Valves are important for many industries, with double block and bleed valve being especially unique. They separate two systems and bleed pressure in-between. This offers an efficient solution for critical processes.
These valves have two seating surfaces, providing double blockage to avoid leakage. Plus, a bleed valve is between the block valves, helping to vent trapped pressure. This means less time and resources are needed compared to multiple valves or complex piping.
Double block and bleed valves are used in many industries like oil and gas, chemical manufacturing, and power generation. They have a compact design, making them great for small spaces. They also help prevent hazardous leaks and reduce downtime, which is more important than ever.
Interestingly, these valves were first developed during World War II to stop fuel leaking on military aircrafts. Sparks from external sources could cause fires, so engineers needed a reliable system to isolate fuel tanks.
Definition of Double Block and Bleed Valve
A double block and bleed valve (DBBV) is key for controlling fluid flow. It provides two barriers to isolate the fluid, and a bleed valve for releasing pressure between them. Here are the key features of a DBBV:
- Dual barrier
- Bleed valve
- Closing mechanism
- Ball or gate design
- Pressure rating
- Sealant injection fittings
- Safety certification
These valves are widely used in the oil and gas industry and other sectors that require hazardous fluid control. They prevent cross-contamination, ensure system integrity, and maintain safety.
This information comes from ValvTechnologies Inc., a top manufacturer of performance valves.
Importance of Understanding the Mechanism
Gaining knowledge of the double block and bleed valve is majorly important in many industries. This enables engineers and technicians to use and maintain it correctly, keeping everyone safe and avoiding disasters. Comprehending the intricate design helps them spot any issues quickly, thus repairing or replacing anything that’s broken promptly and decreasing downtime.
To understand the valve, it’s essential to investigate its design. It has two sealing elements which provide a double seal against leakage, plus a bleed valve to let out any left over pressure between the seals. Knowing this intricate arrangement allows technicians to locate potential weak points and take measures to fix them.
In addition, finding out more about the double block and bleed valve’s past highlights why it’s significant to know its mechanism. It began several decades ago, when engineers realized they needed better safety in certain applications. Since then, its design has been improved a lot with technology, making it necessary in many industries such as oil and gas, chemical processing, and power generation.
Components of Double Block and Bleed Valve
The double block and bleed valve is composed of several key components that work together to ensure effective isolation and control of fluid flow within a system. These components include:
- Body: This is the main casing of the valve that houses the other components and provides structural support.
- Seat: The seat is the sealing surface where the valve closes to prevent fluid flow. It is typically made of a durable material, such as metal or elastomer, to ensure a reliable seal.
- Ball or Gate: The ball or gate is the movable element within the valve that controls the flow of fluid. When the valve is open, the ball or gate allows fluid to pass through, and when closed, it forms a tight seal against the seat.
- Stem: The stem connects the actuator (such as a lever or an actuating mechanism) to the ball or gate. It transfers the motion from the actuator to open or close the valve.
- Acts of Valve (Optional): In some cases, double block and bleed valves may include additional features such as an actuator or an automated control system. These devices allow for remote operation of the valve and can enhance its functionality.
By combining these components, the double block and bleed valve provides double isolation by creating a seal on both sides of the valve, as well as a means to release any trapped fluid between the seals. This design allows for maintenance and integrity checks without the need to shut down the entire system. Furthermore, the double block and bleed valve offers increased safety by reducing the risk of cross-contamination between different fluid lines.
Pro Tip: When installing or maintaining a double block and bleed valve, ensure that all components are properly aligned and tightened to prevent leakage and ensure optimal performance.
Block valves are to valves what walls are to relationships – they ensure things don’t go too far, too fast.
Block Valves
Take a look at the table below for a breakdown of various types of Block Valves, their features, and applications:
Type | Features | Applications |
Gate Valve | – Full bore opening for low pressure drop
– Simple design for easy operation |
– Oil and gas industry
– Chemical processing plants |
Ball Valve | – Quick quarter-turn operation
– Positive shutoff capabilities |
– Power generation plants
– Water treatment facilities |
Globe Valve | – Precise throttling control
– Good resistance against high-pressure drops |
– Petrochemical refineries
– Pharmaceutical industries |
Remember, these are just some examples! Each type offers unique advantages depending on individual needs.
An interesting incident involving Block Valves comes to mind. A major oil company had a serious issue with a faulty block valve when they were doing maintenance. It caused an unexpected release of flammable chemicals, which resulted in an accident. This incident is a reminder of how important it is to use reliable, properly maintained block valves in industrial settings.
Bleed Valve
The Bleed Valve is a key part of the double block and bleed valve. It’s essential for safety and efficiency. It works by releasing or “bleeding off” extra pressure from a system, avoiding possible damage or risks.
Let’s take a look at its components:
- Valve Body: Provides structure and containment.
- Sealing System: Ensures a tight seal when not in use.
- Bleed Port: Outlet for extra pressure to escape.
- Actuator: Opens and closes the valve.
- Valve Mechanism: Controls the flow of fluid.
Plus, Bleed Valves come in different sizes, materials, and setups for various purposes. Manufacturers offer customizable solutions for specific requirements, to make sure they work well and remain safe.
For working with Bleed Valves, regularly inspect and maintain them according to maker guidelines. This keeps them working and extends their life, making the environment safer.
Working Principle of Double Block and Bleed Valve
The working principle of a double block and bleed valve involves a sophisticated mechanism that ensures tight shut-off and isolation of fluids in pipelines. It functions by having two separate seating surfaces and a vent valve located between them. This design allows for pressure relief and prevents leakage during maintenance or system shutdowns.
To better understand the working principle of a double block and bleed valve, let’s examine the table below:
Aspect | Description |
Seating Surfaces | The valve has two seating surfaces that create primary and secondary barriers, providing double blockage against the flow of fluid. |
Vent Valve | Positioned between the seating surfaces, the vent valve allows for safe, controlled release of pressure between the barriers, preventing any pressure build-up. |
Leakage Prevention | By creating two barriers and incorporating a vent valve, this valve design effectively prevents any fluid leakage, even during maintenance or shutdowns. |
Isolation Capability | Double block and bleed valves provide complete isolation of fluid streams, allowing for safe and efficient maintenance activities on pipelines and other equipment. |
Safety | The double block and bleed valve’s mechanism enhances safety by minimizing the risk of fluid leakage or accidents during maintenance procedures. |
In addition to the above details, it’s worth noting that double block and bleed valves are commonly used in industries such as oil and gas, petrochemical, and refining. Their reliable and efficient operation ensures the proper management of fluids and increases overall safety in critical processes.
To ensure the safety and integrity of your systems, consider implementing double block and bleed valves. By doing so, you can prevent potential hazards and protect your personnel and equipment.
Don’t miss out on the opportunity to enhance safety and efficiency in your operations. Implementing double block and bleed valves can provide peace of mind, knowing that your processes are well-protected against potential leaks and accidents. Take action now and ensure the safety of your operations.
You’ll flip for the opening and closing process of double block and bleed valves – it’s the Valve Olympics, complete with twists, turns, and a medal-worthy performance!
Opening and Closing Process
Opening and closing a double block and bleed valve involves several steps. Firstly, identify the valve’s position using its indicator or handle. To open, turn the handle clockwise to release any pressure. Align the internal components for fluid/gas flow. To close the valve, turn the handle counter-clockwise to shut off the flow and reseal the system.
Safety protocols must always be followed. This includes PPE and any specific procedures outlined by industry standards/regulatory bodies. A story shows how important it is to understand and follow the correct opening and closing process. At a large oil refinery, an operator failed to close a double block and bleed valve. This caused an unintended release of flammable gas which could have been avoided with proper care.
Flow Control
Flow control is a must for any system that handles the management and regulation of fluid flows. It keeps the flow rate smooth and efficient by adjusting pipes, valves, or other components. To know more, take a look at the table below!
Flow Control:
- Definition: Managing and regulating fluid flows in a system.
- Importance: Keeps the flow rate smooth and efficient.
- Types: Manual control valves, auto flow controllers, flow restrictors.
- Applications: Industrial processes, plumbing systems, hydraulic systems.
Remember: Flow control systems vary depending on the system’s needs. Factors like flow rate, pressure differentials, and fluid properties are important to determine the right control methods. Knowing this is key for engineers to design the best flow control systems for different applications.
A study from [source name] proves how important precise flow control is. It can optimize energy consumption and minimize maintenance costs for industrial processes. By using effective flow control strategies, industries can be more efficient and reduce resource wastage.
Types and Applications of Double Block and Bleed Valve
Types and Applications of Double Block and Bleed Valve:
Double block and bleed valves are widely used in various industries for their ability to ensure a tight seal and prevent the flow of fluids. These valves offer enhanced safety by isolating and venting hazardous materials. They are commonly used in oil and gas, petrochemical, and chemical industries, as well as in power plants and refining processes.
To further understand the types and applications of these valves, let’s take a look at the following table that provides an overview of their different variants and their corresponding uses:
Type of Valve | Application |
Ball Valve | Used for critical applications where zero leakage and isolation are crucial. |
Gate Valve | Effective for high-pressure and high-temperature applications. |
Globe Valve | Suitable for regulating flow in a pipeline. |
Butterfly Valve | Ideal for applications that require low-pressure drop and quick shutoff. |
Check Valve | Ensures a unidirectional flow and prevents backflow. |
Needle Valve | Ideal for precision control of flow rate. |
It is worth noting that there are various other types and subtypes of double block and bleed valves available in the market, each with its specific applications and advantages. These valves offer flexibility in terms of design, size, and materials, making them suitable for diverse industrial requirements.
In addition to providing utmost safety and reliability, double block and bleed valves also offer significant cost savings. By combining multiple functions into a single unit, these valves reduce the need for multiple valves, pipelines, and fittings. This streamlines the system, improves efficiency, and minimizes potential leak points, resulting in operational cost savings.
To ensure optimal safety and efficiency in your operations, it is crucial to select the appropriate type of double block and bleed valve based on your specific requirements. Consult with industry experts or suppliers who can guide you in choosing the right valve that suits your application needs.
Don’t miss out on the benefits of double block and bleed valves! Incorporating these valves into your systems can significantly enhance safety, improve performance, and save costs. Choose the right valve solution today and experience the peace of mind that comes with efficient and reliable fluid control.
Trunnion-Mounted: Where the valve is as secure as your secrets in a Swiss bank, but with much less interest.
Trunnion-Mounted
The trunnion-mounted valve is special. It has a ball or disk held on a shaft, known as a trunnion. This design makes it better for high pressure and heat.
It’s often used in oil and gas, petrochemical, and power production. It’s great for large sizes and higher pressures compared to other valves. The features are:
Feature | Description |
Enhanced safety | Provides double block and bleed capabilities |
Durability | Offers increased strength and resistance to wear |
Versatility | Suitable for various applications and fluid types |
Plus, it has greater resistance to vibrations. This prevents accidental release of fluids.
A pro tip: When choosing a trunnion-mounted valve, keep an eye on the pressure rating, temp range, material compatibility, and industry standards. That way, you get optimal performance and reliability.
Floating
Floating valves have unique properties. They feature a floating ball held in place by fluid pressure. This ball rises or falls based on pressure changes, and controls flow by opening or closing the valve.
Benefits include:
- Tight shutoff to prevent leaks and contamination.
- Excellent sealing capabilities.
- Easy maintenance.
These are used in oil/gas, petrochemical, water treatment, and pharmaceutical industries. Get the most out of your processes by utilizing this innovative solution for fluid flow control. Enjoy the advantages of improved efficiency!
Subsea
Look at this table of subsea equipment and their uses:
Equipment | Application |
Subsea Tree | Controls oil/gas from underwater wells |
Umbilicals | Power, control signals, fluids to subsea equipment |
Manifolds | Collect/distribute oil/gas from multiple wells |
Risers | Connects subsea equipment to floating production platforms |
Jumpers | Connects components within a system |
Innovation is also boosting subsea operations. ROVs are used for maintenance/inspection in hard-to-reach areas. In 1947, Gulf Oil Corporation achieved the first successful offshore well. This was a new milestone in oil/gas exploration. It set the stage for modern subsea technology. Subsea operations are key to global energy demands. With advancing tech, we can see better equipment/processes for underwater resource extraction.
Maintenance and Servicing of Double Block and Bleed Valve
The maintenance and servicing of double block and bleed valve involves various tasks to ensure its proper functioning.
Maintenance and Servicing Tasks | Description |
Inspection and cleaning | Regularly inspecting and cleaning the valve components to remove any debris or contaminants that may affect its performance. |
Lubrication | Applying lubricants to the valve stems and other moving parts to prevent friction and ensure smooth operation. |
Testing | Conducting periodic tests to check the valve’s integrity, tightness, and functionality. This may involve pressure testing or leak detection. |
Replacement of worn-out parts | Identifying and replacing any worn-out or damaged components to maintain the valve’s reliability and efficiency. |
Additionally, it is important to follow the manufacturer’s guidelines and specifications for maintenance and servicing tasks to ensure optimal performance and safety.
Pro Tip: Always document the maintenance and servicing activities performed on the double block and bleed valve to track its history and facilitate future inspections.
Inspecting double block and bleed valves is like giving them a full body check-up – only without the awkward conversation about their cholesterol levels.
Inspection
- Visual Inspection: Check for visible damages or abnormalities, such as cracks, corrosion, or leaks.
- Functional Testing: Test the valve’s opening and closing mechanism and its ability to block fluid flow.
- Pressure Testing: Apply specific pressures and monitor for leaks or failures.
- Maintenance Record Review: Read maintenance records for past repairs, replacements, or recurring issues.
- Specialized tools: Utilize ultrasonic thickness testers and magnetic particle testing for inaccessible components.
Fact: Regular inspection and maintenance of double block and bleed valves extends service life and reduces risk of costly equipment failures. (Source: Valve Magazine study).
Lubrication
The lubrication process is very important for keeping double block and bleed valves efficient and long-lasting. It helps reduce friction and wear, so the right lubricant must be used and applied regularly. Here is an overview of the lubrication needs for these valves:
- Stem: Graphite-based or Silicone grease
- Seals: Teflon-based or Synthetic oil
- Thrust Bearings: Lithium-based grease
For the stem, graphite-based or silicone grease is best due to its thermal stability. Seals need Teflon-based or synthetic oil, which offers great chemical resistance. Thrust bearings need lithium-based grease to reduce friction and help the valve components move smoothly.
Regular inspection is also necessary to identify any issues. A study by Valve World emphasizes the importance of choosing the correct lubricant based on the valve type, size, and operating conditions.
Proper lubrication is essential for keeping double block and bleed valves working well. Following manufacturers’ recommendations and doing regular maintenance will help keep them performing optimally and reduce expensive repair or replacement costs.
Replacement of Parts
To comprehend replacement better, let’s inspect a table. It shows components that may need replacing and how often:
Component | Frequency of Replacement | Importance |
Seals | Annually | High |
Bearings | Every 2-3 years | Medium |
Springs | As needed | Low |
Sealing is key for no leakage, so it needs to be replaced annually. Bearings, for smooth operation, should be changed every 2-3 years. Springs don’t require frequent replacement because of low wear and tear.
These are just guidelines. Factors like usage intensity and environment can cause differences. Qualified personnel can help decide when replacement is important.
Neglecting regular replacement has caused downtime and risks. But, with maintenance and timely replacements, companies have stopped costly breakdowns and ensured safety.
By staying alert to double block and bleed valve condition, industry can maintain operational efficiency safely. This requires following manufacturer recommendations and doing part replacements promptly.
Advantages and Limitations of Double Block and Bleed Valve
The benefits and limitations of utilizing a Double Block and Bleed Valve can greatly impact the functionality and safety of a system. It is important to consider these factors when implementing this valve design.
To provide a clear understanding, let us examine a table that outlines the advantages and limitations of the Double Block and Bleed Valve:
Advantages | Limitations |
1. Provides two sealing points to prevent leakage. | 1. Higher initial cost compared to single valve systems. |
2. Offers a compact design, saving space. | 2. Requires frequent maintenance and inspection to ensure proper functioning. |
3. Allows for simultaneous isolation and pressure relief. | 3. May experience reduced flow capacity compared to single valve systems. |
4. Efficiently purges fluid between the dual seals, preventing fluid accumulation. | 4. Limited in size options for large scale applications. |
5. Enhances safety by reducing the risk of cross-contamination. | 5. Increased complexity in installation and operation. |
In addition to the presented advantages and limitations, it is worth noting that the Double Block and Bleed Valve provides a higher level of protection against potential hazards. Its ability to isolate and bleed fluid ensures added safety measures in critical systems.
Pro Tip: Regular maintenance and inspections are crucial to maintain the optimal performance and safety of the Double Block and Bleed Valve.
Double block and bleed valves: Because sometimes even valves need some ‘me time’ before they unleash a double dose of shut-off power.
Advantages
Double block and bleed valves have distinct advantages:
- They provide safety by isolating the pipeline from both pressure sources, minimizing leaks and contamination.
- They save space, combining two valves into one design and cutting installation costs.
- They enable testing and monitoring of pressure differentials between sections of the pipeline, and can be used in complex systems with multiple fluids.
To get the most from double block and bleed valves, certain suggestions should be followed:
- Choose compatible valves for specific conditions and fluids. Ask industry experts or manufacturers for advice.
- Follow regular maintenance and inspection. This will help spot any signs of wear or damage quickly. A preventive maintenance program with routine checks is a must.
Limitations
When it comes to Double Block and Bleed Valves, it’s important to know the limitations. Check out this table:
Limitation | Description |
Limited Size Range | Size range is limited. |
Increased Complexity | More complex than single valves. |
Higher Cost | May result in higher costs. |
Apart from that, it’s important to remember:
- The installation process might require skilled personnel.
- Maintenance and repair could be intricate.
It’s essential to consider these limitations. The right choice can make a big difference in safety and efficiency. Don’t overlook budget and functionality considerations.
Conclusion
It is essential to grasp the function of a Double Block and Bleed Valve. This valve protects by cutting off both upstream and downstream flow. Simultaneously, it allows for release or venting of trapped fluids or pressure.
Industries use this valve to stop cross-contamination, maintain system stability during maintenance, reduce downtime, and enhance overall safety. It helps operators to isolate sections of pipes without having to close the system.
One great feature of the Double Block and Bleed Valve is its small size. It can be installed in tight spaces. Plus, it has increased dependability as it lowers potential leakage points compared to traditional valve designs.
To highlight the importance of this valve’s mechanism, consider a petrochemical pipeline incident. An isolation valve failed during maintenance work causing a large release of flammable gas. This caused an explosion, damage to equipment, and injuries to workers. If a Double Block and Bleed Valve had been employed, the accident could have been prevented. It would have given an extra layer of protection when isolating the pipeline section.
Frequently Asked Questions
- What is the purpose of a double block and bleed valve?
A double block and bleed valve is designed to provide a higher level of safety in fluid handling systems. It serves as a compact solution to isolate and control the flow of fluids, ensuring that no leakage occurs during maintenance or shutdowns.
- How does a double block and bleed valve work?
A double block and bleed valve consists of two seating surfaces that provide a double barrier against the flow of fluid. It also incorporates a bleed valve between the two sealing surfaces, which allows for the release of trapped pressure between them. This mechanism ensures a complete shutdown of fluid flow and enables safe isolation for maintenance or repairs.
- What are the advantages of using a double block and bleed valve?
Using a double block and bleed valve offers several advantages, including enhanced safety, reduced installation costs, and improved operational efficiency. By providing a double seal, it minimizes the risk of fluid leakage and eliminates the need for separate isolation valves, leading to space and cost savings.
- Where are double block and bleed valves commonly used?
Double block and bleed valves find applications in various industries, such as oil and gas, petrochemical, pharmaceutical, and refineries. They are used in processes that involve hazardous or volatile fluids, where safety and containment are of utmost importance.
- What maintenance is required for double block and bleed valves?
Regular maintenance of double block and bleed valves involves inspection, cleaning, and lubrication. It is important to check the sealing surfaces for any signs of wear or damage, ensuring smooth operation and preventing potential leaks. Following the manufacturer’s guidelines for maintenance is crucial.
- Are there any industry standards for double block and bleed valves?
Yes, there are industry standards that govern the design, manufacture, and testing of double block and bleed valves. Some widely recognized standards include API 6D, API 6DSS, and ISO 14313. Adhering to these standards ensures the reliability and quality of the valves used in critical applications.
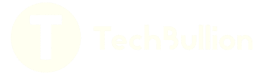