Functional prototypes are essential in new product development. This article explores the benefits of functional prototypes and the pivotal role of plastic prototype companies in developing them.
What Is A Functional Prototype?
Functional prototypes are usually talked about alongside prototypes for appearance and structure. Unlike appearance prototypes for appearance testing and structural prototypes for structure testing only, functional prototypes aim to test the form, structure, fit, and function together for a new design of a physical product. A functional prototype is very close to the final product and thus is more expensive than an appearance or a structural prototype.
What Are the Benefits of Functional Prototypes?
Functional prototypes enable designers and engineers to identify and address potential issues before moving into full-scale production. Below are the several advantages a functional prototype can offer.
New Design Verification
By simulating the final product, functional prototypes are crucial in mitigating risks and ensuring that the end product meets the desired specifications. Key industries such as automotive, aerospace, consumer electronics, and medical devices rely heavily on functional prototypes to validate designs and bring innovative products to market.
Gathering Feedback
Furthermore, functional prototypes are instrumental in gathering valuable feedback from stakeholders, facilitating informed decision-making and refinement of the product design. This iterative approach to prototyping is invaluable in achieving product excellence and customer satisfaction.
Cost- & Time-Effectiveness
Creating a functional prototype saves money and time for businesses before going to mass production. Testing via functional prototypes helps designers and engineers find defects in the present design. Then they can refine the errors before investing too much in costly steel molds for scale manufacturing.
The fast turnaround time for building functional prototypes within days can also speed up the product development cycle.
How to Create A Functional Prototype?
Creating functional prototypes in collaboration with plastic prototype companies involves a series of well-defined steps to translate design concepts into tangible, testable prototypes. These steps typically include:
Design Review and Preparation
Product development teams collaborate with plastic prototype companies to review the design specifications and prepare the necessary files for prototype production, including CAD drawings(in STP, STEP, IGS, or X_T format), 2D files(for tolerance and other detailed requirements), and BOM (Bill of Materials) list. This phase ensures the design is feasible for the chosen manufacturing process and materials. Sometimes, a product designed for plastic injection molding may not be suitable for CNC machining to make a functional prototype.
Material Selection and Procurement
The appropriate materials are selected in consultation with the plastic prototype company based on the design requirements. These materials may range from various plastics to specialized composites based on the application and performance. ABS is the most commonly used plastic material for one-off functional prototypes in CNC machining.
Prototype Production
With advanced manufacturing technologies such as 3D printing, CNC machining, vacuum casting, rapid tooling, or Reaction Injection Molding(RIM), the plastic prototype company produces functional prototypes according to the specified design parameters. Precision and attention to detail are critical in achieving prototypes that accurately reflect the final product’s form and function.
Testing and Iteration
Once the functional prototypes are ready, they undergo rigorous testing to evaluate their performance, fit, and functionality. Any identified issues or areas for improvement are communicated back to the product development team, leading to iterative refinements in the design.
Validation and Finalization
Through collaborative feedback and iteration, the functional prototypes can guarantee that they meet the desired performance criteria. This iterative process continues until the prototype achieves the requisite level of functionality and performance.
The materials and technologies utilized by plastic prototype companies play a pivotal role in the successful creation of functional prototypes.
Plastic Prototype Companies: Key Players in Prototype Development
Plastic prototype companies are at the forefront of prototype development, producing functional prototypes that resemble the final product in form and function. These companies possess extensive expertise in utilizing advanced manufacturing technologies and materials to bring product designs to life as functional prototypes.
The services offered by plastic prototype companies encompass a wide range of capabilities, including 3D printing, CNC machining, vacuum casting, rapid tooling, and RIM. Equipped with state-of-the-art facilities and a skilled workforce, prototyping companies can translate design concepts into physical prototypes with precision and efficiency.
Moreover, plastic prototype companies play a pivotal role in guiding product development teams through the iterative process of prototype refinement. By offering suggestions on material selection, manufacturing processes, and design optimization, these companies contribute to making functional prototypes that meet the highest quality and performance standards.
Final Thoughts
To sum up, plastic prototype companies are vital for speeding up product development, reducing risks, and sparking innovation in various industries. Their skill in making functional prototypes allows for quick testing and refining, shaping the path of product innovation ahead.
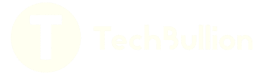