The watch movement, commonly referred to as the “motor,” represents the heart of your timepiece. Unlike automotive engines or electrical motors, watch motors encompass the entire mechanical system driving timekeeping precision. A mechanical movement uses a coiled metal spring, called a mainspring, that releases energy as it uncoils through a series of gears to drive a weighted, oscillating wheel called a balance wheel. This intricate system demands precise calibration and regular maintenance to maintain optimal performance.
Modern automatic watches integrate watch winder motor technology, which requires specialized diagnostic approaches. Understanding these fundamental mechanics enables accurate identification of motor degradation symptoms.
Early Warning Signs of Motor Degradation
1. Timekeeping Accuracy Decline
The most critical indicator involves measuring timekeeping deviation. Healthy mechanical movements maintain accuracy within +/- 10 seconds daily. When your watch consistently gains or loses more than 20 seconds per day, this signals potential motor failure. Document timing variations across multiple days to establish patterns.
2. Power Reserve Reduction
Automatic watches typically maintain 38-42 hours of power reserve when fully wound. If your timepiece stops running within 24 hours of full winding, the mainspring or gear train requires immediate attention. This represents one of the top signs your watch motor needs repair or replacement.
3. Irregular Oscillation Patterns
Professional watchmakers measure balance wheel oscillations at 28,800 beats per hour (4Hz) for standard movements. Irregular beating patterns, audible as inconsistent ticking rhythms, indicate escapement mechanism failure or balance wheel damage requiring motor intervention.
4. Crown and Stem Resistance
Manual winding should feel smooth and consistent. Excessive resistance, grinding sensations, or inability to wind completely suggests gear train contamination or component wear. These symptoms often precede complete motor failure.
5. Date and Complication Malfunctions
Calendar complications provide early warning systems for motor health. Improper date advancement, stuck day-date wheels, or chronograph function failures indicate gear train problems requiring professional diagnosis.
Diagnostic Checklist for Motor Health
Physical Inspection Protocol
Examine the caseback for moisture ingress, which accelerates motor degradation. Check crystal clarity and crown positioning. Visible condensation demands immediate motor assessment to prevent irreversible damage.
Auditory Analysis
Position the watch near your ear and listen for consistent ticking. Irregular rhythms, double-ticking, or silence indicate balance wheel problems. The machine uses ultrasound to agitate the solutions, producing strong forces that break up any contaminants; usually dust and dirt, but sometimes rust or other materials during professional servicing.
Functional Testing
Test all complications systematically. Crown positions should engage smoothly without forcing. Automatic winding should generate consistent rotor movement when shaken gently. Document any anomalies for professional evaluation.
Repair vs. Replacement Decision Framework
Economic Considerations
Service and repair estimates are free and provided within 14 days of receiving your watch. Estimates are provided on a case by case, and vary depending on the specific work and parts needed. Compare repair costs against replacement value, considering the timepiece’s emotional and collectible worth.
Technical Assessment Criteria
Minor timing issues often require simple regulation adjustments. However, mainspring replacement, balance wheel damage, or gear train wear necessitate complete motor overhaul. Professional watchmakers can determine whether repair or replacement provides optimal value.
Age and Availability Factors
Vintage movements may require specialized parts sourcing, affecting repair feasibility. Modern movements benefit from readily available components and standardized service procedures. Consider long-term maintenance accessibility when choosing between repair and replacement.
Preventative Maintenance Strategies
Regular Service Intervals
Your mechanical timepiece could very well outlive you. These are the steps and precautions to take to ensure that does. Professional servicing every 3-5 years prevents major motor failures. This interval allows for lubricant renewal, component inspection, and precision adjustment.
Daily Care Practices
Avoid extreme temperatures, magnetic fields, and impacts that damage delicate motor components. Store automatic watches in best watch winder units to maintain consistent power reserve and reduce wear cycles.
Environmental Protection
Water resistance testing during routine service prevents moisture damage. Avoid crown manipulation underwater and ensure proper sealing after battery replacement in hybrid movements.
Storage Considerations
Position watches crown-up during storage to minimize gear train stress. Avoid extreme humidity and temperature fluctuations that affect metal expansion and lubrication viscosity.
Conclusion
Recognizing the top signs your watch motor needs repair or replacement ensures optimal timepiece performance and longevity. Early intervention prevents costly damage and maintains precision timekeeping. Professional diagnostic services provide accurate assessments for informed repair decisions.
Regular maintenance, combined with careful observation of these warning signs, preserves your timepiece’s mechanical integrity. Investment in proper care yields decades of reliable service from quality watch motors, making professional assessment worthwhile when symptoms emerge.
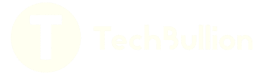