In the vast arena of manufacturing, a Manufacturing Execution System (MES) plays a vital role as an informational nerve center, tracking, controlling, and monitoring the transformation of raw materials into finished products. When implemented appropriately, a MES can significantly boost your team’s performance by supplying the right information at the right moment to the right individuals, thereby optimizing conditions and enhancing production output.
Presently, a majority of successful contractors are leveraging a MES to garner extensive data that was previously inaccessible via conventional methods. This innovation, therefore, presents a plethora of beneficial opportunities for contractors; of which we have highlighted the five most significant ones below.
1. Towards a Paperless Work Environment
A MES makes real-time record-keeping of various costs such as labor, scrap, downtime, and maintenance from the shop floor a possibility. This real-time data enables management to assess unprofitable business models and predict future pricing. With this data being shared across other systems, a MES can help enhance productivity across all your production units.
2. Minimization of Waste, Scrap, and Overages
A MES empowers precise analysis of production lines and finished products, enabling the system to detect inconsistencies on the shop floor promptly and halt them, thus reducing the production of defective parts and wastage of materials.
3. Reduction in Downtime
By tracking raw materials and parts inventory, a MES can generate realistic production schedules, thus cutting down on time wasted in reconfiguring schedules while parts are in transit. This process also facilitates efficient scheduling of employees to maximize utilization of all available workforce.
4. Cost Reduction
Once you have a comprehensive understanding of the product, time, and labor required for a job, it becomes possible to streamline operations. This understanding, facilitated by the MES, can help cut back on orders or free up personnel from managing production lines and controlling inventory.
5. Inventory Reduction
Excess inventory storage is a costly affair. A MES continuously updates your inventory records with fresh production, materials, and product data. This ensures that your purchasing, shipping, and scheduling departments are constantly aware of what is available in each facility and what needs to be ordered.
6. Continuous Improvement:
MES systems promote a culture of continuous improvement. Through data analysis and reporting, manufacturers can identify bottlenecks, inefficiencies, and areas for improvement. This data-driven approach supports the implementation of Lean and Six Sigma principles, resulting in ongoing operational enhancements.
7. Scalability and Flexibility:
Manufacturing environments are dynamic, with evolving processes and changing production volumes. MES systems are highly scalable and adaptable, allowing manufacturers to accommodate growth, integrate new technologies, and respond to market demands effectively.
8. Decision Support:
The wealth of real-time data provided by MES systems empowers decision-makers with actionable insights. By having access to accurate, up-to-date information, managers can make informed decisions quickly, whether it’s adjusting production schedules, reallocating resources, or responding to unexpected issues.
In conclusion, a MES goes beyond merely tracking the volume of product leaving your production lines and shop floor. For Contractors seeking a competitive edge, enhancing your facility’s efficiency starts with accurate recording of data, production, material usage, and personnel time. Implementing a MES solution in your company can accomplish this task with precision and ease.
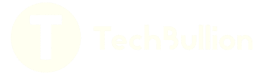