From water supply systems and wastewater treatment plants to chemical processing and medical applications, the right pump can make a significant difference in operational efficiency. Choosing the correct type of pump depends on several factors, including the viscosity of the fluid, required flow rate, pressure demands, and environmental conditions. Understanding the different types of pumps and their specific uses makes sure that you select a system that meets your needs while minimizing maintenance costs and maximizing performance. Some pumps excel at moving large volumes of water, while others are designed for precise dosing, handling corrosive fluids, or operating in submerged environments.
Centrifugal Pumps: The Workhorses of Fluid Movement
They operate by converting rotational energy from a motor into kinetic energy, pushing fluid outward through a spinning impeller. These pumps are ideal for handling large volumes of low-viscosity liquids, making them common in water supply systems, HVAC units, irrigation, and chemical processing. Centrifugal pumps are widely used for moving large volumes of low-viscosity liquids, making them a popular choice when you need to rent a water pump for applications like construction site dewatering, irrigation, or emergency flood control. Because they rely on centrifugal force, their performance depends on maintaining a continuous flow, meaning they work best in applications where there is a steady, non-viscous fluid supply.
Positive Displacement Pumps: Handling High-Viscosity Fluids
These pumps excel at handling viscous fluids, slurries, and even delicate liquids that require gentle handling. They come in various types, including diaphragm, piston, gear, and peristaltic pumps, each designed for specific applications. Diaphragm pumps, for example, are widely used in the chemical and pharmaceutical industries due to their leak-free operation and ability to handle corrosive substances. Gear pumps are good for transferring thick fluids like oils and syrups. Because positive displacement pumps maintain a constant flow regardless of pressure changes, they are ideal for precise dosing and metering applications.
Submersible Pumps: Designed for Underwater Operations
Encased in a sealed housing, they prevent water from entering the motor, making them reliable for deep pumping applications. These pumps are commonly used in wastewater treatment, borehole water extraction, and mining operations where fluid needs to be transported from great depths. Their ability to function directly in the fluid they pump reduces the risk of cavitation, a common issue in surface-mounted pumps. Maintenance can be challenging, as they need to be removed from their submerged position for repairs or servicing. Their high efficiency and ability to handle solids make them a go-to choice for many industries.
Peristaltic Pumps: Precision Fluid Transfer for Sensitive Applications
Peristaltic pumps function by compressing a flexible tube with rotating rollers, pushing fluid forward in a controlled manner. Since the fluid only contacts the inner surface of the tubing, these pumps are ideal for applications requiring sterility, such as medical and laboratory environments. They are commonly used in dialysis machines, food processing, and chemical dosing systems. Because they don’t have seals, valves, or moving parts, they minimize contamination risks and are easy to maintain. The tubing must be replaced periodically due to wear from continuous compression.
Diaphragm Pumps: Versatile and Leak-Free Operation
Diaphragm pumps use a flexible diaphragm that moves back and forth to create suction and discharge, making them highly effective for transferring aggressive, hazardous, or shear-sensitive fluids. Their ability to operate without seals or mechanical components that come into contact with the fluid minimizes leakage risks, making them ideal for handling corrosive chemicals, paints, adhesives, and even food products. These pumps can also run dry without damage, an advantage over many other pump types that require a constant liquid supply. Used extensively in pharmaceuticals, chemical processing, and food manufacturing, diaphragm pumps offer exceptional versatility and durability.
Choosing the Right Pump for Your Needs
Selecting the right pump depends on multiple factors, including the type of fluid, operating conditions, required flow rate, and pressure. For general water movement, centrifugal pumps are highly efficient. If you’re dealing with thick, high-viscosity fluids, positive displacement pumps provide consistent flow. For applications requiring submersion, such as deep well water extraction or wastewater treatment, submersible pumps are the best option. When handling chemicals or pharmaceuticals, diaphragm and peristaltic pumps offer contamination-free fluid transfer. Understanding these differences allows you to choose a pump that increases efficiency, reduces maintenance costs, and secures reliable performance in your specific application.
Pumps are indispensable in modern industries, securing the smooth and efficient movement of fluids in various applications. Whether you need a high-flow centrifugal pump for water distribution, a positive displacement pump for thick, viscous fluids, or a peristaltic pump for sterile medical environments, understanding their functions helps you make the right choice. Each type of pump is designed to meet specific requirements, and selecting the wrong one can lead to inefficiency, higher costs, and potential equipment failure. By carefully thinking about factors like flow rate, pressure, fluid properties, and operating conditions, you can optimize your system for maximum performance.
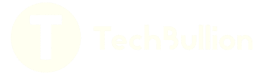