Wire mesh products are integral to numerous industries, embodying versatility and efficiency in various applications ranging from construction and agriculture to pharmaceuticals and automotive sectors. This article delves into the types, manufacturing processes, applications, and future trends of wire mesh products, providing a comprehensive overview of their significance and utility.
Types of Wire Mesh
- Wire mesh is a fabric-like material made from interconnected metal wires. The wires are woven or welded at intersections to create a uniform pattern and structural integrity. The primary types of wire mesh include:
- Woven Wire Mesh: This type is characterized by its method of production where individual wires are woven over and under each other similar to traditional textile weaving. The patterns can vary greatly, including simple square openings to complex decorative designs.
- Welded Wire Mesh: In this type, wires are laid out in a grid and welded at the intersections, offering increased stability and strength. Welded mesh is particularly valued in construction and industrial applications for its load-bearing capabilities.
- Knitted Wire Mesh: Similar to knitted textiles, this mesh is produced by interlocking loops of wire. This type is commonly used in filtration and separation technologies due to its flexible yet dense structure.
Manufacturing Process
- The manufacturing of wire mesh starts with raw wire, which can be made of various metals including steel, stainless steel, copper, and aluminum, depending on the required characteristics like conductivity, rust resistance, and tensile strength. The wire is then either woven or welded into mesh:
- Woven Wire Mesh: Sophisticated looms or weaving machines are employed. The wire is fed into the machine, where it is woven using a shuttle-fed weave or a rapier method to create a tight and consistent pattern.
- Welded Wire Mesh: The wire is placed on a grid pattern and welded at each intersection using electrical resistance welding, which uses heat from an electrical current to join the metal.
- The mesh can be further processed by cutting, shaping, and finishing treatments such as galvanizing or coating to improve corrosion resistance and longevity.
Applications of Wire Mesh
The applications of wire mesh are broad and varied, making it a vital component across many fields:
- Construction and Infrastructure: Wire mesh is extensively used for reinforcement in concrete structures, fencing, and as safety barriers in scaffolding. Its strength and flexibility make it ideal for preventing cracks and structural failure in buildings and roads.
- Industrial Filtration: In the industrial sector, wire mesh is crucial for filtration processes. It is used to filter out impurities in fluids and gases in chemical plants, automotive systems, and wastewater treatment facilities.
- Agriculture: Wire mesh serves several functions in agriculture, including animal enclosures, bird protection nets, and machinery guards.
- Design and Architecture: Architects and designers often use wire mesh for its aesthetic qualities and functionality. It can be found in facades, decorative panels, and artwork installations.
Innovations and Future Trends
The future of wire mesh is driven by advancements in materials and manufacturing techniques. With the rise of automation and robotics, the production of wire mesh is becoming more efficient and cost-effective. Moreover, the development of smart materials, such as shape-memory alloys incorporated into wire mesh, is opening new possibilities for responsive environments that can adapt to changes in temperature or pressure.
Additionally, sustainability trends influence the production and use of wire mesh. Recyclable materials and eco-friendly manufacturing processes are increasingly in demand as industries seek to reduce environmental impact.
Challenges and Considerations
Despite its many advantages, working with wire mesh presents certain challenges. The selection of the appropriate type of mesh (woven, welded, or knitted) and material depends on specific application needs regarding strength, flexibility, and environmental resistance. Moreover, the installation of wire mesh, particularly in large-scale applications, requires skilled labor and precision.
Conclusion
Wire mesh products are a testament to the intersection of traditional manufacturing and modern technological advances. They are indispensable in numerous fields due to their versatility, durability, and cost-effectiveness. As industries continue to evolve, so too will the applications and innovations in wire mesh, suggesting a future where its utility expands even further, supporting new technologies and sustainable practices. The ongoing development and adaptation of wire mesh products will undoubtedly continue to play a critical role across diverse sectors.
Read More From Techbullion And Businesnewswire.com
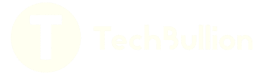