The humble tumbler, a ubiquitous companion for our morning coffee or afternoon iced tea, often goes unnoticed. Yet, behind this seemingly simple vessel lies a complex world of design, engineering, and meticulous manufacturing. In this article, we delve into the fascinating realm of tumbler manufacturers, exploring the intricate processes that bring these everyday essentials to life.
From Concept to Creation: The Design Journey
A tumbler’s journey begins with a spark of creativity. Designers brainstorm ideas, considering factors like functionality, aesthetics, target audience, and market trends.
Sketches flow, exploring different shapes, sizes, and lid mechanisms. Perhaps it’s a sleek, double-walled tumbler for coffee enthusiasts or a vibrant, character-printed design for children. 3D modeling software then takes center stage, creating digital prototypes that allow for precise adjustments and visualization.
Material Matters: The Science of Tumblers
The choice of material significantly impacts a tumbler’s performance and durability. Stainless steel is a popular option, lauded for its heat and cold retention properties. However, stainless steel tumbler manufacturers might utilize double-wall vacuum insulation to further enhance these capabilities. Plastic tumblers offer a lightweight and affordable alternative, often featuring BPA-free materials for safety. Some manufacturers might explore eco-friendly options like bamboo or recycled materials, catering to environmentally conscious consumers.
The Art of Molding: Shaping the Tumbler
Once the design and material are finalized, the manufacturing process kicks in. Depending on the chosen material, different methods come into play. For stainless steel tumblers, manufacturers often utilize metal injection molding (MIM). This intricate process involves injecting molten metal into a mold cavity, creating precise and durable shapes. Plastic tumblers, on the other hand, might be produced through injection molding, where molten plastic is forced into pre-designed molds. The choice of mold material (steel, aluminum) and the molding technique (injection, compression) influence factors like production speed and cost.
The Heat is On: The Power of Forming
After molding, some tumblers might undergo additional forming processes. Stainless
steel tumblers might be spun or drawn to achieve their final shape. Spinning involves rotating a metal disc and shaping it into a desired form. Drawing, on the other hand, pulls the metal through a series of dies to achieve the final dimensions. These processes ensure consistent shapes and a smooth finish for the tumblers.
Joining Forces: Assembly and Finishing Touches
For tumblers with lids or additional components, assembly becomes a crucial step. This might involve ultrasonic welding, which uses high-frequency sound waves to create a strong bond between plastic parts. Alternatively, mechanical fastening like screws or rivets might be employed. Finally, the finishing touches take place. This could involve polishing stainless steel for a gleaming finish or decorating plastic tumblers with vibrant prints or logos using techniques like pad printing or screen printing.
Quality Control: Ensuring Flawless Functionality
Throughout the manufacturing process, rigorous quality control measures are implemented. These might involve inspecting raw materials for defects, checking dimensional accuracy of molded parts, and ensuring leakproof seals on lids. Manufacturers often employ sophisticated testing equipment to evaluate thermal retention capabilities and durability under simulated use conditions.
Innovation and Sustainability: The Future of Tumblers
The world of tumbler manufacturing is constantly evolving. Manufacturers are exploring innovative materials like bioplastics to create more sustainable products. Additionally, advancements in printing technologies offer a wider range of customization options for consumers. Smart tumblers with integrated temperature sensors or connected features might become more prominent in the future.
The Final Sip: A Celebration of Craftsmanship
The next time you reach for your favorite tumbler, take a moment to appreciate the craftsmanship that went into its creation. From the initial design concept to the rigorous manufacturing process, a team of dedicated professionals ensures you have a reliable and stylish companion for your beverages. Tumbler manufacturers, the quiet heroes behind our everyday essentials, deserve a well-deserved toast.
Exploring Further
This article provides a broad overview of tumbler manufacturing. To delve deeper, consider exploring the following:
Specific manufacturing techniques: Research specific processes like metal injection molding (MIM) or vacuum insulation technology for a more technical understanding.
Sustainability initiatives: Look into manufacturers committed to eco-friendly practices, such as using recycled materials or reducing their carbon footprint.
Emerging trends: Explore the latest trends in tumbler design and technology, like smart features or self-cleaning mechanisms.
By venturing further, you’ll gain a deeper appreciation for the ingenuity and dedication that goes into creating the perfect tumbler for every need.
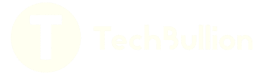