UV-cure adhesives are a type of industrial adhesive that offer rapid bonding capabilities and high strength. These adhesives are often used in industries where speed is essential, such as electronic manufacturing or automotive assembly. The UV light cures the adhesive instantly, allowing for immediate handling and reducing production time. Additionally, UV-cure adhesives have excellent resistance to chemicals and temperature variations, making them suitable for a wide range of applications.
Another important type of industrial adhesive is epoxy resin. Epoxy adhesives are known for their exceptional bonding strength and durability. They can bond various materials together, including metal, plastic, ceramics, wood, and glass. Epoxy resins also provide excellent resistance to moisture and chemicals, making them ideal for use in harsh environments such as underwater applications or chemical processing plants. Furthermore, epoxy adhesives cure at room temperature and can withstand high temperatures once cured. This versatility makes them an invaluable tool across numerous industries.
Hot melt adhesives: Versatile and easy to use
Hot melt adhesives are a popular choice in the manufacturing industry due to their versatility and ease of use. They are thermoplastic materials that can be melted and cooled multiple times without losing their adhesive properties, making them ideal for various applications. One of the main advantages is the speed at which they are set, allowing for faster production times and increased efficiency.
These adhesives can be applied in a number of ways, including via spray guns, rollers, or dispensing equipment. Their quick setting time means that assembly line processes can continue smoothly without waiting for the glue to dry. Additionally, hot melt adhesives provide strong bonds to different types of substrates such as wood, plastic, metal, fabric, and even uneven or porous surfaces.
Another major advantage is that hot melt adhesives do not require any solvents or water during application. This eliminates the need for drying time or curing processes often associated with other types of adhesive. The absence of solvents also means there are no harmful fumes released during bonding, creating a safer working environment for employees.
Epoxy adhesives: Strong and durable bonding solution
When it comes to industrial adhesive solutions, epoxy adhesives reign supreme as a strong and durable bonding solution. What sets epoxy adhesives apart is their ability to create incredibly strong bonds on a wide range of materials. From metal and plastic to wood and ceramics, epoxy adhesives can bond almost any material together with exceptional strength.
One of the unique properties of epoxy adhesives is their high resistance to chemical exposure. This makes them an ideal choice for industries where harsh chemicals are present, such as automotive manufacturing or chemical processing plants. It also means that epoxy adhesives can withstand prolonged exposure to various environmental conditions without deteriorating, ensuring long-lasting durability.
Epoxy adhesives offer excellent versatility in application methods. They can be applied using different techniques such as brush-on, spray-on, or even injected into tight spaces using syringes. This ease of application ensures that regardless of the complexity of the project or the specific requirements, epoxy adhesives can provide a reliable bonding solution.
Acrylic adhesives: Excellent for plastic bonding applications
Acrylic adhesives have emerged as a preferred choice for plastic bonding applications in various industries. These versatile adhesives offer excellent bonding strength and durability, making them ideal for joining different types of plastics together. Unlike other types of adhesives, acrylics can bond plastics that are chemically challenging to adhere to, such as polyolefins and fluoropolymers.
One of the key advantages of acrylic adhesives is their ability to maintain strong bonds even under extreme conditions. They exhibit exceptional resistance to temperature fluctuations, moisture, chemicals, and UV radiation. This makes them perfect for outdoor applications or environments that require adhesive materials to withstand harsh elements. Additionally, acrylics have a high degree of flexibility and can accommodate thermal expansion and contraction without compromising the integrity of the bond.
Another notable feature of acrylic adhesives is their fast curing time. Unlike some other industrial adhesives that require clamping or extended curing periods, acrylics typically cure within minutes. This accelerates manufacturing processes by reducing assembly times and increasing productivity levels. It also allows for greater efficiency when working with delicate or intricate plastic parts where prolonged exposure to heat or pressure may cause damage.
Cyanoacrylate adhesives: Fast curing and strong bonding capabilities
Cyanoacrylate adhesives, also known as instant adhesives or super glues, are renowned for their fast curing and strong bonding capabilities. These adhesives can bond a wide variety of materials, including plastics, metals, rubber, and ceramics. Unlike traditional adhesives that require hours to set and cure, cyanoacrylate adhesives can achieve full bonding strength within seconds.
One of the key advantages of cyanoacrylate adhesives is their ability to quickly bond dissimilar materials. This makes them particularly useful in industries where different materials need to be joined together. Additionally, these adhesives offer excellent resistance against impact and temperature variations, ensuring a durable bond even in demanding environments.
Another noteworthy feature of cyanoacrylate adhesives is their versatility in various applications. They are commonly used in electronics assembly, where they can securely bond delicate components without the need for additional mechanical fixtures. Furthermore, these highly adhesive substances find widespread use in automotive manufacturing for bonding trim pieces and securing gaskets.
Polyurethane adhesives: Ideal for diverse substrates and surfaces
Polyurethane adhesives have gained immense popularity in various industries due to their exceptional versatility and ability to adhere to diverse substrates and surfaces. Unlike traditional adhesives that are only effective on specific materials, polyurethane adhesives can bond a wide range of materials such as wood, metal, ceramics, plastics, and even glass. This makes them ideal for multi-material applications where different components need to be securely bonded together.
One of the key benefits of polyurethane adhesives is their excellent strength and durability. They form extremely strong bonds that resist heat, water, chemicals, and various other environmental factors. Whether it’s joining metal parts in automotive manufacturing or bonding plastic components in electronics assembly, polyurethane adhesives provide a long-lasting solution that ensures structural integrity.
These adhesives offer a unique advantage when it comes to flexibility. They have the ability to absorb vibrations and expand/contract with temperature changes without losing their adhesive properties. This makes them particularly suitable for applications that involve dynamic stress or movements.
Overall, the remarkable ability of polyurethane adhesives to adhere to diverse substrates combined with their strength and flexibility make them an excellent choice across a wide range of industries including automotive manufacturing, construction, electronics assembly and more.
Silicone adhesives: Heat resistant and flexible adhesive option
Silicone adhesives are a popular choice in many industries for their impressive heat resistance and flexibility. Unlike other types of adhesives, silicone adhesive can withstand extreme temperatures, making it ideal for applications where heat is a concern. From automotive to electronics, these adhesives are used to bond components that are exposed to high heat, such as engine parts in cars or heating elements in appliances.
One of the major advantages of silicone adhesives is their flexibility. They have the ability to adhere well on various surfaces, including plastics, metals, ceramics, and even glass. This makes them versatile and suitable for a wide range of applications. Additionally, silicone adhesive remains flexible even after curing, allowing for expansion and contraction without losing its bond strength.
Another notable feature of silicone adhesives is their excellent electrical insulation properties. This makes them an indispensable component in electronics manufacturing where precision bonding is required while ensuring effective thermal conductivity. Silicone adhesives also offer high resistance to weathering and chemicals, further enhancing their durability and reliability.
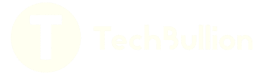