In the area of industrial automation Human-Machine Interface (HMI) systems have turned out to be crucial elements for operators and engineers. HMI systems are defined as the link between the technological procedures of industries and the individuals who supervises them. HMI systems allow the operator to interface with the machinery, view system status and initiate remedial action, all this in near real time thanks to the application of the intuitive interfaces. This article focuses on bringing out the basic understanding of HMI, the constituents of HMI and the significance of HMI in the improvement of industrial automation.
What is HMI?
The Human-Machine Interface (HMI) definition is a graphical interaction between a human and a machine, system or a process. In industries, HMI systems act as a graphical interface to a control system showing information from the real control system comprising of sensors, devices among others. This type of display enables the operator to observe the condition of equipment, control it and address alarms or signals.
HMIs can be installed in functions in various industries, for instance in manufacturing, energy, and transportation and utility industries. They are used in supervising and regulating industrial processes so as to check on the performances of systems.
Key Components of HMI
An HMI system typically consists of several key components that work together to provide a seamless user experience:
Hardware:
From the above description, it will be seen that, the HMI system hardware component comprises of the physical gadgets required to interface the human operator with the system. This may comprise touch screens, computer keyboards, mice or any other touch responsive devices. The material used in the creation of the hardware is such that it enters the industrial environment in a way that it is ready to endure conditions like high temperatures, dust, and vibrations.
Software:
Additional, HMI software is used in developing the graphical user interface through which the operators work. These can run between mere control interfaces to sophisticated applications that give comprehensive information on the state of the system. Advanced HMI software packages contain built-in tools such as data acquisition, data analysis and trend evaluation, and alarm systems which if used properly enable operators to make proper decisions.
Communication Interfaces:
HMI systems are dependent on communication interfaces that enable it interface with the actual control systems such as the PLC’s or the DCS. These interfaces enable the exchange of information between the HMI and the control system in a way that is conducive to messaging and real-time in order to give the operators an efficient way to understand processes and be able to control them.
The Role of HMI in Industrial Automation
These HMI systems are very essential for industrial automation because they offer the operator, by way of tools, means of monitoring, control and optimization of these processes. Here are some of the key benefits of HMI in industrial settings:
Enhanced Operator Efficiency:
HMI systems thereby reduce the complexity of operators’ and machines’ interface so as to be easy to use. In view of this, one can tell at first glance the state of a process, problems that may be arising, and take appropriate measures. This makes the systems highly easy to use and learn especially to new operators while at the same time improving efficiency.
Real-Time Monitoring and Control:
Probably the most important advantage of HMI systems is that they allow for the continuous monitoring and controlling of the process. They can see what is happening in relation to sensors and devices in real time, analyse trends, and address alarms. Such real-time visibility is necessary for achieving and maintaining right conditions, avoiding equipment breakdown, and providing product quality.
Improved Decision-Making:
HMIs offer control room operators the opportunity of getting advanced data and analysis that improves on decision making. For instance, in an HMI system, trends of parameters such as temperature, pressure or anything else in the operation may indicate that this or that part of the equipment may develop a significant problem later on. For further assistance, HMI systems may also be incorporated to give alarm or even advice to the driver.
Increased Safety:
The issue of safety is critically essential in industrial situations, and HMI systems play an enhanced and crucial role in making manufacturing secure. As a result of HMI systems, the operators are easily alerted to extremes of situation so they can counteract them and learn the overall status of the system. However, common functions of the HMI systems consist of the following: Alarm management that is used to ascertain that the critical alarms are highlighted and addressed appropriately.
Customization and Flexibility:
Today’s HMIs are quite versatile and could be used to determine the capability that an industry or application requires in a system. Static interface is available to operators where they can manage the amount of data presented to the extent that only the most critical information is presented. This flexibility makes it possible for HMI systems to meet most of the society and industries’ needs or processes.
The Future of HMI in Industrial Automation
Thus, the HMI systems are being developed today to be even more sophisticated, including more features and functions. For instance, the combine of HMI with the Industrial Internet of Things (IIoT) leads to even more, connectivity and data processing. Also, utilizing AI and machine learning in HMI systems allow decision making and predictive maintenance of the systems to be enhanced.
Hence it is expected that the use of HMI in Industrial automation will experience further increased level of interaction in the future through touchless interfaces, voice commands and augmented reality (AR). These will extend the understanding of and further improve main HMI systems by making their usability, or the handling of the human-machine interface even more efficient.
Conclusion
Human-Machine Interface (HMI) systems are the basic elements of today’s industrial automation to offer the proper interfaces to the operators. The advantages that come with HMI systems such as the provision of real time visibility, improved decision making and safety make it so critical in enhancing reliability in the industrial operations. In future, the part of HMI in automation system of industries will remain high and new avenues will opens up contributing to the growth of industries to fulfil the future requirements.
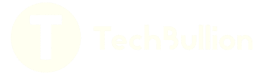