In today’s rapidly evolving world, where sustainability is a paramount concern rather than a mere buzzword, manufacturers are continuously exploring inventive strategies to curtail their environmental impact. Embracing the concept of converting waste into valuable resources has emerged as a powerful approach. Join us as we delve into the realm of energy efficiency and investigate how state-of-the-art technologies are revolutionizing manufacturing processes, ushering in a more ecologically conscious and economically viable future. Prepare to be inspired and captivated by the astonishing advancements taking place in this dynamic domain!
Introduction: Imperative for Energy Efficiency in Manufacturing
As the global landscape progresses, the demand for energy escalates. This escalating demand necessitates more efficient means of energy creation and utilization. One of the pivotal areas demanding focused attention in the pursuit of energy efficiency is manufacturing.
Manufacturing accounts for a substantial proportion of global energy consumption. In fact, according to data from the U.S. Department of Energy, manufacturing utilizes over 30% of the world’s total energy supply. This percentage is projected to amplify as the global population expands and the need for manufactured goods rises.
The reasons to prioritize energy efficiency in manufacturing are manifold. For one, it holds the potential to curtail greenhouse gas emissions. Manufacturing is a significant contributor to global greenhouse gas emissions, making any efforts to mitigate these emissions beneficial for the environment.
Moreover, enhancing energy efficiency in manufacturing processes translates to cost savings for businesses. Given the upward trajectory of energy costs, these savings can be substantial for companies engaged in large-scale production. Simultaneously, bolstering energy efficiency contributes to a safer work environment by diminishing the risk of heat-related exposure and other perils linked to inefficient manufacturing procedures.
In essence, the rationale to enhance energy efficiency in manufacturing is multi-faceted. Such initiatives hold the promise of minimizing greenhouse gas emissions, driving cost savings, and fortifying worker safety—cornerstones of a sustainable future for our planet.
Automation and Data Analysis: Catalysts for Enhanced Energy Efficiency
The industrial sector commands a substantial share of global energy consumption, rendering it a prime focus for efficiency enhancements. In recent times, remarkable strides have been made in this arena through the assimilation of modern technologies and practices, including automation and data analysis.
Automation offers manifold avenues for diminishing energy consumption. For instance, automated machinery can be programmed to operate at reduced speeds during periods of low demand, translating into significant energy savings. Furthermore, automated systems often facilitate more continuous operations compared to manual counterparts, yielding additional efficiency gains.
Data analysis constitutes another pivotal tool for optimizing energy efficiency. By monitoring energy consumption data over time, manufacturing facilities can pinpoint instances of excessive energy usage and take corrective actions. Furthermore, data analysis equips managers with insights to make well-informed decisions on implementing measures to enhance efficiency.
Collectively, automation and data analysis form a formidable arsenal for enhancing energy efficiency in manufacturing settings. Leveraging these tools empowers companies to diminish their environmental footprint while concurrently reaping energy cost benefits.
Sensors: Monitoring the Manufacturing Landscape
Manufacturing processes are growing increasingly intricate and sensitive, underscoring the significance of a comprehensive understanding of production lines for performance optimization and averting costly downtime. In this context, sensors are progressively assuming a pivotal role in manufacturing, offering real-time data for monitoring and enhancing production processes.
A plethora of sensors is available for monitoring various facets of the manufacturing process, spanning energy consumption and machine performance to environmental conditions and product quality. Deploying suitable sensors across the production line empowers manufacturers to glean valuable insights into process efficiency and identify areas ripe for improvement.
Illustrative examples of sensors relevant to monitoring manufacturing processes include:
- Energy Consumption Sensors: These sensors track energy utilization throughout production, facilitating the identification of avenues for improved efficiency.
- Machine Performance Sensors: These sensors capture data on parameters such as speed, temperature, vibration, and pressure, facilitating an assessment of machine performance and early issue detection.
- Environmental Conditions Sensors: These sensors oversee factors such as humidity, temperature, and air quality, guaranteeing a production environment conducive to equipment and material usage.
- Product Quality Sensors: These sensors scrutinize products for defects or anomalies to ensure adherence to quality standards.
Leveraging Connected Technologies for Optimizing Energy Usage
In an era of rapid progress, manufacturers face an ever-mounting need to optimize energy consumption. The advent of cutting-edge connected technologies has significantly eased this endeavor.
Among these technologies is the Internet of Things (IoT), a network interconnecting physical objects linked to the internet, collecting and exchanging data. By tethering devices and machinery to the internet, manufacturers can amass real-time energy consumption data, spotlighting areas ripe for efficiency enhancement.
Another promising technology is artificial intelligence (AI). AI’s prowess lies in analyzing extensive datasets to uncover patterns conducive to energy savings. For instance, AI systems can detect deviations from normal machine parameters and autonomously adjust settings to bolster efficiency.
In harnessing connected technologies like IoT and AI, manufacturers take substantial strides toward optimizing energy efficiency and minimizing waste, catalyzing a transformative impact.
Advantages of Waste Reduction and Efficiency Enhancement in Manufacturing
In the United States, the manufacturing sector garners annual shipments exceeding $2.2 trillion and employs over 12 million individuals. As the cornerstone of the American economy, it is imperative that manufacturers embrace policies and practices fostering energy efficiency and waste reduction.
Fortunately, reaping benefits from waste reduction and efficiency enhancement in manufacturing encompasses a range of advantages, including:
Diminished Production Costs: Waste reduction translates into lower production expenses, augmenting profitability. Simultaneously, efficiency improvement entails reduced energy and raw material consumption, further cutting costs.
Enhanced Competitive Edge: Global competition places American manufacturers in a fierce battleground. Minimized waste and amplified efficiency furnish a much-needed competitive edge.
Reduced Environmental Footprint: Manufacturing exerts a significant ecological toll through pollution and greenhouse gas emissions. Waste reduction serves as a means to alleviate manufacturing’s environmental impact.
Heightened Employee Morale: Efficient, clean workspaces tend to yield more productive and satisfied employees compared to cluttered, inefficient setups.
Elevated Customer Satisfaction: Modern consumers exhibit a heightened inclination toward sustainable products and businesses. Waste reduction enables manufacturers to align with this growing demand for eco-friendly offerings.
Case Studies: Exemplars of Successful Technological Implementation
To elucidate the potential of energy efficiency in manufacturing, we present a selection of case studies highlighting companies that effectively harnessed cutting-edge technologies in their operations.
one2one Corporation: Based in Los Angeles, CA, one2one Corporation specializes in LED lighting products. In 2013, the company undertook a transition to energy-efficient technologies, resulting in a remarkable 25% reduction in overall energy consumption. Additionally, the new production processes yielded a notable 30% decrease in waste output.
Johnson & Johnson: Founded in 1892, Johnson & Johnson stands as a global healthcare behemoth. Its commitment to innovation extends to energy efficiency. By 2009, Johnson & Johnson pledged to slash global greenhouse gas emissions by 20% by 2020, relative to a 2005 baseline. Through the adoption of energy-efficient technologies and production practices, the company successfully realized this goal.
PepsiCo: A prominent corporation, PepsiCo set its sights on energy efficiency as well. The company aimed to achieve a 20% reduction in absolute greenhouse gas emissions by 2030, compared to a 2006 baseline. PepsiCo triumphed by achieving a noteworthy 28% reduction in emissions, driven significantly by investments inefficient technologies and processes.
Conclusion
The transformative power of technological adoption in manufacturing energy efficiency is undeniable. Through strategic investments in advanced technologies, such as predictive maintenance software and intelligent sensors, manufacturers assert control over energy consumption, steering toward sustainability. As research continues in this sphere, the potential for these innovative solutions to benefit businesses and the environment alike is unmistakable.
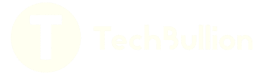