable to different cleaning requirements.
Modified alcohols are designed to be non-toxic and environmentally friendly, offering high cleaning power with low environmental impact.
Modified alcohol washing systems operate in a closed-loop system: a sealed environment to prevent solvent release into the air, conserving resources and minimizing environmental impact.
This type of system is excellent for industries that need to meet high cleanliness standards while adhering to environmental regulations.
Which industries use industrial washing systems?
Industrial washing systems are used in a variety of sectors where component cleanliness is critical.
for example…
For cleaning engine parts, transmissions, and various components during manufacturing and assembly.
- Aerospace
Ensures precision cleaning of sensitive components such as turbines, gears, and structural parts.
- Medical and pharmaceutical
Cleans equipment and tools to maintain hygiene standards, reducing contamination risks.
- Electronics
Removes contaminants from circuit boards, semiconductors, and other sensitive electronic parts.
- Food and beverage
For sterilizing and cleaning equipment, conveyors, and tools to meet food safety regulations.
Advantages of Industrial Washing Systems
Industrial washing systems are designed to enhance cleanliness, quality, and efficiency.
They offer specific advantages because they can be customized to clean different materials such as metals, plastics, ceramics, and composites without causing damage.
This flexibility makes them valuable across diverse industries where different materials are used in production.
Some parts, like engine components or circuit boards, have complex geometries with hard-to-reach areas.
Despite that, advanced industrial washing systems like ultrasonic cleaning can target these areas, ensuring complete cleanliness for even the most intricate parts.
Whether the contaminant is oil, grease, dust, or fine particles, different systems are suited to different contaminants.
Low-boiling solvent and vapor degreasing systems, for instance, excel in removing oils and hydrocarbons, while water-based systems are versatile for various contaminants.
Industrial washing systems help ensure that components meet rigorous quality standards, critical in industries like aerospace, automotive, and medical devices. Cleanliness is directly related to product reliability and performance, which in turn affects brand reputation and regulatory compliance.
Modern industrial washing systems are designed to operate in compact spaces and with high automation levels, improving productivity and reducing labor requirements. Closed-loop systems like those used in modified alcohol washers also conserve resources and minimize waste, lowering operational costs and enhancing environmental sustainability.
Industrial washing systems are crucial for maintaining quality, efficiency, and safety in production.
By understanding the types of systems available, the industries that benefit from them, and the unique advantages each system provides, manufacturers can select the right solution to meet their specific cleaning requirements.
This, in turn, helps businesses improve productivity, reduce costs, and ensure compliance with quality standards.
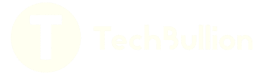