Vacuum is a utility used in a vast array of industrial manufacturing processes including packaging, bottling, drying, degassing, pick and place to name but a few. An industrial vacuum pump is used for creating, improving and maintaining vacuum in these processes. There are many types of industrial vacuum technologies available and this article will explore those technologies. To understand which type of vacuum is most suitable for you and your application, it is crucial to understand the features, benefits and operating principle each type of technology. This article will review the most common types of industrial vacuum pump, how they work and in what types of applications they are best suited.
If you want to discover more about the full range of vacuum technologies we suggest you visit Agilent Vacuum Technology. Agilent Technologies Inc. is a company leader in life sciences and diagnostics, and provides many laboratories worldwide with its own instruments and services. Agilent makes top quality vacuum pumps, systems, and components and has extensive expertise in the field.
Basic Operating Principle of an Industrial Vacuum Pump
The basic operating principle of an industrial vacuum pump remain the same no matter the technology type.
Vacuum pumps remove air molecules (and other gases) from the vacuum chamber (or the outlet side in the case of a higher vacuum pump connected in series). As the pressure in the chamber is reduced, removing additional molecules becomes increasingly harder to remove. Therefore, an industrial vacuum system (Fig. 1) must
be able to operate over a portion of an extraordinarily large pressure range, typically up to 10-9 Torr. To accomplish this, different types of pumps are used in a standard vacuum system, each covering a proportion of the pressure range, and operating in series at times.
Pressure Ranges of Industrial Vacuum System
Industrial Vacuum systems can be placed into the following groups of pressure ranges:
- Rough/Low Vacuum: 1000 to 1 mbar / 760 to 0.75 Torr
- Fine/ Medium Vacuum: 1 to 10-3 mbar / 0.75 to 7.5-3 Torr
- High Vacuum: 10-3 to 10-7 mbar / 7.5-3 to 7.5-7 Torr
- Ultra-High Vacuum: 10-7 to 10-11 mbar / 7.5-7 to 7.5-11 Torr
- Extreme High Vacuum: < 10-11 mbar / < 7.5-11 Torr
Different types of pumps for these vacuum ranges can then be divided into Primary (Backing) Pumps, Booster Pumps and secondary (High Vacuum) Pumps: High, very high and ultra-high vacuum pressure ranges.
There are two basic categories of vacuum pump: Gas Transfer Pumps and entrapment or capture pumps:
Gas Transfer Pumps
Transfer Pumps transfer gas molecules by either momentum exchange (kinetic action) or positive displacement. The same number of gas molecules are discharged from the pump as enter it and the gas is slightly above atmospheric pressure when expelled. The compression ratio is the ratio of the exhaust pressure (outlet) to the lowest pressure obtained (inlet).
Kinetic Transfer Pumps
Kinetic transfer pumps use high speed blades or introduced vapor to direct gas towards the outlet, working on the principle of momentum transfer. These types of pump can achieve high compression ratios at low pressures but typically don’t have sealed volumes.
Positive Displacement
Pumps which work by mechanically trapping a volume of gas and moving it through the pump are known as positive displacement pumps. Often designed in multiple stages on a single drive shaft, the isolated volume is compressed to a smaller volume at a higher pressure, and finally the compressed gas is expelled to either atmosphere or the next pump. To provide a higher vacuum and flow rate two transfer pumps are often used in series.
As mentioned previously, positive displacement vacuum pumps are used to create low vacuums. This type of vacuum pump, expands a cavity and allows the gases to flow out of the sealed environment or chamber. After that, the cavity is sealed and causes it to exhaust it to the atmosphere. The principle behind positive displacement vacuum pump is create a vacuum by expanding the volume of a container. For example in a manual water pump, a mechanism expands a small sealed cavity to create a deep vacuum. Because of the pressure, some fluid from the chamber is pushed into the pump’s small cavity. After that, the pump’s cavity is then sealed from the chamber, opened to the atmosphere and then squeezed back to a minute size. Another example of positive displacement vacuum pumps is like a diaphragm muscle expands the chest cavity, causing the volume of lungs to increase. This expansion results to creating a partial vacuum and reducing the pressure, which is then filled by air pushed in by atmospheric pressure. The examples of positive displacement vacuum pumps are liquid ring vacuum pumps and roots blower which are highly used in various industries to create vacuum in confined space.
Entrapment Pumps
Pumps which capture gas molecules on surfaces within the vacuum system are unsurprisingly known as, Capture or Entrapment Pumps. These pumps operate at lower flow rates than vacuum pumps such as transfer pumps, however, they can provide extremely high vacuum, down to 10-12Torr. Capture pumps operate using cryogenic condensation, ionic reaction, or chemical reaction and have no moving parts, therefore creating oil-free vacuum.
Those Entrapment Pumps that work using chemical reactions, perform more effectively as they are usually placed inside the container where vacuum is required.
Air molecules create a thin film which is removed as the pumps operation cause a chemical reaction to the internal surfaces of the pump. Entrapment pumps are used along with positive displacement vacuum pumps and momentum transfer vacuum pumps to create ultra-high vacuum.
What else?
The vast range of products and techniques shows that high vacuum technology plays a significant part in numerous industrial applications and in the research and medical fields. For example vacuum technology is pivotal for the sterilisation of medical equipment as well as the use of x-ray tubes in high vacuum conditions.
Visit agilent.com website to discover more applications of vacuum technologies.
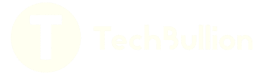