Introduction
The automotive industry has witnessed remarkable transformations and innovations since its inception. Over the years, vehicles have evolved from simple means of transportation to complex technological machines. Subsequently, the materials and processes used in their production have also undergone significant changes. One notable advancement in automotive manufacturing is the growing reliance on molded plastic parts. These components are shaped through various techniques like injection molding, blow molding, and compression molding, making them indispensable in constructing and designing modern vehicles. Molded plastic parts offer many benefits to the automotive industry including lightweight construction, cost-effectiveness, and exceptional customization capabilities. These advantages enable manufacturers to comply with strict environmental regulations and enhance fuel efficiency while achieving unique aesthetic designs. In this article, we will explore the role and importance of plastic injection molding in the automotive industry.
Historical Perspective
The history of the automotive industry is closely tied to advancements in materials technology. A notable transformation has been witnessed, shifting from metal parts to plastic components in the industry. This change has been driven by a pursuit for efficiency, safety, and innovation.
During the early stages of automobile manufacturing, cars were mainly constructed using a combination of metal, wood, and glass. Among these materials, steel emerged as the frontrunner due to its strength and ease of manipulation. It found widespread application in critical structural components such as the chassis and body. During the 1980s and 1990s, as safety standards became more stringent, plastics began to play a vital role in automotive design. Engineers discovered that certain types of plastics could effectively absorb and distribute energy during collisions, significantly enhancing vehicle safety. This era also witnessed the emergence of high-performance plastics like polycarbonates and polyamides, specifically engineered to withstand extreme temperatures and harsh chemical environments.
III. Benefits of Using Plastic Injection Molding in Automotive Manufacturing
Weight Reduction and Fuel Efficiency:
Plastic injection molding plays a significant role in reducing the overall weight of automotive components compared to traditional materials like metals. This decrease in weight benefits vehicles, as they require less energy to operate. This has also led to improved fuel efficiency, which is particularly important given the growing concerns for the environment and automotive emissions.
Cost-effectiveness:
Plastic injection molding is a highly efficient and scalable process. It has the capability to produce large volumes of components with consistent quality. This process can create complex parts in a single step, reducing labor costs and streamlining the production process. As a result, overall manufacturing costs are lower. Additionally, plastics are cheaper compared to metals, leading to additional savings on raw material expenses.
Design Flexibility and Aesthetics:
Plastic injection molding offers designers exceptional design freedom, allowing them to create intricate and complex designs that would be difficult to achieve with metals. This flexibility empowers designers to innovate and enhance the visual appeal of vehicle components by incorporating sleek, modern, and highly stylized components. It also contributes significantly to a vehicle’s branding and overall aesthetic refinement.
Durability and Resistance to Corrosion:
Plastics manufactured through injection molding possess exceptional durability and resilience across various conditions. Unlike metals, which are susceptible to rust and corrosion in harsh environments, engineered plastics can withstand exposure to moisture, chemicals, and extreme temperatures without any degradation. This property contributes to the durability of components, reducing the need for expensive and frequent replacements while enhancing the overall endurance and dependability of vehicles.
Common Automotive Components Made Through Plastic Injection Molding
Interior Parts: Dashboard, Knobs, Controls: Plastic injection molding has a wide range of applicability in the production of various interior components for vehicles. The dashboard is one of the interior components manufactured using plastic injection molding. Similarly, knobs and controls such as climate control dials and gear shifts are commonly manufactured through this process. As a result, it facilitates the creation of ergonomic and visually appealing designs that exhibit durability while remaining cost-effective.
Exterior Parts: Bumpers, Grilles, Light Housings: Plastic injection molding offers a unique combination of resilience and design flexibility in manufacturing exterior components. Bumpers, made from high-impact-resistant plastics, effectively absorb and distribute energy during collisions, minimizing potential damage. Grilles play a dual role by protecting the engine bay while allowing proper airflow, often custom molded to ensure precise fit and finish. Light housings, including headlights and taillights, commonly utilize clear or colored plastics that are formed with utmost precision to provide optimal sealing and alignment with the vehicle’s overall design.
Engine Components: Containers, Seals, Valves: Plastic injection molding is indispensability in manufacturing critical engine components that endure extreme temperatures and harsh chemicals. Components like windshield washer reservoirs and coolant tanks, which frequently rely on molded plastics for their exceptional resistance to leaks and long-lasting durability are some of the components manufactured using this process. Seals and gaskets are also made from high-performance plastics to protect the engine against leakage while maintaining optimal pressure. Additionally, valves responsible for regulating fluid and gas flow within vehicle engines are now embracing high-strength, heat-resistant plastics to minimize weight without compromising performance.
Challenges and Solutions in Automotive Plastic Injection Molding
There are various challenges associated with automotive plastic injection molding. These include:
- Ensuring High-Quality and Durable Parts: To ensure high-quality and durable automotive plastic injection molded parts, maintaining consistency is key. However, this can be a challenge due to variations in material properties, process parameters, or mold design that may result in substandard parts. A solution for this challenge is implementing strict quality control procedures and regular equipment maintenance. Additionally, advanced process monitoring technologies can be utilized for better part quality management. To enhance durability, advancements in material science play a crucial role as the development of new, high-performance polymers contributes to stronger parts.
- Overcoming Molding Defects: Warping, Sinking, Bubbles: Molding defects like warping, sinking, and bubbles have significant challenges to the structural integrity and appearance of components. These issues commonly occur due to uneven cooling, inappropriate material selection, or incorrect process parameters. To overcome these defects, it is crucial to optimize the mold design for uniform cooling, precisely control process parameters such as temperature and pressure, and select suitable materials. Additionally, simulation software can be used to predict and address potential issues before actual production commences.
- Addressing Environmental Concerns and Sustainability: With increasing pressure to minimize the environmental impact of automotive plastic injection molding, addressing issues such as the use of plastics has become essential. Plastics obtained from non-renewable sources have the potential to contribute to pollution if not managed effectively. One solution is adopting a circular economy approach that emphasizes recycling and reusing materials. Using bioplastics sourced from renewable sources or incorporating recycled plastics into injection molding processes, a viable path towards reducing environmental impact is created. Manufacturers can invest in research and development efforts aimed at innovating eco-friendly polymers and supporting effective recycling programs.
Future Trends: Sustainable and Innovative Practices
Use of Bioplastics and Recycled Materials: To support global sustainability goals, the industry is increasingly adopting bioplastics derived from renewable sources like corn or sugarcane. Additionally, using recycled materials is another viable option. These alternatives reduce reliance on petroleum-based raw materials and promote a circular economy approach. This approach is vital for minimizing environmental impact.
Integration of Smart Technology in Plastic Components: The incorporation of smart technologies into plastic components is a major trend. By integrating sensors and connectivity features, these components go beyond their structural and aesthetic functions. They actively contribute to the vehicle’s operation, enhancing safety, efficiency, and user experience.
Advanced Molding Techniques for Improved Efficiency: As the demand for more complex and higher-quality parts increases, advanced molding techniques are expected to become more widespread. These techniques include gas-assist injection molding and overmolding, which offer greater design flexibility, reduced material usage, and improved component properties. By addressing efficiency and quality simultaneously, these methods meet the evolving needs of manufacturers.
VII. Conclusion
The future of automotive plastic injection molding is heading towards an innovative and sustainable landscape. This transformation is characterized by the adoption of eco-friendly materials, integration of smart technologies, and utilization of advanced molding techniques. Companies like TDL molds are on the forefront of developing and enhancing innovative and sustainable manufacturing in automotive plastic injection molding.
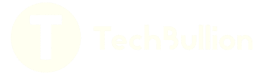