Total Quality Management System (TQMS) is a set of management practices that focus on enhancing customer satisfaction by improving the quality of products and services. It is an integrated system involving all operations, from top-level management to front-line employees. TQMS is based on continuous improvement, where organizations look for ways to improve their current processes and procedures to meet or exceed customer expectations. The key elements of TQMS include process management, employee involvement, quality assurance, training, and feedback loops.
To learn more, visit:https://hgint.com/tqm-total-quality-management-software/ or https://hgint.com/
Benefits of implementing a Total Quality Management System (TQMS):
Improved Customer Satisfaction: TQMS focuses on meeting or exceeding customer requirements, resulting in increased customer satisfaction. By continually improving product or service quality, organizations can enhance customer loyalty and retention, which leads to increased profitability.
Increased Efficiency: TQMS helps organizations identify and eliminate waste and non-value-added activities, resulting in increased efficiency and productivity. By streamlining processes and improving workflow, organizations can reduce costs, improve cycle time, and increase throughput.
Better Quality Control: TQMS involves a structured approach to quality control, including the use of statistical process control (SPC), root cause analysis, and other tools and techniques. These methods help organizations identify and eliminate the root cause of defects, resulting in better quality control and fewer customer complaints.
Continuous Improvement: TQMS is a continuous improvement process, where organizations constantly look for ways to improve their processes and procedures. By implementing a culture of continuous improvement, organizations can remain competitive, increase profitability, and stay ahead of the curve.
Employee Engagement: TQMS encourages employee involvement and empowerment, resulting in increased engagement and motivation. By involving employees in the improvement process, organizations can tap into their knowledge and expertise, leading to better problem-solving and decision-making.
Competitive Advantage: Implementing TQMS can provide organizations with a competitive advantage in the marketplace. By focusing on customer requirements, quality, and efficiency, organizations can differentiate themselves from their competitors, resulting in increased market share and profitability.
Overall, implementing a Total Quality Management System can help organizations improve their operations, reduce costs, enhance customer satisfaction, and increase profitability.
Process management focuses on identifying problem areas in the organization’s production process to eliminate waste and ensure efficient use of resources. This involves analyzing each step in the process flow and determining what can be improved upon. Employee involvement is critical for the successful implementation of TQMS since it provides the necessary support and motivation for teams to follow the system’s guidelines. Quality assurance refers to activities designed to ensure products meet customer requirements. Training is essential as it helps employees understand how TQMS works and how they need to apply it in their daily tasks. Finally, feedback loops are an important part of TQMS as they provide a mechanism for capturing data about how well the system works so that adjustments can be made as needed.
Organizations such as Harrington Group International have reaped great benefits from implementing the Total Quality Management System (TQMS). Through its implementation of this system, Harrington Group International has significantly improved its operations through increased efficiency, lower costs, improved quality control measures, and improved customer service levels. Adopting a TQMS approach has enabled Harrington Group International to continuously identify areas for improvement, resulting in greater profitability and increased customer satisfaction ratings over time.
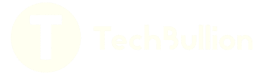