Tube furnaces have become a cornerstone of modern melt furnace technology, revolutionizing the way materials are heated, melted, and processed. These versatile heating systems find applications in various industries, including metalworking, glass manufacturing, ceramics production, and research laboratories. By utilizing a cylindrical heating chamber, tube furnaces offer exceptional temperature control, uniform heating, and precise thermal processing capabilities. In this article, we will delve into the world of tube furnaces, exploring their design, functioning, applications, and the benefits they bring to the realm of melt furnace technology.
Tube Furnaces: Features
Tube furnaces are high-temperature heating systems that consist of a cylindrical heating chamber, often made of refractory materials, enclosed by a protective outer shell. The central heating element, typically made of resistance wires, runs along the length of the chamber. The sample or material to be heated is placed inside a ceramic or quartz tube that is inserted into the heating chamber. This configuration allows for efficient and uniform heat transfer, ensuring precise temperature control during the melting or thermal processing of materials.
Efficient Melt Furnace Technology
Tube furnaces excel in melt furnace applications, offering remarkable efficiency and performance advantages. With their cylindrical design and central heating element, tube furnaces provide even heat distribution, eliminating hotspots and promoting uniform melting throughout the material being processed. This uniformity enables optimal mixing, alloying, and homogenization, resulting in superior quality melt products.
The precise temperature control offered by tube furnaces is crucial in achieving specific melting points for different materials. Whether melting metals, glass, or ceramics, the ability to precisely reach and maintain target temperatures ensures consistent and accurate results. Additionally, the insulation properties of tube furnaces help minimize heat loss and enhance energy efficiency, reducing operating costs and environmental impact.
Diverse Applications
Tube furnaces find a wide range of applications across industries, such as the following:
- In metalworking, these furnaces are used for the melting and casting of various metals, such as aluminum, copper, and steel. They are instrumental in processes like alloy development, metal analysis, and heat treatment applications.
- The glass manufacturing industry also relies on tube furnaces for the production of specialty glasses, optical fibers, and laboratory glassware. The precise temperature control and uniform heating provided by these furnaces contribute to the high-quality standards required in glass production.
- In the field of ceramics, tube furnaces are utilized for sintering, annealing, and glazing applications. These furnaces ensure consistent and controlled heating, enabling the formation of ceramic components with desired properties and characteristics.
Moreover, tube furnaces have significant applications in research laboratories and educational institutions. They are used for material synthesis, chemical reactions, thermal analysis, and various scientific experiments.
Advantages and Innovations
The benefits of tube furnaces and the modifications/innovations are as follows-
- Tube furnaces offer several advantages that make them highly desirable in melt furnace technology. Their cylindrical design allows for easy insertion and removal of samples, simplifying the loading and unloading process. The excellent temperature uniformity provided by tube furnaces ensures consistent results, reducing the likelihood of material defects or inconsistencies.
- Innovations in tube furnace technology have further enhanced their capabilities. Advanced control systems with programmable temperature profiles enable precise and automated thermal processing. Safety features such as over-temperature protection and gas flow control ensure operator safety and process reliability.
- The integration of advanced materials, such as high-purity ceramics and advanced refractories, has improved the durability and thermal efficiency of tube furnaces. These advancements contribute to longer service life, reduced maintenance requirements, and enhanced energy efficiency.
Conclusion
Tube furnaces have transformed melt furnace technology with their exceptional temperature control, uniform heating, and precise thermal processing capabilities. From metalworking to glass manufacturing and ceramics production, these versatile heating systems find diverse applications across industries. With ongoing innovations and advancements, tube furnaces will continue to play a vital role in achieving efficient and high-quality melt processes, empowering industries and research institutions with advanced capabilities for material processing and experimentation.
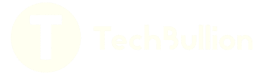