When it comes to construction and DIY projects, fasteners are a low-tech but high-importance component. Choosing the right fastener for the job can mean the difference between a successful project and a failure. In this article, we’ll discuss the key factors to consider when selecting fasteners and provide some tips for choosing the right fastener for the job. We will also delve into the different alloys of fasteners and compare their properties and suitability for various applications.
Factors to Consider
When selecting fasteners, there are several factors to consider, including:
- Type: There are many different types of fasteners available, including screws, bolts, nuts, and nails. Each type has its own specific use and is best suited for certain applications. For example, screws are good for holding materials together and can be easily removed, while bolts are better for high-stress applications and are more difficult to remove.
- Material: The material of the fastener is also important to consider. Different materials have different properties, such as strength, corrosion resistance, and cost. Some common materials for fasteners include steel, stainless steel, brass, and aluminum.
- Alloy: The alloy of the fastener can have a significant impact on its properties and suitability for certain applications. For example, steel fasteners are made up of iron and carbon, but other elements, such as chromium, nickel, and molybdenum, can be added to create different alloys with specific properties. Stainless steel fasteners, for example, contain a high percentage of chromium, which gives them good corrosion resistance.
- Size and strength: The size and strength of the fastener should be appropriate for the size and weight of the materials being fastened. Overly large or small fasteners may not provide the necessary support, while fasteners that are too weak may break under the
- Finish: The finish of the fastener can affect its appearance and performance. For example, a galvanized finish can provide additional corrosion resistance, while a polished finish can give the fastener a sleek, modern look.
Tips for Choosing the Right Fastener
Here are a few tips for choosing the right fastener for the job:
- Determine the purpose of the fastener: First and foremost, consider the purpose of the fastener. What are you trying to accomplish with the fastener? Are you trying to hold materials together, or are you trying to apply a load to the materials? This will help you determine the type and size of fastener that is best suited for the job.
- Consider the materials being fastened: The type and properties of the materials being fastened can also influence the choice of fastener. For example, if you are fastening materials that are prone to corrosion, you may want to choose a fastener made of a corrosion-resistant material, such as stainless steel.
- Think about the environment: The environment in which the fastener will be used can also impact the choice of fastener. If the fastener will be exposed to water, moisture, or other corrosive substances, you may want to choose a fastener with a high level of corrosion resistance.
- Follow manufacturer recommendations: If you are using a specific product or piece of equipment, be sure to follow the manufacturer’s recommendations for fasteners. These recommendations are designed to ensure that the fastener is suitable for the specific application and will provide the necessary support and strength.
Comparing Different Alloys
When it comes to choosing fasteners, the alloy of the fastener can be just as important as the material. Different alloys have different properties and are best suited for certain applications. Here is a comparison of some common fastener alloys:
- Carbon steel: Carbon steel fasteners are made up of iron and carbon. They are strong and durable, but they
- Stainless steel: Stainless steel fasteners are made up of iron, chromium, and other elements. They are often used in outdoor or marine environments, and highly resistant to corrosion. They are more expensive than carbon steel fasteners, but they are worth the extra cost in applications where corrosion resistance is a top priority.
- Brass: Brass fasteners are made up of copper and zinc. They are strong and resistant to corrosion, making them a good choice for outdoor or high-moisture environments. They are also non-magnetic, which can be an important consideration in certain applications.
- Aluminum: Aluminum fasteners are made up of aluminum and other elements. They are lightweight and corrosion resistant, making them a good choice for outdoor or high-moisture environments. However, they are not as strong as steel fasteners and are not suitable for high-stress applications.
Conclusion
In conclusion, choosing the right fastener for the job is essential for the success of any construction or DIY project. By considering the type, material, size, and finish of the fastener, as well as the purpose, materials being fastened, and environment, you can ensure that you are using the best fastener for the job. Don’t forget to consider the alloy of the fastener as well, as it can have a significant impact on the performance and suitability of the fastener for your specific application.
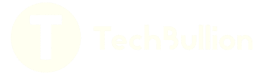