Sheet metal fabrication is a widely – used technology in the manufacturing industry. It involves processing metal sheets into desired shapes and structures through various processes. From automobiles to aerospace, and from medical equipment to electronic devices, sheet metal fabrication plays a crucial role in numerous fields.
This article will provide a detailed introduction to the definition of sheet metal fabrication, its main technologies, material selection, application areas, as well as the sheet metal fabrication design and manufacturing capabilities of CTT Machine.
The Definition of Sheet Metal Fabrication
Sheet metal fabrication is a technology that uses metal sheets to manufacture a variety of products. Through processes such as cutting, forming, and joining, metal sheets are processed into the required shapes and sizes.
Sheet metal fabrication is suitable for a wide range of metal materials, including stainless steel, aluminum, copper, brass, and steel, etc. The thickness of these materials is usually between 0.5 millimeters and 6 millimeters, which ensures both processing flexibility and meets the needs of different application scenarios.
The Three Main Technologies of Sheet Metal Fabrication
The core technologies of sheet metal fabrication can be divided into three major categories: cutting technology, forming technology, and joining technology. Each of these technologies has its own characteristics and plays a unique role according to different materials and application requirements.
1. Sheet Metal Cutting Technology
Sheet metal cutting technology is a key link in sheet metal fabrication. It mainly uses various process methods to cut metal sheets into the required shapes and sizes. These technologies include laser cutting, plasma cutting, water jet cutting, and traditional mechanical cutting (such as shearing and stamping).
1.1 Laser Cutting
Laser cutting uses a high – energy laser beam to irradiate the metal surface, causing it to melt or vaporize rapidly, thus achieving high – precision cutting. This technology is suitable for a variety of metal materials, such as stainless steel, aluminum, and copper. Its advantages include high cutting precision, fast speed, and good edge quality. It is widely used in the aerospace and automotive manufacturing fields.
1.2 Plasma Cutting
Plasma cutting uses high – temperature plasma to melt the metal and then blows away the molten metal with a high – speed gas flow. Plasma cutting is suitable for conductive metal materials, such as steel and aluminum. Its advantages are fast cutting speed and large cutting thickness, making it suitable for cutting medium – and thick – plates.
1.3 Water Jet Cutting
Water jet cutting uses high – pressure water flow or water flow mixed with abrasives to cut metal sheets. Water jet cutting is suitable for various metal and non – metal materials, including soft metals, rubber, and plastics. Its advantages are no heat – affected zone in cutting and smooth edges, making it suitable for cutting complex shapes and precision parts.
1.4 Shearing and Stamping
Shearing and stamping use shearing force and stamping force to cut metal sheets into the required shapes. Shearing is suitable for straight – line cutting, while stamping is suitable for manufacturing holes and complex shapes. The advantages of shearing and stamping are low cost and high efficiency, making them suitable for mass production.
2. Sheet Metal Forming Technology
The significance of sheet metal forming lies in reshaping the material to meet different application requirements. By using various process methods, such as bending, rolling, stamping, etc., metal sheets undergo plastic deformation without destroying their integrity, forming parts or structural components of specific shapes and sizes.
2.1 Bending
By applying external force, metal sheets are deformed at a specific angle to form the required shape. It is usually carried out using a press brake or a roll bender and is suitable for materials such as stainless steel, aluminum, and copper. The advantages of bending are low cost and high efficiency, making it suitable for medium – and low – volume production.
2.2 Rolling
By using one or more pairs of rollers to continuously deform metal sheets, thus achieving thinning of thickness or change of shape. Rolling is divided into cold rolling and hot rolling. Cold rolling is suitable for processing at room temperature, while hot rolling is suitable for processing at high temperature. The advantages of rolling are high production efficiency and good surface quality. It is widely used in the manufacture of tubes and profiles.
2.3 Stamping
Using stamping dies and presses to stamp metal sheets into the required shape. It is suitable for mass production and can manufacture parts of complex shapes. The advantages of stamping are high production efficiency and high precision, making it suitable for applications in the automotive and electronic equipment fields.
2.4 Hemming and Curling
Hemming is the process of curling the edge of a metal sheet to form a double – layer structure, enhancing edge strength and aesthetics. Curling is the process of curling a metal sheet into a cylindrical or other shape, which is suitable for manufacturing containers and pipelines. The advantages of hemming and curling are that they can improve the strength and durability of parts while also improving their appearance.
3. Sheet Metal Joining Technology
Sheet metal joining technology, as the name suggests, is the technology of connecting sheet metal parts with other components. It mainly includes various methods such as welding, riveting, bolted connections, and bonding. Welding connects metals together by melting them at high temperature and has the characteristics of high connection strength and good sealing. Therefore, sheet metal welding is often used for the connection of various structural components.
3.1 Welding
Common welding methods include Metal Inert Gas (MIG) welding, Tungsten Inert Gas (TIG) welding, and Shielded Metal Arc Welding (SMAW). It is a processing method that connects metal sheets together by heating or pressing. The biggest advantage of welding is its high connection strength and good reliability, so it is widely used in the automotive and construction fields.
3.2 Riveting
By drilling holes in metal sheets under external force and inserting rivets, then flattening the tail of the rivet to connect the sheets together. Riveting is suitable for non – ferrous metal materials, such as aluminum and copper. The advantages of riveting are reliable connection and low cost, making it suitable for the manufacture of lightweight structures.
Common Materials in Sheet Metal Fabrication
In sheet metal fabrication, common materials include stainless steel, hot – rolled steel, cold – rolled steel, pre – coated steel, carbon steel, aluminum, copper, and brass, etc.
When selecting materials, factors such as strength, corrosion resistance, processability, and cost need to be considered comprehensively. For example, stainless steel, with its excellent corrosion resistance, is widely used in the chemical and food processing industries; while aluminum, with its light weight and good thermal conductivity, is more suitable for the aerospace and electronic equipment fields.
Industry Applications of Sheet Metal Fabrication
Sheet metal fabrication is the most ideal production and processing method in industrial production and plays a key role in multiple industries.
1. Automotive
Sheet metal fabrication has a wide range of applications in the automotive industry. Through processes such as laser cutting, stamping, and welding, it can manufacture high – strength, lightweight automotive parts. For example, parts such as a vehicle’s fenders, skin, hood, and roof are all products of sheet metal fabrication.
2. Aerospace
The aerospace industry has very high requirements for the precision and strength of parts, and the tolerance requirements are also more stringent. Most aerospace sheet metal products need to be custom designed by result engineers. By using high – pressure and corrosion – resistant stainless steel and aluminum materials, sheet metal fabrication processes can manufacture complex and high precision aerospace parts according to requirements, such as aircraft wings, fuselage, and engine components.
3. Electronic Communications
Electronic communication equipment usually has a compact structure and extremely strict requirements for the size accuracy of sheet metal parts, often needing to be controlled within a very small tolerance range. For example, the size deviation of the outer shell of electronic products such as mobile phones and tablet computers may be required to be within ±0.05 millimeters.
4. New Energy
In the field of new energy batteries, the application of sheet metal fabrication is extensive and crucial. Taking the common new energy vehicle battery box as an example, sheet metal parts are mainly used to connect components such as the battery shell and battery connection pieces.
It is necessary to ensure not only the strength of the steel plate but also its good electrical conductivity. In addition, the cabinet body of commercial and industrial energy storage is also an important application field of sheet metal fabrication. The external cabinet structure of commercial and industrial energy storage cabinets is usually complex and needs to be manufactured through high – precision processing technology to ensure the overall strength and sealing.
Sheet Metal Fabrication Supplier:CTT Technology’s Design and Manufacturing Capabilities
Choosing a high – quality sheet metal manufacturing Supplier is the key to the successful completion of a project. CTT Technology, with over 20 years of technical experience in the sheet metal manufacturing field, has served more than 500+ enterprises globally. We have achieved important cooperation results in multiple industry fields such as new energy, life medical care, and automotive. Combined with our outstanding technical and R & D personnel, your project ideas can be 100% realized through us.
At the same time, CTT Technology has obtained ISO certification. With our service network in Europe, Southeast Asia, the United States, Mexico, and other countries, we can provide you with quick quotation response and logistics transportation.
Conclusion
Sheet metal fabrication is a widely – used technology in the manufacturing industry. Sheet metal fabrication is an important manufacturing technology that is widely used in various fields. By understanding the definition, main technologies, material selection, and application areas of sheet metal fabrication, we can better utilize this technology to improve the quality and performance of products. As a professional sheet metal fabrication enterprise, CTT Technology can provide customers with high-quality design and manufacturing services to help them achieve success.
Read More From Techbullion
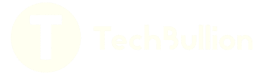