Robot welding is one of the most important and widely used in several manufacturing applications. Welding used to be a labor-intensive process the introduction of welding robots, or automated welding revolutionized the industry.
It is possible to achieve precise and speedy outcomes with robotic technology while reducing waste and increasing safety. Compared to manual welding, a welding robot can reach previously unreachable locations and perform precise and challenging welding lines and welds in a fraction of the time.
7 Common Welding Processes
A welding robot can conform to a broad range of welding processes thanks to the diverse array of machine parts available. Some parts include robotic arms and end of arm tools (EOAT). These processes include:
-
Resistance welding
Resistance welding is one of the most cost-effective forms of robotic welding, making it particularly well suited for large-scale production runs and heat-treatment projects. Furthermore, it contributes to the preservation of stable conditions. There are several types of resistance welding processes, the most common of which are:
- Flash welding
- High-frequency welding
- Percussion welding
- Projection welding
- Resistance seam welding
The process involves joining two overlapping sheets together by applying pressure to them. When an electrical current passes through the sheets, resistive heating occurs, causing the metal to melt and fuse, resulting in a weld. Resistance welding is a fast operation, but each process has its welding time cycle.
-
Arc Welding
Arc welding is one of the most commonly used welding processes in the manufacturing industry. Construction jobs, steel erection, heavy machinery repair, and pipeline welding are some of the most common applications for arc welding in the workplace.
The process involves joining metal pieces together with electricity instead of several other welding techniques that use gas. It makes use of consumable or non-consumable electrodes coated in flux and direct or alternating currents.
The heat temperatures used in arc welding are incredibly high. The excessive heat density poses a danger to the human workers, making a welding robot an appropriate solution for the procedure.
-
Spot Welding
The resistance welding technique of spot welding is yet another procedure that a welding robot carries with precision and consistency. The process involves joining two thin metals with high electrical current resistance. The most common spot welding defects are:
- Asymmetrical spot marks
- Weld material splattering
- Loose material
- Metal cracks or indentations
The agility of a welding robot allows the welding tool to be more precise and consistent, thereby reducing the likelihood of spot welding defects. Welding robots have the unique ability to spot weld in a way that would be nearly impossible with other types of automated equipment.
Their adaptability enables them to reach the workpiece from any configuration, which is necessary to orient the tool to the precise location required for the correct performance of the weld.
-
TIG Welding
In contrast to other welding processes, TIG (tungsten inert gas) welding is highly resistant to errors and produces a high-quality product. Creating an arc between the metal part and a non-consumable tungsten electrode is the goal of the procedure. TIG welding requires a high level of precision, one of the most critical factors when using the process.
For the TIG welding robot setup, a manual welding booth with additional space is required as part of the process. Among the other critical considerations when automating TIG welding are the following:-
- A welding robot with a control system attached to it
- A safety enclosure, complete with safety equipment, to avert any unauthorized access to the automated operation during operation
- Welding torch that includes a power source, a hose assembly, and a feeding wire assembly
- Supply lines for electricity, gas, coolant, or high-pressured air
- Welding fixtures modified for use with an automated positioning system
- An external cooling system
- Curtains that provide protection
- A system for extracting fumes
TIG welding is particularly well suited for joining aluminum, stainless steel, and copper together.
-
MIG Welding
It is necessary to form an electric arc between two metals to be joined and between the metals and the consumable wire electrode for MIG welding. The melting that occurs because of the process joins the metals together.
The welding process is cost-effective, fast, and durable, making it an excellent choice for welds of greater magnitude. MIG welding has some limitations, including the possibility of spattering, which makes using a welding robot ideal for this process.
-
Laser Welding
Laser welding is not a commonly used process, as it is comparatively expensive. The precision of this process, on the other hand, makes it one of the best processes for complex joint geometry procedures. Like other welding processes, laser welding entails fusing two metal plates but with the help of a laser beam.
The process necessitates a substantial working space and the absence of access to parts that do not necessitate welding. Gas lasers, solid-state lasers, and fiber lasers are the three primary types of laser welding currently in use. Welding robots outperform all other forms of automation when providing the high precision and accuracy necessary in laser welding.
-
Plasma Welding
Because of its ambiguity and the need for specialized gear, plasma arc welding is one of the most underexplored welding processes. It is necessary to produce extremely high temperatures during the welding process, accomplished by passing ionized gases through a copper nozzle.
Among the most popular plasma implementations include the assembly of exhaust components and the construction of automobile body panels. Plasma welding is not only sluggish than other welding processes, but it also requires a more significant amount of energy to operate.
Due to its ability to produce ultraviolet and infrared radiation, plasma welding is an excellent candidate for a welding robot. It is particularly well suited for applications requiring high levels of flexibility, as it is simple to adapt to temperature increases and acceleration.
Wrapping up
There are many different robotic welding processes, but the ones listed above are the most common for a broad array of applications across many manufacturing industries. A welding robot provides a healthy and safe work environment, uniformity, quicker welding processes, consistency in production, and superior products regardless of the process.
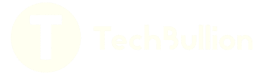