Recent statistics show that the global aerospace manufacturing industry was worth more than $850 billion USD in 2021. With a projected compound annual growth rate of 4%, that figure could grow to almost $1.4 trillion by 2030. If such projections are accurate, current and future aerospace part makers could see significant profits and expansion potential.
Success in this industry calls for a carefully devised strategy. When judiciously chosen, your metalworking tools help create an efficient and cost-effective aerospace manufacturing production environment. Advanced, well-designed solutions maintain the strict quality standards needed to produce flawless components to each client’s specifications.
Solutions for Successful Production in the Aerospace Industry
Aerospace manufacturing uses unique materials and processes, which all differ according to the part that’s being constructed. Every metal and allow has distinctive heat and electrical conductivity properties as well as densities, melting points and malleability properties. One notable example is aluminum, commonly in airframe construction. As it’s one of the softer metals, you need high-horsepower and high-speed tools for processes like cutting, milling and drilling.
Titanium alloys require special approaches. They’re heavily involved in making blades, roots, casings, discs, rings, beams, landing gear parts and even body components. Aerospace tooling and machining processes typically use two kinds of titanium alloys:
- Alpha-beta alloys: display high and moderate room temperature strength
- Beta alloys: Incorporating transitional metals for better heat treatability and greater strength
Machining tools must also take part sizes into account. For example, fabricating large-sized landing gear pieces may require long-reach tools. Engine casings have complex shapes, which may call for modular solutions that can combine multiple tooling processes in the same setup.
Create Custom Metal Working Tools
Metalworking tools can be combined in modular solutions. This approach is especially effective for parts with complex manufacturing processes. Modular tooling lets you use multiple adapters and tools on the same CNC machining workstation. It allows you to change out adapters and tools, plus it reduces your overall tooling costs.
Additive manufacturing is also relevant in aerospace parts production. You mostly think of 3D printing in the additive manufacturing world. However, machining and heat-treating are also vital parts of the process. AM applications are expanding to structural components, even including those composed of titanium and similar alloys.
For AM processes, these alloys are rendered into powder form. Stellite 6-AM-K powder is one example. This wear-resistant compound blends nickel, silicon, iron, manganese, chromium, molybdenum, tungsten and carbon. It excels in critical aspects such as corrosion resistance and high-temperature performance.
As an additive manufacturing supplier, Kennametal works with clients to create products from start to finish. Kennametal provides gas-atomized metal powders directly to clients for their own AM processes or in conjunction with Kennametal’s printing services. Other services include optimizing and prototyping client designs as well as end-to-end production, which incorporates post-print processing and tooling.
Multiple Approaches, Versatile Solutions
Aerospace manufacturing often involves traditional CNC machining and metalworking tools. Additive manufacturing is slowly making headway in the field, thanks to metal powders, sophisticated 3D printing solutions and post-print finishing. By partnering with Kennametal, you can develop manufacturing operations that best suit your firm’s needs.
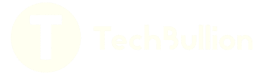