Die-cutting is an essential process in the manufacturing of customized business materials, acting as a bridge between creativity and functionality. This specialized technique offers companies the flexibility to produce unique shapes and intricate designs, transforming ordinary materials into custom-made solutions tailored to meet specific business needs. Whether it’s crafting a standout business card, intricate packaging, or perfectly fitted machine components, die-cutting pushes the boundaries of what can be achieved through innovative engineering and design.
A Versatile Solution Across Industries
From automotive manufacturers to electronics producers, die-cutting services cater to a plethora of industries. Automotive die-cutting, for example, is critical in producing parts that conform exactly to the shapes and specifications required for optimal vehicle performance and safety. Similarly, die-cut solutions for electric vehicle batteries ensure precision in this rapidly evolving field, where exact specifications are crucial for battery performance and longevity.
In the realm of electronics, PCB Shielding Gaskets made through die-cutting protect devices from electromagnetic interference, enhancing device reliability and function. Likewise, Die-cutting Mylar Film and Die-cutting EMI Foam are used extensively to shield sensitive components from external noise and disturbance, ensuring that products meet strict industry standards for performance.
The role of die-cutting extends also to thermal management within devices. Products like Thermal Gap Pads are made using die-cutting processes to fit perfectly within electronic assemblies, enhancing cooling efficacy and overall device performance. Silicone Rubber Gaskets, another product born from the precision of die-cutting technology, provide excellent sealing properties, crucial for protecting against moisture and contaminants in a variety of applications.
Innovation in Materials and Design
One key advantage of using die-cutting in business material production is its compatibility with a wide range of materials. Foil Heat Shields and Die-cutting Conductive Foam are examples where even materials with delicate properties can be precisely shaped to fulfill specific functions, such as managing heat or conducting electricity within tight spaces.
This adaptability is particularly valuable in industries where high-precision parts are critical. It allows for rapid prototyping and scaling up to high-volume production without losing accuracy. The precision delivered by advanced die-cut technologies ensures that each piece is consistently produced to exact specifications, reducing waste and improving overall efficiency.
Business Through Customization
Customization is where die-cutting truly shines, providing businesses with the tools to create branding elements that are as functional as they are eye-catching. This ability to customize does not stop at visual appeal; it also extends to functional customization necessary for creating pieces that integrate seamlessly into larger systems or products. The meticulous precision and efficiency provided by high-end die-cut solutions enable businesses to bring their most ambitious projects to fruition affordably and reliably.
Seamless Production From Concept to Reality
The integration of state-of-the-art die-cutting solutions helps streamline production processes from initial design to final output. Companies specializing in die-cutting have honed their processes to handle both detailed small-scale prototypes and extensive production runs efficiently. This ability to scale without sacrificing detail or quality ensures that businesses can respond swiftly to market changes or demands without compromising on the quality of their materials.
As businesses continue to search for innovative ways to stand out and enhance their operational efficiencies, die-cutting stands out as a pivotal technology. The myriad applications from Foil Heat Shield in aerospace engineering to Die-cutting Conductive Foam in portable electronics illustrate the versatility and indispensability of this technology.
Die-cut technologies offers a formidable competitive edge by allowing unparalleled precision, efficiency, and customization. With continuous advancements in this field, businesses can expect even greater capabilities, making their materials not just components but pivotal aspects of their brand identity and operational success.
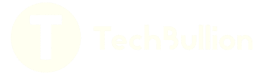