Water bottle manufacturing is a complex process with multiple cost variables. Whether you’re a startup or a seasoned buyer, understanding the breakdown of these costs is essential for making informed decisions. In this article, we will explore the various factors that influence the cost of manufacturing water bottles and provide buyers with a clear understanding of where their money goes.
1. Raw Materials Cost
The choice of material is one of the biggest factors influencing the cost of water bottle manufacturing. The two primary materials used in manufacturing water bottles are plastic and stainless steel, though other materials like glass and aluminum are also popular.
- Plastic (PET, HDPE, LDPE): Plastic bottles, particularly made from PET (Polyethylene Terephthalate), are widely used because of their low cost. The cost of plastic bottles is influenced by the fluctuating prices of crude oil, as it’s a petroleum-derived material.
- Cost: Low
- Pros: Affordable, lightweight
- Cons: Environmental concerns, not as durable as other materials
- Stainless Steel: Stainless steel water bottles are more expensive to produce due to the higher cost of raw materials. Stainless steel is durable, resistant to corrosion, and keeps beverages insulated for longer periods.
- Cost: Medium to high
- Pros: Durable, reusable, environmentally friendly
- Cons: Higher upfront costs
- Glass and Aluminum: These materials fall somewhere between plastic and stainless steel in terms of cost. Glass is often preferred for its purity and inert properties, while aluminum is valued for being lightweight and recyclable.
- Cost: Varies depending on design and quality
- Pros: Both eco-friendly and reusable
- Cons: Glass is breakable; aluminum can be more expensive than plastic
Key Takeaway: Buyers must weigh the benefits of material quality versus cost, keeping their target market and sustainability goals in mind.
2. Design and Customization Costs
Customization is a major driver of cost in water bottle manufacturing. Whether you’re aiming for simple branding or intricate designs, the more complex the design, the higher the cost.
- Mold Creation: Custom molds for bottles, particularly in unique shapes or sizes, can significantly increase upfront costs. Mold charges can range from hundreds to thousands of dollars, depending on complexity.
- Printing and Logo Application: Adding logos or artwork to bottles requires techniques like screen printing, heat transfer printing, or laser engraving. These options vary in cost depending on the number of colors, design complexity, and the production run size.
- Packaging: Custom packaging also adds to the cost. Simple cardboard boxes are less expensive, while branded packaging with inserts, labels, and other features can escalate expenses.
Key Takeaway: Customization options, especially molds and packaging, can add significant costs to production. Buyers need to plan for these expenses early in the product development phase.
3. Labor and Manufacturing Location
The cost of labor varies widely depending on where the manufacturing takes place. Manufacturing in regions with lower labor costs can significantly reduce expenses.
- China: As one of the world’s largest manufacturers, China offers a cost-effective option for producing water bottles due to lower labor costs and well-established production facilities.
- USA & Europe: Manufacturing in the U.S. or Europe usually comes with higher labor costs. However, for some buyers, the benefits of quicker shipping, closer communication, and supporting local economies may justify the higher price.
- Automation: In highly automated factories, labor costs are lower, but the initial investment in machinery can be high. However, these savings in labor can benefit manufacturers in the long term.
Key Takeaway: Buyers need to consider both the cost of labor and the advantages of manufacturing locally or overseas based on their budget and supply chain needs.
4. Production Volume and Economies of Scale
The number of units produced directly impacts the cost per bottle. Manufacturers often offer discounts for larger production runs due to economies of scale.
- Small Batches: Producing water bottles in small quantities typically results in a higher cost per unit. This is because the fixed costs, such as mold creation and setup fees, are spread across fewer units.
- Large Batches: Larger orders spread these fixed costs across more units, reducing the cost per bottle significantly. In many cases, manufacturers will provide tiered pricing, where higher volumes reduce the price per unit.
Key Takeaway: Buyers aiming to reduce their per-unit cost should aim for higher order volumes if their budget allows. Planning for bulk production can save significantly over time.
5. Shipping and Logistics
Shipping can be a significant component of the overall cost, especially for buyers located far from the manufacturing plant. There are two main factors to consider:
- Freight: The cost of shipping large volumes of water bottles depends on the weight, distance, and the shipping method (air vs. sea freight). Sea freight is more cost-effective for bulk orders, while air freight is faster but more expensive.
- Import Duties and Taxes: Importing goods from overseas can involve additional taxes and duties, depending on the buyer’s country of origin and trade agreements.
Key Takeaway: Buyers should factor in shipping and import costs, especially if they are sourcing water bottles from overseas. Negotiating terms such as FOB (Free on Board) or DDP (Delivered Duty Paid) can help clarify shipping costs.
6. Quality Control and Testing
Ensuring the quality of water bottles is a crucial step in the manufacturing process, but it can add to the cost. Many reputable manufacturers include quality control as part of their service, but buyers may opt for additional third-party testing to ensure safety and compliance with regulations, especially for materials that come into contact with food and beverages.
- Quality Assurance (QA): This includes visual inspections, durability tests, leak tests, and ensuring the product meets international standards like FDA or BPA-free certifications.
- Third-Party Testing: Buyers may choose to pay for independent testing for certifications, which ensures product quality and reduces the risk of defects. However, these tests come with additional costs.
Key Takeaway: Ensuring the highest quality standards through testing can increase costs but may save buyers from potential legal issues or customer dissatisfaction down the road.
Conclusion
Understanding the full spectrum of costs in water bottle manufacturing helps buyers make informed decisions. From material selection and customization to labor and shipping, each factor plays a role in the final price. By carefully evaluating these aspects, buyers can optimize their purchasing strategy, reduce unnecessary costs, and ensure the best value for their investment.
Whether you’re sourcing bottles from an overseas manufacturer or producing them locally, gaining insight into these cost components is the key to staying competitive and making sound financial choices in the water bottle manufacturing market.
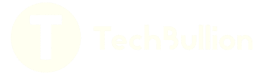