The Psychology Behind Delayed Equipment Upgrades
The resistance to equipment upgrades stems from several understandable business concerns. First and foremost is the significant capital expenditure that new industrial equipment represents. For many operations managers, the immediate impact on quarterly budgets creates hesitation, particularly when existing equipment continues to function, albeit suboptimally. This “if it isn’t broken, don’t fix it” mentality persists throughout many industrial operations.
Additionally, the perceived disruption to established workflows gives pause to decision-makers. Introducing new equipment requires reconfiguring production lines, retraining staff, and potentially experiencing temporary productivity dips during implementation. These transition costs, both tangible and intangible, create a psychological barrier that reinforces the status quo.
However, this delay-focused thinking comes with significant hidden costs that accumulate over time. Equipment that appears functional on the surface may be operating well below optimal efficiency levels. Modern machinery typically consumes less energy, requires fewer operators, experiences less downtime, and produces higher-quality output than aging equipment. These efficiency differentials compound daily, creating an invisible drain on profitability that grows increasingly burdensome as competitors embrace technological advancement.
Uncovering the Hidden ROI Drivers
The return on investment for industrial equipment upgrades extends far beyond the obvious metrics of faster production speeds. These hidden ROI drivers often go unnoticed in traditional cost-benefit analyses but provide substantial long-term value.
Reduced Downtime
Aging equipment requires more frequent maintenance interventions, with each instance creating a cascade of associated costs. Beyond the direct expense of repairs, businesses incur opportunity costs from lost production, labor inefficiencies during downtime, and potential deadline penalties with customers. Modern equipment’s improved reliability dramatically reduces these interruptions.
A manufacturing plant in Michigan recently reported that replacing a 12-year-old packaging line with current technology reduced unplanned downtime by 87%. This improvement alone delivered approximately $318,000 in annual savings through avoided production losses and maintenance costs—a figure that significantly accelerated the payback period for their investment.
Lower Labor Dependencies
The evolution of industrial automation continues to reshape labor requirements across manufacturing sectors. While older equipment often demands constant operator attention, modern machinery typically requires fewer staff to achieve the same or greater output. This reduction extends beyond simple headcount savings to include decreased training costs, lower turnover-related expenses, and minimized human error rates.
Investments in tools such as orbital wrappers often pay off faster than expected through labor savings and throughput gains, particularly in distribution and packaging operations where manual processes still predominate.
Consistent Output Quality
Quality consistency represents another significant but frequently overlooked ROI driver. Modern equipment typically delivers more precise manufacturing tolerances, better finish quality, and fewer defects than aging machinery. These improvements translate directly to reduced scrap rates, fewer customer rejections, and enhanced brand reputation—all of which contribute substantially to profitability.
A food processing operation in Oregon documented a 2.3% improvement in raw material yield after upgrading their production line equipment. This seemingly modest increase translated to approximately $430,000 in annual materials savings, demonstrating how small efficiency gains multiply dramatically at scale.
Energy Efficiency Gains
The energy consumption differential between older and newer equipment often provides another surprising source of returns. Modern industrial machinery typically incorporates advanced power management features, more efficient motors, and optimized operational cycles that collectively reduce energy usage by 15-40% compared to equipment manufactured just a decade ago.
For energy-intensive operations, these savings accumulate rapidly. A metal fabrication facility in Tennessee reported annual energy cost reductions of $217,000 after upgrading their primary production equipment—an improvement that represented nearly 18% of the total upgrade investment recovered in just the first year of operation.
Manual vs. Modern: The Real-World Impact
To illustrate the comprehensive impact of equipment upgrades, consider these comparative scenarios based on composite industry data:
Scenario 1: Warehouse Pallet Wrapping
A distribution center handling 400 pallets daily relied on manual wrapping methods, requiring three full-time employees and consuming substantial amounts of stretch film. The manual process created inconsistent wrap patterns, leading to occasional load failures during transit and associated replacement costs.
After implementing an automated orbital wrapper, the operation reduced labor requirements to a single part-time operator, decreased film consumption by 37%, and virtually eliminated in-transit load failures. The cumulative annual savings reached $163,000, providing full ROI within 14 months while simultaneously increasing daily throughput capacity by 22%.
Scenario 2: Production Line Automation
A manufacturer operating with 15-year-old assembly equipment employed 12 workers across two shifts to maintain production targets of 6,000 units daily. Frequent breakdowns created unpredictable delivery schedules and quality inconsistencies.
After upgrading to a modern automated production line, staffing requirements decreased to five operators while daily output increased to 7,800 units. Maintenance costs decreased by 68%, and product quality improved significantly. The annual operational savings of $876,000 combined with increased sales capacity delivered complete investment recovery in just under two years.
These scenarios highlight a critical insight: the ROI calculation for equipment upgrades must encompass all affected operational aspects rather than focusing solely on the most obvious benefits. When comprehensive analysis includes labor savings, material efficiency, quality improvements, maintenance reductions, and capacity increases, the investment case typically becomes substantially more compelling.
Automation’s Role in 2025’s Competitive Landscape
The accelerating pace of automation adoption has fundamentally altered the competitive dynamics across manufacturing and distribution sectors in 2025. What once represented optional efficiency improvements now increasingly constitutes table stakes for competitive viability.
This shift stems from several interconnected market forces. Labor market dynamics continue to challenge industrial employers, with skilled operator shortages persisting across most manufacturing regions. This constraint places particular pressure on operations relying heavily on manual processes or aging equipment requiring specialized maintenance expertise.
Simultaneously, customer expectations regarding delivery speed, production flexibility, and quality consistency continue to intensify. These demands create particular challenges for operations lacking the responsiveness and precision that modern equipment provides.
Perhaps most significantly, the competitive gap between automation leaders and laggards continues to widen. Early adopters of advanced industrial equipment gain compounding advantages through earlier ROI realization, which subsequently funds additional upgrades. This virtuous cycle creates accelerating differentiation between forward-looking operations and those maintaining outdated equipment.
Industry analysis indicates that manufacturers who have systematically upgraded their core production equipment over the past three years report average profit margin improvements of 4.7 percentage points compared to competitors maintaining legacy systems. This differential highlights how equipment modernization increasingly separates market leaders from followers.
Strategic Approaches to Equipment Upgrade Decisions
Given the significant competitive implications of equipment modernization, operations leaders benefit from adopting structured approaches to upgrade decisions:
Total Cost of Ownership Analysis
Rather than focusing exclusively on purchase price, comprehensive evaluation should incorporate all lifecycle costs associated with both existing and proposed equipment. This analysis includes energy consumption, maintenance requirements, labor needs, consumable usage, quality-related expenses, and anticipated residual value.
The total cost perspective typically reveals that apparently expensive modern equipment delivers substantially lower lifetime costs than maintaining aging machinery—particularly when accounting for the opportunity costs associated with reduced capabilities.
Phased Implementation Strategies
For operations unable to undertake comprehensive equipment overhauls, strategic phased approaches often provide viable alternatives. Identifying critical production bottlenecks or particularly problematic equipment allows organizations to prioritize upgrades where they’ll deliver maximum immediate impact.
This targeted approach can generate early wins that improve cash flow and build organizational confidence in the modernization process. These initial successes often facilitate subsequent upgrade phases by demonstrating tangible ROI examples internally.
Financing and Leasing Considerations
Modern equipment financing options frequently allow organizations to align payment structures with anticipated savings streams, effectively creating cash-flow-positive upgrades from implementation onward. Leasing arrangements in particular often enable access to cutting-edge equipment while preserving capital for other strategic priorities.
Additionally, various tax incentives designed to encourage industrial modernization can significantly impact the financial analysis. These programs typically reduce effective equipment costs through accelerated depreciation schedules or direct tax credits for productivity-enhancing investments.
Making the Case for Equipment Modernization
For operations professionals advocating for equipment upgrades within their organizations, several approaches can help build compelling internal cases:
- Document Current Inefficiencies – Establish baseline performance metrics for existing equipment, including downtime frequency, labor requirements, energy consumption, and quality variation. These measurements create the foundation for calculating improvement potential.
- Develop Comprehensive ROI Models – Ensure financial analyses incorporate all relevant factors rather than focusing solely on equipment costs versus speed improvements. The most persuasive models include maintenance savings, labor efficiency gains, quality improvements, and capacity increases.
- Consider Competitive Positioning – Frame equipment upgrades as strategic competitive necessities rather than optional improvements. This perspective shifts the decision context from “whether to upgrade” to “how quickly can we implement.”
- Start Small When Necessary – When comprehensive upgrades face resistance, identify opportunities for limited-scope pilot implementations that can demonstrate concept validity and generate organizational support for broader initiatives.
Conclusion: The Strategic Imperative of Equipment Modernization
As industrial equipment continues its rapid technological evolution, the strategic implications of upgrade decisions extend far beyond operational efficiency. In 2025’s increasingly competitive manufacturing landscape, equipment modernization directly impacts market positioning, customer satisfaction, and long-term viability.
The most forward-thinking operations leaders recognize that equipment upgrades represent investments in competitive differentiation rather than simply maintenance expenses. By understanding and communicating the comprehensive ROI potential of modern industrial equipment, these leaders position their organizations for sustained success.
For organizations still operating with aging equipment, the time for action is now. The quiet ROI of equipment modernization awaits those willing to look beyond immediate costs to embrace the transformative potential of technological advancement. Begin by auditing your current production line and identifying where modern equipment could deliver the greatest impact on your long-term competitive position and profitability. The equipment decisions made today will shape operational capabilities—and financial results—for years to come.
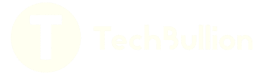