One of the most important elements affecting the price of die casting parts is the material selection.
Cost control is essential to production to maintain profitability and competitiveness in the market. Although die casting is a common production technique for producing high-quality metal parts, the associated prices can differ significantly based on several variables. Your bottom line might be greatly impacted by comprehending these factors and putting control measures in place. In this post, we will look at the top five factors influencing die casting part cost and how to control them.
1. Selection of Materials
One of the most important elements affecting the price of die casting parts is the material selection. Magnesium, zinc, and aluminum are common materials; each has special qualities and costs.
- Aluminum: Generally more costly than zinc, aluminum is lightweight, corrosion-resistant, and appropriate for high-strength applications.
- Zinc: Zinc is heavier than aluminum but is more affordable and simpler to cast, making it perfect for intricate designs.
- Magnesium: Strong and lightweight, but more expensive as a basic material.
Ways to Reduce Expenses
Effective cost control is essential to sustaining profitability, particularly in markets with intense competition. Here are a few doable tactics to save expenses without sacrificing effectiveness or quality.
- Optimize Material Use: Choose the most economical material that satisfies performance standards by consulting with engineers.
- Bulk Purchasing: To lower prices per unit, bargain with suppliers for bulk discounts.
- Recyclability: To reduce waste and material costs, use scrap and recycled materials whenever you can.
2. Tooling Costs
The design and production of the molds (dies) are included in the die casting tooling expenses. Although these expenses are usually substantial, they can be spread out over a lot of production.
Elements Affecting Tooling Prices:
- The mold’s intricate pattern.
- Durability and mold material type.
- Tolerance and precision are necessary.
Ways to Reduce Expenses
- Invest in Durable Dies: Although high-quality molds may cost more upfront, their longer lifespan lowers long-term costs.
- Simplify Designs: Assist designers in getting rid of extraneous details from the part design.
- Shared Tooling: To spread expenses over several projects, take into account shared tooling options for smaller production runs.
3. Production Volume
The cost per unit is strongly influenced by the volume of parts produced. Because die casting allows tooling expenses to be spread across numerous pieces, it is most cost-effective for large production runs.
Ways to Reduce Expenses
- Plan for Scale: To save costs per part, try to increase production volumes.
- Estimated Demand Correctly: Steer clear of overproduction, which can result in waste and needless storage expenses.
- Batch Optimization: To reduce downtime and increase efficiency, arrange manufacturing in batches.
4. Part Complexity
The die casting part’s complexity, which includes finely detailed designs, precise tolerances, and extra features, might raise the cost and duration of manufacture.
- Complex Designs: Demand more time for fabrication and sophisticated tools.
- Tight Tolerances: Raise the bar for inspection and machining.
- Secondary Operations: The total cost is increased by procedures like coating, polishing, and machining.
Ways to Reduce Expenses
- Design for Manufacturability (DFM): Work with engineers to create components that are less complicated and costly to manufacture.
- Employ Standard Features: Steer clear of custom components unless they are required.
- Automate Secondary Activities: Use automated procedures to cut labor expenses for inspection and finishing.
5. Labor and Overhead Costs
The cost of die casting parts is largely determined by labor and overhead costs, which include salaries, facility upkeep, and energy use.
- Skilled Labor: Although they can be costly, highly skilled workers are necessary.
- Energy Costs: Die casting requires high temperatures, which use a lot of energy.
- Facility Overheads: The total cost is increased by maintenance, utilities, and other running costs.
Ways to Reduce Expenses
- Invest in Automation: Automated equipment can increase manufacturing efficiency and lower labor expenses.
- Energy Efficiency: Use energy-efficient furnaces and optimize manufacturing schedules, among other energy-saving techniques.
- Location Optimization: If quality criteria are upheld, take into account producing in areas with less labor and operating expenses.
Extra Tips for Controlling Die Casting Part Costs
Partner with Skilled Suppliers: To take advantage of their knowledge and economies of scale, pick suppliers who have a track record of producing die casting at a reasonable cost.
- Put Quality Control Measures in Place: Defects are detected early, which lowers waste and rework and keeps prices down.
- Frequent Equipment Maintenance: Well-maintained machinery minimizes production inefficiencies and downtime.
- Negotiate Long-Term Contracts: By entering into long-term agreements with suppliers, you can obtain advantageous terms.
- Leverage Technology: To reduce expensive errors, test designs and procedures using simulation software before production.
Conclusion
Optimizing your production budget requires an understanding of and control over the factors that affect die casting part cost. Businesses can use efficient cost-management techniques without sacrificing quality by concentrating on labor and administrative costs, production volume, part complexity, material selection, and tooling costs. With careful planning, teamwork, and the application of contemporary technologies, cost-effective die casting is possible, guaranteeing that your products maintain their competitiveness in the market.
These considerations will assist you in striking the ideal balance between cost, quality, and efficiency, regardless of whether you’re new to die casting or want to improve your current procedures.
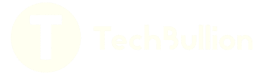