Waterjet cutting is a versatile and precise machining process that has revolutionized various industries. This technology employs a high-pressure stream of water mixed with abrasive particles to cut through materials with remarkable accuracy and minimal heat generation. In this article, we delve into the world of waterjet cutting, exploring its applications, benefits, and the technology behind this remarkable process.
The Technology Behind Waterjet Cutting
At the heart of waterjet cutting lies a powerful pump that pressurizes water to incredibly high levels, typically exceeding 60,000 PSI (pounds per square inch). This pressurized water is then forced through a small nozzle, creating a concentrated and high-velocity stream. To enhance cutting capabilities, abrasive particles, such as garnet or aluminum oxide, are often added to the stream, turning it into a potent cutting tool.
Unparalleled Precision and Versatility
One of the key advantages of waterjet cutting is its precision. It allows for intricate and highly detailed cuts with tolerances as tight as 0.005 inches. This level of accuracy makes it an ideal choice for industries that demand precise shapes and intricate designs, such as aerospace, automotive, and architectural industries.
A Wide Range of Materials
Waterjet cutting can slice through an extensive array of materials, from metals like steel and aluminum to non-metals like glass, ceramics, plastics, and composites. This versatility makes it a valuable tool in various sectors, as it can handle materials of varying hardness and thickness.
Minimal Heat-Affected Zone (HAZ)
Unlike traditional thermal cutting methods like laser and plasma cutting, waterjet cutting generates minimal heat during the process. This characteristic is particularly advantageous for materials that are sensitive to high temperatures, such as plastics and certain alloys. The absence of a significant HAZ prevents material distortion or the alteration of its properties.
Environmental Friendliness
Waterjet cutting is an environmentally friendly machining process. The primary cutting medium is water, and the abrasive used is non-toxic and recyclable. This means that there are no harmful fumes, chemicals, or hazardous waste generated during the cutting process, contributing to a cleaner and safer working environment.
Applications Across Industries
The versatility of waterjet cutting is exemplified by its wide range of applications. In the aerospace industry, it is used to precisely cut intricate components from metals and composites. In the automotive sector, it plays a crucial role in fabricating parts with precision and accuracy. In architecture and interior design, it can create intricate patterns and designs on materials like stone and glass.
Complex Shapes and Intricate Designs
Waterjet cutting excels at creating complex shapes and intricate designs that would be challenging or impossible to achieve with other cutting methods. This capability makes it a valuable tool in the production of custom signage, artistic sculptures, and architectural features that require precise detailing.
Maintenance and Operating Costs
While waterjet cutting offers numerous advantages, it is essential to note that the equipment’s maintenance and operating costs can be relatively high. The pumps and nozzles require regular maintenance to ensure optimal performance. However, these costs are often outweighed by the process’s efficiency and precision.
The Future of Waterjet Cutting
As technology continues to advance, waterjet cutting is poised to become even more efficient and versatile. Innovations in pump technology, abrasive delivery systems, and control software are continuously improving the capabilities of waterjet machines. This ensures that waterjet cutting will remain a valuable tool for industries seeking precision, versatility, and environmentally friendly machining solutions.
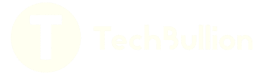