Concrete is a primary component of modern construction. In fact, it is second only to water as the most consumed item on the globe, with 30 billion tons processed annually worldwide. From humble home driveways to giant commercial structures, concrete exists in all of its forms.
Even though it’s common, estimating concrete accurately can be tricky. If you order too little, the project may stop midway. Order too much, and you waste money and materials. Studies show that about 9% of construction cost overruns come from poor material estimates, with concrete being a major one.
This guide will take you through the various steps involved in proper concrete estimating, from basic principles and formulas to suggested tools, tips, tricks, and common mistakes. Whether you are a contractor, builder, or just a homeowner working on a project, this guide will help you better prepare and reduce the risk of surprises.
What Is Concrete Estimating?
Concrete estimating is the process of calculating the required concrete materials and the total cost of a given project’s financial outlay. The estimate covers more than the concrete; it includes the costs of labor, reinforcing steel, construction of formwork, equipment used, and applicable overheads.
The generation of a concrete estimate allows you to anticipate costs and material needs prior to work. This process allows contractors to provide realistic costs, exercise financial control, and complete projects without problems.
Although professionals with experience in estimating are critical for more substantial or complicated concrete works, accurate estimates are provided, which is the professionals’ key role.
Why Accurate Concrete Estimating Matters
The accuracy of your concrete estimates has a major impact on profits. Inaccurate estimation figures might lead to added hidden costs or material shortages that can tie up your project and burn your earnings.
Here’s why precise estimating is critical:
- Cost Control: Lack of precise figures regarding materials and labor maximizes wastage and protects against unexpected cost debacles.
- Bidding Accuracy: Once your estimations are right, it is easier to win contracts without compromising your business gains.
- Project Planning: Careful estimates make for a smooth rationing between deliveries and workers.
- Client Confidence: A detailed estimate builds trust with clients and stakeholders by showing you’ve done your homework.
Components Included in a Concrete Estimate
To create a complete and accurate concrete estimate, you need to account for several key elements:
- Materials: Cement, sand, gravel, water, and any specified admixture or additive.
- Labor: Payment of workers’ wages for concreting placement, verification, and curing.
- Equipment: Equipment that will be needed for concrete will include mixers, pumps, vibrators and other finishing equipment.
- Formwork: Wood or metal members used to shape concrete before it is cast.
- Reinforcement: Rebar, wire mesh, or fibers, depending on structural requirements.
- Finishing and Curing: Surface finishing, sealers, and curing compounds.
- Transportation: Delivery charges for concrete and other materials.
- Waste: Additional amounts of concrete required for spills, over-excavation, or depth inconsistencies.
How to Calculate Concrete Volume
Initiate with calculating the amount of concrete needed to assess your project’s size. Concrete is measured by cubic yards in the US and cubic meters according to the metric system.
Basic Formula:
Length × Width × Thickness = Volume
- Convert all dimensions to feet
- Multiply to get cubic feet.
- Divide by 27 to convert to cubic yards.
Example:
Let’s say you’re pouring a driveway that is:
- 20 feet long
- 10 feet wide
- 4 inches thick (which is 0.33 feet)
Volume = 20 × 10 × 0.33 = 66 cubic feet
66 ÷ 27 = 2.44 cubic yards
Add 10% for waste:
2.44 × 1.10 = 2.68 cubic yards
You’d round up and order 2.75 to 3 cubic yards of concrete.
Common Methods of Concrete Estimating
There are a few different ways to approach concrete estimating, depending on the project size and complexity:
- Manual Estimating: Involves calculations using standard formulas, charts, or handbooks.
- Spreadsheet Templates: Customizable templates for tracking material quantities and prices.
- Estimating Software: Tools like PlanSwift, Bluebeam, or RSMeans can automate measurements, takeoffs, and costing.
- Unit Price Estimating: Calculates the cost depending on the last price per cubic yard or square foot.
There are merits and demerits for each method; manual estimation is suitable for simple projects, while sophisticated software streamlines and improves efficiencies for big tasks.
Key Factors That Affect Concrete Costs
Several variables can influence how much your concrete job will cost:
- Location: Local labor and material rates vary widely.
- Site Conditions: Sloped terrain, limited access, or poor soil may require extra work.
- Weather: Cold or wet conditions may slow down work and increase costs.
- Project Complexity: More formwork, decorative finishes, or unusual shapes take more time and materials.
- Labor Availability: The availability of experienced laborers determines whether or not wages can increase.
- Reinforcement Requirements: Projects that are highly used or set in zones with seismic activity may require more steel materials.
Tips for Improving Accuracy in Concrete Estimating
Getting your estimate right takes a mix of experience and attention to detail. Here are some best practices:
- Always review the drawings: Ensure dimensions are correct and scale is accurate.
- Include a waste factor: Waste should always be accounted for in order to prevent little mistakes or changes when implementing the project.
Consult local suppliers: Check for updated prices for concrete supplies and delivery services. - Use digital tools: Construction estimating software makes the process easy and helps to eliminate errors.
- Check local codes: Requirements for strength, reinforcement, or finish may impact cost.
- Break estimates down by section: Makes it easier to adjust individual components if needed.
Common Mistakes to Avoid
Even experienced professionals can overlook details. Watch out for these pitfalls:
- Underestimating Volume: A common mistake is failing to adjust for slope, curves, or thickness variations. Always double-check your math.
- Ignoring Formwork or Rebar: These are usually the primary cost, particularly when construction activity is increasing.
- Skipping Site Prep Costs: Soil preparations such as clearing, grading; or compacting is essential and all of these cost labor time.
- Missing Finishing Requirements; Additional labor and materials may be necessary for such means as stamping, staining, broom finishes, and sealing.
- Not Planning for Curing Time: Curing impacts labor scheduling and can delay follow-up trades if not properly accounted for.
Benefits of Professional Concrete Estimating Services
Hiring a professional estimating service can give you several advantages:
- Save Time: Let experts handle the math while you focus on managing your crew and clients.
- Increase Accuracy: Professional estimators use industry-standard software and current pricing databases.
- Win More Bids: Detailed and competitive proposals make your business more attractive to clients.
- Scale with Confidence: Take on bigger projects knowing you have reliable data behind your costs.
- Fewer Surprises: Comprehensive estimates reduce the risk of budget overruns, delays, or change orders.
FAQs
What is concrete estimating?
Concrete estimating measures the amount of concrete needed in a construction site. It addresses the method of calculation of volume, allowances for waste, and estimation of expenditure on materials, labour and construction equipment.
How do you estimate concrete?
Start estimating concrete by measuring the planned pour’s length, width, and depth. Multiply the dimensions to get volume in foot-cubed or meters-cubed, then convert that quantity to yard-cubed or meter-cubed for uniform measurement. Add a waste factor, usually 5–10%.
How to calculate the quantity of concrete?
Use this formula:
Volume = Length × Width × Depth
Then convert the result to cubic yards (if in feet) by dividing by 27. For example, a 10 ft × 10 ft slab that’s 0.5 ft thick is 5 cubic feet. Divide by 27 = 1.85 cubic yards.
What is the concrete method?
Concrete methods usually involve a variety of construction practices, such as mix design, site pouring, and post-pour care measures. This ensures that the concrete will possess reasonable strength, longevity, and operational nature.
What material is concrete?
The concrete composition contains cement, sand, gravel (or crushed stone), and water. Various chemicals, such as fly ash or admixtures, may be added to the concrete mix for better strength, faster setting, or greater durability.
Conclusion
Accurate concrete estimating is essential in project planning because it will influence your expenses, timeline, and overall success. Regardless of whether you are involved up close or remain at a distance, you can at least understand the basic principle well enough to make informed decisions to avoid expensive errors. Compliance with existing standards and the use of the appropriate tools help ensure your concrete work continues effectively and at an affordable cost.
Need help with concrete estimating? At Prime Estimation, our takeoffs deliver accurate, timely, and economical results, allowing you to build wisely. Contact us to let’s work together on your next building project.
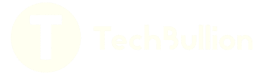