Navigating the complexities of injection molding requires an in-depth understanding of what makes the processes used so special. Factors such as the technology’s adaptability to design complexity, production speed, cost-effectiveness and surface quality need to be taken into account.
To help you navigate this complex field, we’ve summarized three of the most popular and widely used technologies: polycarbonate (PC) injection molding, polymethylmethacrylate (PMMA) injection molding, and acrylonitrile-butadiene-styrene copolymer (ABS) injection molding.
Each offers unique benefits and targets specific applications. In the coming sections, we’ll explore the properties, applications, and performance of these techniques, empowering you to make informed decisions and bring your ideas to life.
What is Polycarbonate (PC) Injection Molding?
Polycarbonate (PC) injection molding is a manufacturing technique that uses polycarbonate, a thermoplastic polymer known for its strength, durability, and transparency. This versatile process can produce various components ranging from automotive parts to protective eyewear, offering significant advantages in industries that prioritize structural integrity and aesthetics.
The parts created through this technique can be crystal clear or colored during the process to accommodate specific design requirements, making them highly favored in industries where visual appeal is as important as functionality. Additionally, PC injection molded parts exhibit high-quality surface finishes, minimizing the need for post-production treatments.
What Makes Polycarbonate (PC) Injection Molding the Go-To Choice for High-Stress Applications?
Polycarbonate (PC) injection molding is a revolutionary technology in the world of manufacturing, highly favored for its application in producing impact-resistant components. It utilizes polycarbonate, a thermoplastic polymer known for its excellent strength, transparency, and heat resistance.
This process provides an unrivaled advantage in industries such as automotive, aerospace, and electronics, where durability and resilience are paramount. PC injection molding can withstand tremendous force without cracking or breaking, making it an excellent choice for producing sturdy eyeglass lenses and durable automotive parts.
Furthermore, this technique also boasts versatility as polycarbonate can be molded into almost any shape while retaining its beneficial properties.
The advantages of PC injection molding
First of all, polycarbonate is a particularly tough and heat-resistant thermoplastic material that can be used to manufacture products capable of withstanding physical pressure and high temperature conditions.
Secondly, the natural transparency of polycarbonate allows for the production of clear parts, while its dyeability provides aesthetic diversity in product design.
In addition, PC injection molding helps create complex-shaped products without compromising the ideal properties of the material.
Lastly, this technology is suitable for mass production and enables high-quality surface finish directly from molds, often reducing the need for additional surface treatment processes.
How to understand the pmma injection molding?
Polymethyl methacrylate (PMMA) injection molding is a popular manufacturing process used to create components from PMMA, also known as acrylic or acrylic glass. This material is a transparent thermoplastic that offers superior optical clarity, making it an excellent alternative to glass in many applications.
PMMA injection molding is extensively used in industries such as automotive, aerospace, and electronics, as well as consumer products like eyewear and home decor. It’s particularly valued for applications requiring high optical clarity, UV resistance, and dimensional stability.
Which fields that apply PMMA injection molding technology?
PMMA (polymethylmethacrylate) injection molding technology is widely used in many industries because of its desirable properties such as high transparency, UV resistance and color diversity.
Due to its high light transmittance and weather resistance, PMMA is used for manufacturing components such as tail lights, signal lights, and dashboards. Its excellent optical clarity also makes it the preferred choice for screens, displays, and light guide panels in various electronic devices.
Meanwhile, PMMA injection molding is used for its aesthetics and durability in a variety of consumer products, such as eyewear, cosmetic packaging, and even household furniture. Utilizing the biocompatibility of PMMA grades provides solutions in medical devices such as surgical instruments, dental prostheses and intraocular lenses.
In addition, PMMA’s high light transmission and UV resistance make it a po
pular choice for indoor and outdoor lighting fixtures, including LED light diffusers, and PMMA’s weatherability and resistance to UV radiation make it suitable for applications such as windows, skylights and acoustic walls.
Why choose PMMA injection molding as the manufacturing process?
From a performance perspective, PMMA has excellent light transmission capability and resistance to ultraviolet radiation, making it an ideal choice for products that need to resist UV rays. This ensures that the product will not turn yellow or degrade over time when exposed to sunlight.
PMMA injection-molded parts can maintain their shape and size even under different temperatures and over time, demonstrating high reliability.
Although not as strong as some other plastics, PMMA provides a good balance between strength and flexibility. It is more impact-resistant than glass, increasing its durability.
In large-scale production, PMMA injection molding offers not only economic benefits but also the convenience of creating complex shapes and intricate details.
The concept of ABS injection molding
ABS injection molding is a popular manufacturing process that uses thermoplastic polymer Acrylonitrile Butadiene Styrene (ABS) to produce various products. It is highly regarded for its ability to create durable components with complex geometries.
The products produced using this process are sturdy and able to withstand daily wear and tear, making ABS the preferred material in various industries. It is commonly used in automotive interior and exterior parts, consumer electronics casings, toys, and other industries.
In which fields is ABS injection molding technology applied?
ABS (Acrylonitrile Butadiene Styrene) injection molding technology has been widely used in various industries due to its excellent durability, impact resistance, and ease of use.
Due to ABS’s strong impact resistance and ability to withstand harsh weather conditions, it is widely used in the manufacturing of automotive interior and exterior parts such as dashboards, bumpers, and wheel covers.
ABS is also commonly used for components such as computer keyboard keys, electronic device casings, and television casings. Products produced through ABS injection molding combine heat resistance with impact resistance, making them the preferred choice for electronic consumer goods. Additionally, many household appliance components such as washing machine drums, vacuum cleaner bodies, and kitchen utensils are made using ABS injection molding.
It is worth mentioning that ABS is a primary material for LEGO bricks. Its safety, strength, and colorability make it an ideal choice for toys.
In the medical field, ABS is used for non-implantable medical instruments such as surgical tools, medical instrument cases,and medical equipment housings due to its strength and sterilizability. In the construction industry,ABS’s durabilityand weather resistance make it an ideal material for items like pipes,fittings,and panels.
Why choose ABS injection molding as the project technology?
ABS (Acrylonitrile Butadiene Styrene) is well-known for its strength, durability, and heat resistance, ensuring the longevity of molded parts.
This thermoplastic material is easy to mold and supports complex precision designs, providing flexibility in product development. With its excellent dyeability, ABS offers a wide range of aesthetic options during the design process.
Furthermore, it provides a high-quality surface finish that often requires no additional post-processing. Additionally, ABS injection molding is an efficient and cost-effective manufacturing process, particularly suitable for large-scale production and significant cost savings.
Conclusion
In summary, the unique advantages of injection molding technology, including strength, aesthetics, and cost-effectiveness, have been widely applied in various industries, shaping the landscape of modern manufacturing. In the future, these technologies will drive further development on a global scale, enabling innovative product designs and improved production efficiency.
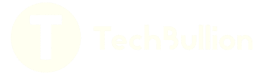