Electric vehicles (EVs) have revolutionized the automotive industry by offering an environmentally friendly alternative to traditional combustion engines, and their electrical systems are a pivotal aspect of this transformation. A critical component within these systems is the use of precharge and discharge resistors. These resistors play a vital role in managing the high-voltage circuits integral to EV operation, ensuring both safety and efficiency. Their function is particularly crucial during the initial power-up phase and when the vehicle is turned off, as they regulate the current flow to prevent damage to sensitive electronic components.
Precharge resistors are employed during the vehicle’s start-up process to mitigate the surge of current that could damage components such as capacitors and the battery management system (BMS). By controlling the inrush current, these resistors prevent potential short-circuits and contribute to extending the lifespan of the vehicle’s electrical systems. Their role is not only crucial for safety but also for maintaining the reliability and stability of high-voltage systems. As the demand for electric vehicles increases, the optimization of precharge resistors remains a focus for engineers aiming to improve performance and efficiency[1][2].
Similarly, discharge resistors ensure the safe de-energizing of EV systems once the vehicle is switched off. These resistors facilitate the quick discharge of DC link capacitors, crucial for maintaining the safety and longevity of electronic components. Unlike industrial systems where discharge times can be prolonged, EVs require swift discharge processes to maintain operational efficiency. This necessity underscores the importance of discharge resistors in preserving the performance and safety standards of electric vehicles[3][4].
The use of precharge and discharge resistors has become a central topic of discussion in the automotive industry due to its implications for both safety and performance. As manufacturers strive to enhance the design and functionality of EVs, ongoing research and development in resistor technology remain critical. Innovations such as the elimination of bulky power resistors, which reduce heat dissipation and accelerate the precharge process, exemplify the industry’s commitment to advancing electric vehicle technology. These advancements are pivotal for the broader adoption and success of electric transportation technologies[5][6].
Basics of EV Electrical Systems
Electric vehicles (EVs) have distinct electrical systems designed to manage and optimize energy use. At the core of these systems is the battery, which supplies power to the electric motor through a series of processes that ensure efficient energy conversion and usage.
Battery Management and C-Rates
The battery management system (BMS) is crucial for maintaining the balance between performance, longevity, and safety of the battery. It regulates charge and discharge rates, often measured in C-rates, which directly impact the vehicle’s range and performance. To optimize these factors, a BMS typically maintains discharge rates between 0.2 and 0.5C during regular driving conditions, reserving higher discharge rates for specific situations like overtaking or climbing steep inclines[7].
Discharge Circuits and Safety Mechanisms
The discharge circuit in an EV is responsible for converting the battery’s direct current (DC) into alternating current (AC) to power the motor. This conversion is achieved using components such as diodes, capacitors, and transistors. To safeguard against electrical malfunctions, these circuits incorporate safety features like fuses and circuit breakers[4]. These mechanisms ensure that the vehicle operates safely and efficiently under various conditions.
Role of Resistors
Resistors play a pivotal role in EV electrical systems, especially within the braking system. Unlike conventional vehicles that lose energy as heat during braking, EVs employ regenerative braking to recapture some of this energy, which is then stored back in the battery[8].
Additionally, precharge resistors are essential in managing power surges during charging and discharging processes. They help limit current flow, preventing damage to the battery cells and the BMS, thereby extending battery life and preserving its performance[9].
Importance of Precharge in High Voltage Systems
Precharging is an important process, particularly for high voltage systems. It involves controlling the rise time of the system voltage during power-up to reduce stress on components. Proper precharge practices prevent sudden surges that could otherwise lead to system damage. For instance, a high voltage system may take several seconds to precharge effectively, allowing components like an electronics control unit with significant input capacitance to stabilize before full power is applied[6]. This procedure is vital for maintaining the integrity and reliability of the EV’s electrical system.
Precharge Resistors
Precharge resistors are essential components in electric vehicles (EVs) that play a crucial role during the initial power-up phase of the vehicle’s high-voltage system. They are designed to slowly charge the capacitor in the early stages, preventing an excessive inrush current that could damage high-voltage electrical components if left unchecked[1]. Without these resistors, the direct application of high voltage to the capacitor would be equivalent to an instantaneous short-circuit, leading to a potentially damaging high current[1].
The functionality of precharge resistors is pivotal in determining the speed of the pre-charging process, the spatial footprint of the resistor within the vehicle, and the overall safety, reliability, and stability of the high-voltage system[1]. They are typically used in conjunction with a relay or precharge contactor and are installed on the positive leg of the circuit in parallel with the main relay[2].
In practice, precharge resistors are employed in a variety of systems, ranging from consumer electronics to vehicle applications, with the latter requiring pre-charging multiple times per day due to frequent usage[6]. This frequent activation helps increase the lifespan of electronic components and enhance the reliability of the high voltage system[6].
Additionally, advanced designs may incorporate time delay relays to disengage the resistor after a short duration, optimizing the precharge process[10]. By understanding and effectively implementing precharge resistors, engineers can ensure a more efficient and durable high-voltage system in EVs, ultimately contributing to the broader adoption and advancement of electric transportation technologies[8].
Discharge Resistors
Discharge resistors play a crucial role in the operation of electric vehicles (EVs), specifically in safely discharging the DC link capacitors once the vehicle has been switched off[3]. These resistors are typically utilized in inverters and are designed to be high-voltage-resistant and non-inductive, allowing for various circuit configurations[3]. Their compact and lightweight construction enables easy integration onto printed circuit boards, optimizing space and weight in the vehicle’s design[3].
In EVs, the efficiency of discharging capacitors is paramount, contrasting with industrial systems where resistors may be left on permanently, with a discharge time extending up to five minutes[4]. In contrast, the need for swift discharge in vehicles necessitates a different approach to ensure efficiency and safety[4]. This is often achieved by attaching a precharge resistor to the contactor, which helps in managing the discharge process effectively[4]. The choice of resistor value is critical to balance power efficiency and the discharge time required[4].
The discharge process in EVs not only facilitates the safe de-energizing of capacitors but also contributes to the overall reliability and longevity of the vehicle’s electronic components[6]. By incorporating resistors with optimized discharge times, EVs can maintain their performance and safety standards, ensuring that electronic components are preserved, thereby prolonging their lifespan[6].
Technical Considerations
The implementation of precharge and discharge resistors in electric vehicles (EVs) involves several technical considerations, each playing a crucial role in ensuring the safety, efficiency, and longevity of the vehicle’s electrical system.
Precharge Resistor Design
The design of precharge resistors in EVs requires meticulous attention to various conditions and working environments[1]. A precharge resistor is vital for managing the initial inrush of current when an EV is powered on, thus preventing damage to the electrical components by limiting the surge of power[9]. This resistor helps to eliminate costly power resistors with contactors, reducing heat dissipation and potentially providing a faster bus pre-charge[5].
Selecting the appropriate resistor involves choosing one with a suitable voltage and current rating. For instance, a relay rated at 125vdc may suffice for short-term current requirements[11]. Moreover, the choice of resistors should also consider the impact on overall vehicle performance and efficiency, as even minute resistances can affect the operation[12].
Discharge Resistor Considerations
Discharge resistors, used for managing energy release during braking or emergency stops, are crucial for EV safety. These resistors ensure quick deceleration without causing damage to the battery or other electrical components[8]. A leading luxury sports car manufacturer collaborated with a supplier to develop discharge resistors that offered high energy capacity and customizable specifications, highlighting the importance of a tailored approach to resistor design[3].
The circuit design of discharge resistors, whether employing single pulse or constant power discharge methods, impacts their size and weight. Smaller designs, which are achievable with constant power pulse discharge, offer the advantage of reduced weight and space requirements, which are critical for high-performance vehicles[3].
Battery Management System (BMS) Integration
The integration of precharge and discharge resistors with the EV battery management system (BMS) is essential for optimizing vehicle performance. A BMS typically maintains discharge rates between 0.2 and 0.5C to balance performance, battery longevity, and safety[7]. High discharge rates are reserved for specific situations such as highway overtaking or emergency maneuvers, minimizing battery cell degradation over time[7].
Industry Perspectives
The use of precharge and discharge resistors in electric vehicles (EVs) has become a focal point in the automotive industry as it grapples with the dual challenges of ensuring safety and enhancing efficiency. After nearly a decade of technological advancements, the EV industry has developed substantial technical expertise in the design of electric vehicle components, particularly concerning precharge resistors. These resistors play a crucial role in high-voltage circuits, ensuring that components like the motor controller and high-voltage accessories are pre-charged properly to manage current flow and safeguard the system[1][8].
In the context of safety, precharge resistors are indispensable. They prevent abrupt electrical surges that could otherwise damage vital components such as large capacitors in the motor controller or other high-voltage systems like the DCDC converters and on-board chargers[1][8]. By carefully balancing the power efficiency and discharge time, precharge resistors facilitate a controlled and reliable startup process, which is crucial given the repeated use of the system multiple times per day in vehicle applications[4][6].
From a performance perspective, the industry has recognized that these resistors can also contribute to improved efficiency. By integrating compact and lightweight designs, manufacturers can reduce the overall size and weight of the electrical systems in EVs, which is a critical consideration in vehicle design[3]. Furthermore, the elimination of costly power resistors and their associated contactors, as suggested in some innovative solutions, helps in reducing heat dissipation and enhancing the speed of pre-charge, potentially optimizing the vehicle’s overall performance[5].
As the EV landscape continues to evolve, industry experts emphasize the importance of ongoing research and development in the field of resistors. By addressing both the safety and efficiency concerns, the industry is better positioned to meet the demands of modern technology and drive the future of transportation[8].
Alternatives and Innovations
Recent advancements in electric vehicle (EV) technology have led to the exploration of alternatives to traditional precharge and discharge resistors, which are crucial in managing the high voltage systems within these vehicles. One notable innovation involves the elimination of the costly power resistor and its associated contactor, a development that significantly reduces heat dissipation and may provide a faster bus pre-charge process[5].
The design of precharge resistors has evolved over nearly a decade of development in the field of new energy electric vehicles. Engineers and manufacturers have accumulated substantial technical knowledge in this area, focusing on optimizing the pre-charging circuit to meet various operational conditions and requirements[1]. Innovations in this field aim to enhance the reliability and longevity of high voltage systems by implementing more efficient precharge solutions, which are activated multiple times per day in vehicle applications[6].
One example of innovation in this area comes from a collaboration between a leading luxury sports car manufacturer and Miba, where the development of discharge resistors with high energy capacity and customizable specifications was a key focus[3]. Such collaborations emphasize the industry’s push towards more tailored and efficient components, addressing the specific needs of high-performance electric vehicles.
Moreover, the integration of advanced battery management systems (BMS) in EVs allows for better control of charging and discharging processes, maintaining optimal discharge rates between 0.2 and 0.5C to ensure an ideal balance between performance, battery longevity, and safety[7]. These advancements contribute to minimizing mechanical stress and thermal issues, further extending the battery’s lifespan and enhancing overall system efficiency.
Further Reading
For those interested in delving deeper into the intricacies of precharge and discharge resistors in electric vehicles, there are several avenues of exploration. The development of electric vehicles over the past decade has accumulated significant technical knowledge, particularly regarding the design of precharge resistors, which need to consider various conditions and working environments[1].
A notable example is the collaboration between a leading luxury sports car manufacturer and Miba, which resulted in the development of discharge resistors with high energy capacity and customizable specifications[3]. These resistors ensure safe and reliable operation for both precharge and discharge applications, underscoring the importance of such components in the overall safety and efficiency of electric vehicles[3].
Additionally, understanding the impact of inrush current, which can potentially cause damage to relay contacts, highlights the necessity of a precharge resistor in the pre-charging circuit of an EV high-voltage system[11][2]. The schematic designs for such systems reveal the complexity and precision required to manage electrical components effectively[2].To explore these topics further, one might investigate various scholarly articles and industry reports that discuss the energy value chain in EVs and how components like precharge and discharge resistors contribute to efficient energy management[3].
References
[1] Etengoff, A. (2024, February 6). How do EV battery cell charge and discharge rates compare? Ev Engineering Online. https://www.evengineeringonline.com/how-do-ev-battery-cell-charge-and-discharge-rates-compare/
[2] nikita. (2014, March 14). Discharge circuit in electric vehicle. Physics Forums. https://www.physicsforums.com/threads/discharge-circuit-in-electric-vehicle.743270/
[3] Resistor Cermet. (2024, September 17). What is the role of resistors in electric vehicles? Resistor Cermet. https://www.resistorcermet.com/role-of-resistors-in-electric-vehicles/
[4] Mulani, B. (2022, December 20). Role of pre-charge resistors in BMS. Valipod. https://www.valipod.com/post/role-of-pre-charge-resistors-in-bms
[5] Wikipedia contributors. (n.d.). Pre-charge. Wikipedia. https://en.wikipedia.org/wiki/Pre-charge
[6] ZENITHSUN. (2021, July 25). The secret of using precharge resistors for electric vehicles. One Resistor. https://www.oneresistor.com/news/the-use-of-pre-charging-resistors-for-electric-vehicles/
[7] Guchen EAC. (2022, June 30). Precharge control circuit. Guchen EAC. https://www.guchen-eac.com/who/news/precharge-control-circuit.html
[8] DIY Electric Car. (n.d.). Dual contactors and precharge resistors question. DIY Electric Car. https://www.diyelectriccar.com/forums/showthread.php/dual-contactors-and-precharge-resistors-question-163506.html
[9] Miba. (n.d.). Bleeding resistor for e-cars: Miba discharge resistors. Miba. https://www.miba.com/en/product-areas/power-electronics/bleeding-resistor-for-e-cars-miba-discharge-resistors/
[10] Ipek, E. (2022, December 12). Pre-charge resistor. Battery Design. https://www.batterydesign.net/pre-charge-resistor/
[11] Rayco. (2021, August 5). Precharge: What is it? Why do I need it? How do I do it? DIY Electric Car. https://www.diyelectriccar.com/threads/precharge-what-is-it-why-do-i-need-it-how-do-i-do-it.25419/
[12] Endless Sphere. (n.d.). Pre-charge resistor help. Endless Sphere. https://endless-sphere.com/sphere/threads/pre-charge-resistor-help.18572/
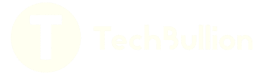