Warehouses rely on HVAC systems to maintain safe, comfortable environments for workers and stored goods. Due to their size and usage, HVAC units often face unique challenges, causing breakdowns and uneven temperatures. Ignoring these issues leads to higher energy costs and disruptions. In this article, we’ll cover the top seven HVAC problems warehouses face year-round and how to fix them.
7 Common HVAC Issues That Affect Warehouse Efficiency
Below are the most common issues warehouses face with their HVAC systems, their causes, and practical solutions to keep your system running efficiently.
1. Uneven Temperature Distribution and Airflow Problems
One of the biggest problems in warehouses is inconsistent temperatures, where some areas become too hot or too cold, affecting comfort.
Signs of Temperature Issues
- Hot and Cold Spots: Certain zones feel noticeably warmer or cooler than others throughout the day.
- Worker Complaints: Staff frequently report discomfort in specific areas during shifts.
- Product Quality Concerns: Temperature-sensitive inventory may spoil due to poor air distribution or humidity.
Fix: Inspect and balance the ductwork to ensure even airflow and temperature. Adjust or install additional dampers and fans for better circulation. Regularly clean air filters to improve system airflow performance.
2. Frequent HVAC System Short Cycling and Power Surges
Short cycling occurs when the HVAC system turns on and off frequently without completing full heating or cooling cycles, increasing wear.
Signs of Short Cycling
- Frequent Starts and Stops: The system powers on and off multiple times in a short period, causing inefficiency.
- Increased Energy Bills: Rapid cycling wastes electricity and drives up energy costs noticeably.
- Wear and Tear: The system experiences more stress, leading to early component failure and repairs.
Fix: Check for thermostat malfunctions or incorrect placement affecting performance. Inspect the system for airflow restrictions like dirty filters or blocked vents. A professional tune-up can recalibrate system controls and improve reliability.
3. Poor Air Quality and Dust Build-Up Issues
Warehouses often accumulate dust, debris, and pollutants that degrade indoor air quality and severely affect HVAC performance.
Signs of Poor Air Quality
- Dusty Surfaces and Equipment: Visible dust accumulation on racks, machinery, and other surfaces.
- Employee Complaints: Reports of allergies, respiratory irritation, or headaches occurring frequently.
- Clogged Air Filters: Frequent filter changes are needed due to high dust buildup within the system.
Fix: Install high-efficiency air filters and replace them regularly to trap contaminants. Consider adding air purifiers or ventilation upgrades for improved air quality. Schedule routine cleaning of ductwork and vents to reduce dust accumulation.
4. Refrigerant Leaks Causing Cooling System Failure
Leaks in the refrigeration cycle reduce cooling capacity and increase energy consumption, risking equipment damage.
Signs of Refrigerant Leaks
- Reduced Cooling Performance: HVAC struggles to maintain set temperatures, affecting warehouse climate.
- Hissing or Bubbling Sounds: Audible leaks near refrigerant lines during HVAC operation or inspection.
- Ice Build-Up: Frost or ice forms on evaporator coils, reducing cooling efficiency considerably.
Fix: Call a licensed technician to detect and repair leaks promptly to prevent further damage. Recharge refrigerant to the recommended levels as specified by the manufacturer. Regular maintenance prevents leaks before they worsen and cause failure.
5. Faulty Thermostats and Control System Failures
Malfunctioning thermostats can cause HVAC systems to run inefficiently or fail to maintain the correct temperature, disrupting the warehouse climate.
Signs of Thermostat Issues
- Inaccurate Temperature Readings: Displayed temps don’t match the actual environment’s temperature accurately.
- Unresponsive Controls: The System doesn’t react to thermostat adjustments or manual inputs properly.
- System Running Constantly or Not at All: Overheating or no heat/cool output causes system inefficiency.
Fix: Test thermostat calibration and replace batteries if needed to restore control function. Upgrade to programmable or smart thermostats for better operational control. Replace faulty thermostats as soon as issues appear to prevent downtime.
6. Inefficient or Failing HVAC Fans and Motor Components
Fans and motors are critical for moving air through the system; when they fail, airflow and system efficiency drop significantly.
Signs of Fan and Motor Problems
- Strange Noises: Grinding, squealing, or rattling sounds during HVAC operation or startup.
- Reduced Airflow: Noticeably weaker air blowing from vents due to failing fans or motors.
- System Overheating: HVAC shuts down due to overheating components or electrical failures.
Fix: Lubricate motor bearings regularly and replace worn belts to improve performance. Clean fan blades and check electrical connections for safety. Replace motors or fans immediately if they show signs of imminent failure.
7. Blocked or Damaged Ductwork and Air Leakage
Duct damage or blockage reduces airflow efficiency, causing poor temperature control and wasted energy across large spaces.
Signs of Duct Issues
- Visible Damage: Tears, holes, or disconnected sections of ductwork are noticeable during inspections.
- Air Leaks: Warm or cool air escaping before reaching target areas reduces system effectiveness.
- Uneven Air Distribution: Certain areas receive less airflow than others due to duct problems or blockages.
Fix: Inspect and seal ducts with mastic or metal tape to prevent leaks. Replace damaged sections promptly to restore airflow. Regularly clean ducts to remove dust buildup and obstructions for better efficiency.
Preventive Tips to Keep Warehouse HVAC Running Smoothly
Maintaining warehouse HVAC systems requires regular attention to prevent breakdowns and inefficiencies. Follow these tips consistently:
- Schedule professional inspections and maintenance twice a year to catch problems early.
- Replace air filters every 1–3 months, depending on dust levels and usage intensity.
- Keep vents and registers unobstructed by pallets, boxes, or stored inventory.
- Monitor temperature zones and adjust airflow balancing regularly for even climate control.
- Train staff to report HVAC issues promptly to prevent larger system failures.
Ignoring HVAC problems in warehouses can lead to uncomfortable working conditions, spoiled inventory, and increased operating costs. Early detection and proactive maintenance help avoid costly repairs and downtime.
Need reliable HVAC parts for your warehouse system? PartsHnC offers quality components, including thermostats, motors, fans, filters, and more to keep your equipment running efficiently.
FAQs
Is it possible to integrate smart building management systems (BMS) with warehouse HVAC?
Yes, modern HVAC systems can be integrated into building management systems for real-time monitoring, predictive maintenance alerts, and energy optimization across multiple zones or facilities.
How long should a commercial HVAC system last in a warehouse environment?
Typically, commercial HVAC systems last 15–20 years, but this can vary based on usage, maintenance, environmental conditions, and equipment quality. Proactive maintenance extends system life and improves performance.
How do I choose the right HVAC system size for my warehouse?
The correct HVAC system size depends on factors such as square footage, ceiling height, insulation, regional climate, and internal heat sources (like machinery). A load calculation performed by an HVAC professional ensures proper sizing, which prevents inefficiency and premature wear.
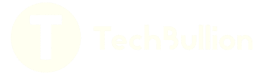