What is a twin screw extruder and How Does it Work?
In numerous firms where materials have to be processed, twin screw extruders serve as strong machines with great flexibility. The twin screw extruder consists of two screws that mesh together and revolve in the barrel smoothly, creating optimal conditions for material processing. This section will cover the fundamentals of twin screw extrusion, its benefits, and the major elements used.
For more in-depth information, you should view Twin Screw Extruder – UDTECH.
Advantages of Twin Screw Technology
There are numerous reasons why twin screw extruders are greatly liked in comparison to other techniques; some of them include:
- Enhanced Mixing: The intermeshing screws of the twin extruder create an excellent solution that leads to better blending and superior product outcomes.
- Superior squirter performance: Highly viscous/shear-sensitive materials can be processed without taking any performance hits and other quality indicators where TSEs primarily excel.
- Elevated efficiency: Higher volumes of production leads to greater throughput and efficiency; when placed side to side with single screw extruders, twin screw extruders stand higher.
View Twin Screw Extruder – UDTECH for More Details
Key Components of a Twin-Screw Extruder
A strong tri-slap brot, the self Avery, and finally, a tanger; by gaining an intersected understanding, one can really get a grip on what a twin screw extrusion is.
- Barrel: Keeping the temperature restraints in place during the extrusion process tends to heat or cool down the barrel, which also accommodates a controlled ambiance for the housing of screws.
- Screws: The intermeshing screws come in various forms, co-rotating and counter-rotating being the most common. They play a crucial role in mixing and melting which makes them the centerpiece of the extruder.
- Feed section: When using features like side feeders or vacuum vents to ensure greater miscibility of raw materials with the extruder, the Feed section allows the raw materials to get an extra grip on the device.
- Screw Elements: The Conveying, mixing, shearing, and melting functions are not performed by the screws alone, there are certain elements that more invoices these processes, and these elements can be adjusted to suit the different processes.
- Die: The die merges alongside the other components to forge shapes out of raw material, it accommodates different shapes and sizes of a product. To put it simply the Die sets the product dimensions.
After comprehending the general summary of the twin screw extrusion, one can transition into gaining a deep understanding of the industries it is applicable in and how one can enhance its performance.
Exploring the types of twin screw extruders
Twin screw extruders can be classified into two main types: co-rotating and counter-rotating. Each type offers unique advantages and is suitable for specific applications in the plastic processing industry.
Co-rotating Twin Screw Extruders
Twin screw extruders that rotate together possess screws that revolve in the same direction. This setup facilitates smooth advancement, melting, and homogenization of the material. Co-rotating extruders are adaptable in nature and find application in the following:
- Compounding and blending of a group of polymer materials
- Steerable heat polymers’ chemical synthesis and modification by reactive extrusion.
- Making and combining polymer masterbatches and additives
- Plastics recycling and reprocessing
Counter-rotating Twin Screw Extruders
Counter-rotating twin screw extruder consists of two screws which rotate in opposite directions. This type of rotation will result in a greater degree of shear and mixing, thus making the use of counter-rotating extruders ideal for applications with high shear and compounding requirements. The main applications of the counter-rotating extruders are:
- Composition of high filler compounds
- Severe mixing of pigments and additives
- Extrusion of reactive compounds with greater control over shear and residence time
Reconciling the main distinctions between the co-rotating and counter-rotating twin screw extruders permits the manufacturers to make the right decision on the type of extruder which would be suitable for them. Thus, by utilizing the potential of these different types of extruders, production processes in industries are enhanced, leading to improved product quality.
What twin screw extruders offer in Plastic Processing?
TSEs (twin screw extruders) have the most impressive mixing and disbursement qualities and enable new domains in the manufacturing of plastic. The use of co-rotating or counter-rotating screws ensures that the extruders possess enhanced ability of mixing and subsequently dispersing additives, fillers, and pigments. This mixing capability leads to substantial advantages:
- Homogeneous Product Quality: one of the major features of twin screw extruders is their intense mixing and as a result homogenous uniformity and even distribution of fillers and additives is achieved, this leads to the final product possessing consistent quality and high-performance capabilities.
- Optimized Product Properties: Achieving better dispersion in TSE enables the manufacturers to optimally adjust the features plastic compounds and fine-tune properties such as mechanical strength, thermal stability and color consistency.
- Reduced Processing Variability: Consistent mixing and disbursement results into reduction in variability in manufacturing processes which in turn minimizes the percentage of defects, waste produced and the requirement for rework.
- Increased Production Efficiency: Due to the high loadings that extrusion machines provide, melt quality is enhanced along with production rates and efficiency while reducing energy consumption.
Manufacturers also need to consider screw design, residence time control, temperature control, and other control systems to fully benefit from these advantages. If Plastic manufacturers correctly manage these factors, they can use TSEs to their fullest potential and reduce operational costs while enhancing product quality and consistency.
Advantages of twin screw Extruders Over Single Screw
When it comes to plastic production, twin screw extruders tend to offer more benefits than single screw types. Bearing in mind those benefits which are intrinsically connected with some of the peculiarities of twin screw extruders technology is likely to facilitate companies in making appropriate decisions for their operations. The following are the main benefits & features which should be taken into account:
- More Efficient Mixing: Twin screw extruders are very good at the mixing and dispersion of materials thoroughly, which means that differences in what is being manufactured is also reduced. This reduces the defects that may occur the waste and the need for extra work and increases the quality and consistency of the product.
- Enhanced Energy Efficiency: Because of the effective mixing function of twin screw extruders, melters are capable of achieving higher production speed with much lower energy which allows manufacturers to lower production costs.
Main characteristics of twin screw extruders that allow to benefit from more modern types of extruders include that:
- Special Features of the Screws: Generally, twin screw extruders have intermeshing or co-rotating type screws with certain geometries, which are prepared specially to aid in the mixing and melting process. It is very important to choose the right type of screw to ensure adequate performance and output.
- Temperature Control and Residence Time: Effective temperature management is of paramount importance, along with having appropriate mechanisms to combine control. Additionally, residence time must be not only controlled but even optimized, in order to deliver the best end results. Precise temperature profiles, for example, exposed along the extruder barrel, are crucial in defining the material properties.
- High Shear Considerations: The twin screw extruders developed (or rather modified) by growth in research today match the high shear forces coupled with better material dispersion, melt homogeneity and increased mixing efficiency. Other factors, such as the intended plasticization or process requirements, have to also be given considerable thought before determining the desired shear rate and intensity for such applications.
The designed performance of the twin screw extruders would remain wanting unless put into context with implementing an effective control system. This encompasses thorough monitoring, process control and even automation in order to ensure reliability and consistency of the operation.
Understanding the features of the twin screw extruders and leveraging the advantages that come with them can considerably increase the quality of the products that the manufacturers provide and even enhance the operational efficiency and speed of the plastic manufacturing processes.
How to Optimize twin screw Extruder Performance
Importance of Temperature Control and Residence Time
The performance of twin screw extruders is enhanced with temperature control which is critical in this case. Material properties melt quality, and overall efficiency of processing are directly achieved with temperature regulation. When temperature control is undertaken with caution, manufacturers are able to obtain results that are accurate and consistent, maintaining the right characteristics of a certain material while also preventing mixing or degradation issues. Likewise, applying shear and heat for a certain time frame will also enable compliance at the prerequisites. It enables the effective transfer of heat, even melting, and material distribution.
Screw Geometry and High Shear Considerations
Twin-screw extruders have outstanding geometries and configurations of screws that extrude feed within the twin-screw to suit the form of homogeneous material within the cavity. There is a screw design which enhances the flow of the material that is being mixed and determines the performance of the extrusion machine. Application such as the desired properties of a material and other conditions, therefore the manufacturers should apply due diligence when deciding on the geometry of a screw. Furthermore, strong shear forces can be applied by twin screw extruders improving the dispersion of materials, uniformity of melt and mixing efficiency. It would also be prudent to evaluate the specific demands of the process and decide on the correct shear rate and intensity.
Advanced Performance Monitoring Systems
Must have design elements for twin screw extruders is determining dual screw parameters that offer control features that are easy to implement. This also includes the increased degree of automation in conjunction with broad-scale monitoring of numerous non-linear systems. The use of more advanced control systems makes it possible to set dosing control, heater power limiting, and speeds for the screw rotation and other technological devices. The types of real-time monitoring systems and feedback even more so enable easier correction as well as fine-tuning the process to the best possible conditions along with the required product quality. Another important aspect of a control system is the total control over data allowing reworking and further improving the process.
Employing the benefits of temperature control, screw geometry improvement, high shear assessment, and maintaining an adequate control system, manufacturers can enhance the processes of plastic manufacturing. In this way, the quality of the products improves, operational efficiency improves, and the increased requirements of modern plastic extrusion applications are satisfactorily fulfilled.
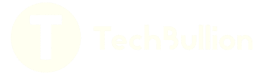